Im ersten Teil ging es um die ganze Theorie rund um Schraubverbindungen und warum das Drehmoment so wichtig ist. In diesem Teil gehen wir auf die Praxis und die Benutzung des Drehmomentschlüssels ein. Das Thema ist also: Welches Drehmonent-Werkzeug braucht ihr und wie werden Schrauben damit richtig angezogen.
Die Theorie, das was, wie und warum kennt ihr aus dem ersten Teil. Hier könnt ihr lesen, welches Werkzeug ihr braucht und wie ihr es richtig einsetzt. Ein guter, teurer Markendrehmomentschlüssel und die Sache ist geritzt, könnte man meinen. Ist das wirklich so einfach?
Leider ist dem nicht ganz so, aber eines ist sicher richtig: Es sollte ein guter Drehmomentschlüssel sein. Dennoch, in den im ersten Teil erwähnten Versuchen von AJAX und der NASA wurde ebenso festgestellt, dass die Fehlerquote mit einem Drehmomentschlüssel immerhin noch bei +/- 25% liegt. Wenn es richtig gemacht wird, wohlbemerkt! +/- 15% Genauigkeit wird mittels Festziehen nach Winkelangaben erreicht.
Ebenfalls wurde im ersten Teil aufgezeigt, warum der Montage so eine große Bedeutung zukommt zu. Nur der Monteur kann sich ein Bild über den Zustand des Materials machen und entsprechend darauf einwirken. Er entscheidet über das Werkzeug, dass er einsetzt und wie genau er damit umgeht. Die besten Schrauben und die sicherste Dimensionierung nützen nichts, wenn bei der Montage nicht sorgfältig gearbeitet wird. Deshalb kommen hier unsere Tipps für eine gute Montage.
Diese Tipps sind nicht auf jede einzelne Schraubenverbindung anzuwenden. In diesen beiden Artikeln geht im Wesentlichen um hoch-belastete und sicherheitsrelevante Schraubverbindungen. Dort wo ihr in der Regel Angaben zum Drehmoment findet.
Kurz rekapituliert
Fassen wir schnell noch einmal zusammen, was im ersten Teil stand. Die Klemmkraft, erzeugt durch die Schraube, ist das was eine geschraubte Verbindung sicher zusammenhält. Um diese Klemmkraft zu erhalten, muss eine Vorspannung, gemessen in kN (Kilonewton) in die Schraube eingebracht werden, wodurch sie sich längt und die Bauteile zusammenpresst. Um diese Vorspannung zu erhalten, müsst ihr ein Drehmoment einbringen, also die Schraube mit einer definierten Kraft anziehen. Das Drehmoment ist in Nm (Newtonmeter) angegeben. Von diesem Drehmoment bleibt jedoch nur ein schwer zu bestimmender Bruchteil übrig und erzeugt die Vorspannung. Der größte Teil geht als Reibung verloren. Durch Unterschiede in den Oberflächen, Material und Verarbeitung unterscheidet sich zudem bei mehreren gleichen Schrauben und gleichem Drehmoment die resultierende Vorspannung teils erheblich. Ziel ist es also, die Reibungsverluste gleichmäßig zu halten und eine möglichst gleichmäßige Vorspannung in allen Schrauben einer Bauteilverbindung zu erreichen. Diese Vorspannung muss zudem ein Mindestmaß erreichen, um ein selbstständiges Lösen der Verbindung zu verhindern und es darf ein Maximum nicht überschreiten, um die Schraubverbindung nicht zu beschädigen.
Das richtige Drehmoment-Werkzeug
Ganz klar, ein guter Drehmomentschlüssel ist notwendig. Wer sich auch an Zylinderköpfe oder andere Gewerke begibt, die ein möglichst genaues Einhalten des Drehmoments erfordern, benötigt zusätzlich die Möglichkeit den Drehwinkel zu messen. Das muss jetzt keiner der sehr teuren elektronischen Drehmoment-/Drehwinkel-Schlüssel sein, die bei 1.500 Euro aufwärts liegen. Es gibt günstigere Möglichkeiten für um die 100 Euro und weniger. Sogenannte Drehwinkelscheiben, sind für den privaten Einsatz in Ordnung. Bevor es die teuren elektronischen Schlüssel gab und wahrscheinlich auch noch heute werden diese Scheiben in vielen Werkstätten zu finden sein. Sie werden zwischen Schraube und irgendeinem Schlüssel gesetzt und zeigen einem dann den gedrehten Winkel an. Beispielsweise die Hazet Winkelscheibe.
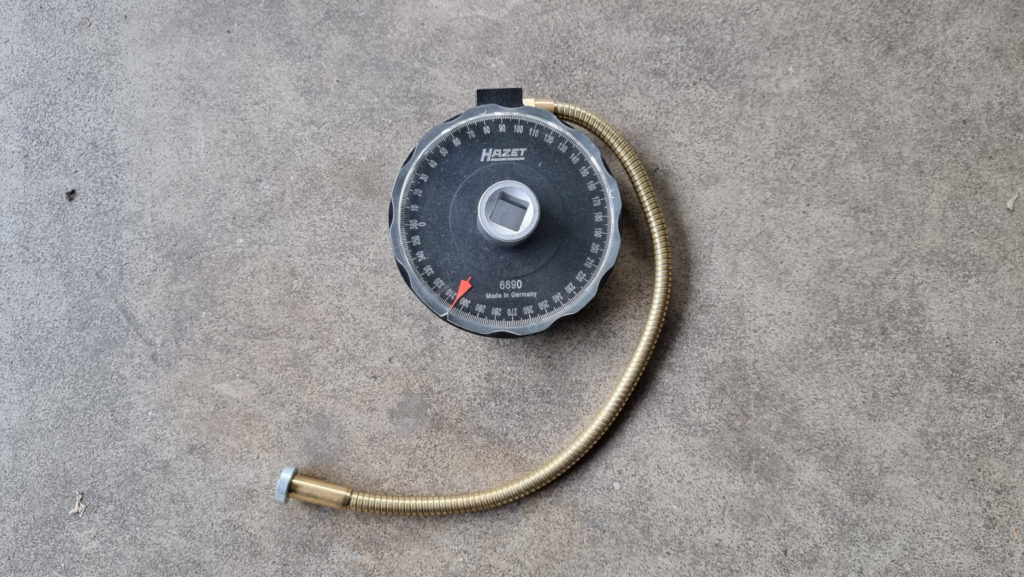
Ein Drehmomentschlüssel ist schon eine kleine Investition. Nehmt ihn daher vorher mal in die Hand und schaut ihn euch genauer an. Ist die Skala gut ablesbar und genau einzustellen? Oft finden sich dafür zwei Skalen. Eine die beispielsweise das Drehmoment nur in Zehnerschritten anzeigt und eine, die die Zwischenwerte angibt. Bei anderen zeigen beide Skalen in Ein-Newtonmeterschritten an, wobei die Skala am Griff zur Feinjustierung dient.
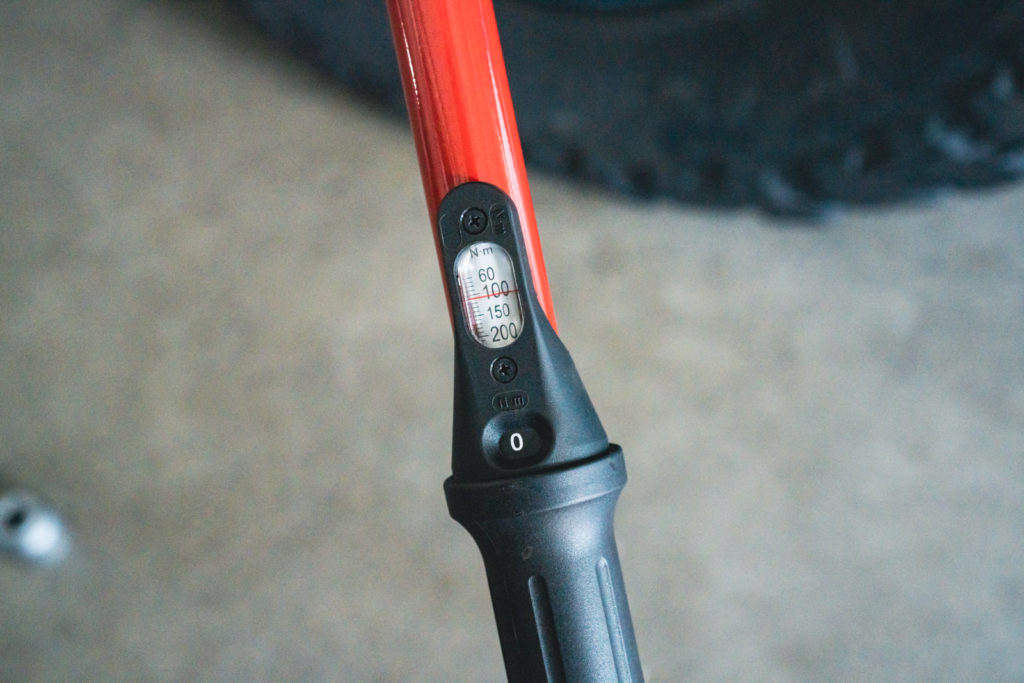
Gerade bei Fahrzeugen ausländischer Hersteller wird das Drehmoment in „Pfund-Kraft pro Fuß“ oder „Pfund-Kraft pro Zoll“ (lbf/ft oder lbf/in) angegeben. Manche Schlüssel können nach beiden Systeme eingestellt werden. Ansonsten hilft euch nur das Umrechnen, z.B. mit der Android-App „Unit Converter Pro“
Sinnvolle Drehmoment-Bereiche wählen
Bei der Auswahl des Drehmomentschlüssels sollte ein sinnvoller Bereich gewählt werden. Oder besser gesagt mehrere. Denn sowohl vom Drehmomentbereich als auch von der Größe her gesehen, gibt es nicht den einen universellen Schlüssel.
Viele mechanische Drehmomentschlüssel werden im unteren Drehmomentbereich ungenau, weil die Feder über die das Drehmoment eingestellt wird, dort nicht mehr linear arbeitet. Elektronische Schlüssel haben das Problem nicht, sind aber in der Regel teurer. Für den Fahrzeugbereich ist es daher sinnvoll, sich zwei oder drei Schlüssel zuzulegen. Für die großen Drehmomente eignen sich Schlüssel mit einem 1/2″-Kopf und ein Bereich von 60 bis 300 Nm. Für Arbeiten im Bereich des Motors sind dann kleinere Schlüssel mit 1/4″-Kopf und Bereichen zwischen 5 und 40 Nm gut geeignet. Wenn nötig, kann auch ein dritter Schlüssel für den mittleren Bereich sinnvoll sein.
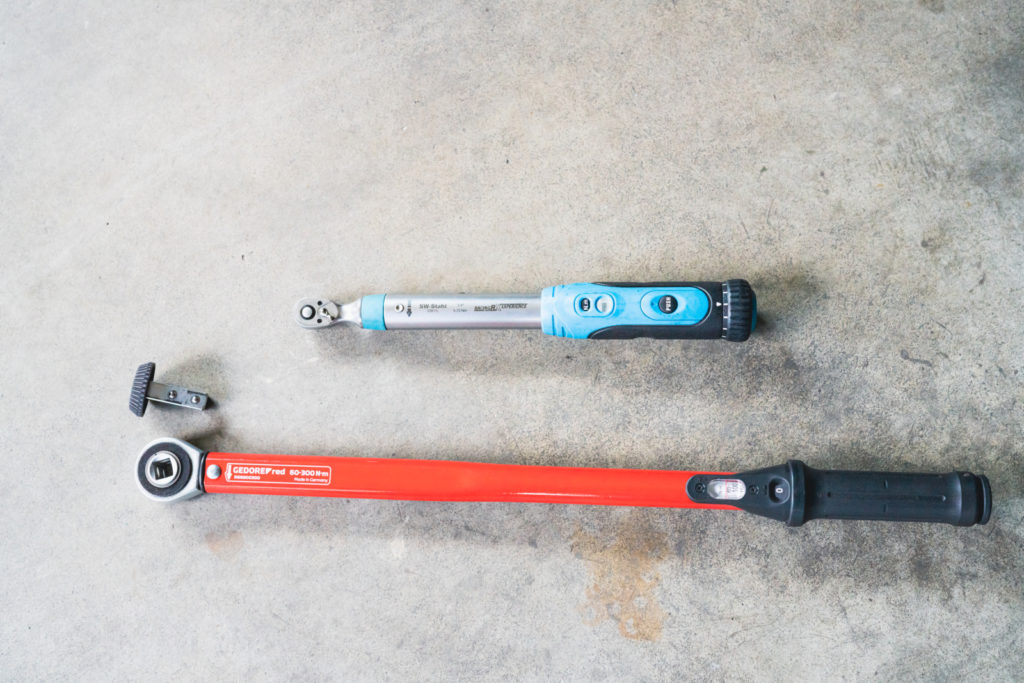
Der Drehmomentschlüssel ist kein Werkzeug, es ist ein Messgerät, insofern ist damit vorsichtig umzugehen. Er wird nur benutzt, wenn ein Drehmoment einzustellen ist und nicht zum allgemeinen Festziehen. Und auch nicht zum Lösen. Der Wechsel der Drehrichtung dient zum Anziehen von Schrauben mit Linksgewinde. Nach der Benutzung die Feder bei mechanischen Schlüsseln entlasten und ihn auf den geringst möglichen Wert, oder falls vorhanden, in die „Parkposition“ stellen. Es gibt einige Hersteller, bei denen der Drehmomentschlüssel nicht zurückgedreht werden muss, wie z.B. Hazet, aber es ist nie verkehrt sich das Rückstellen generell anzugewöhnen. Wer über lange Zeit gute Ergebnisse erzielen will, sollte ihn jedes Jahr oder alle 5.000 Lastwechsel kalibrieren lassen, so wie es in der DIN EN ISO 6789 gefordert wird..
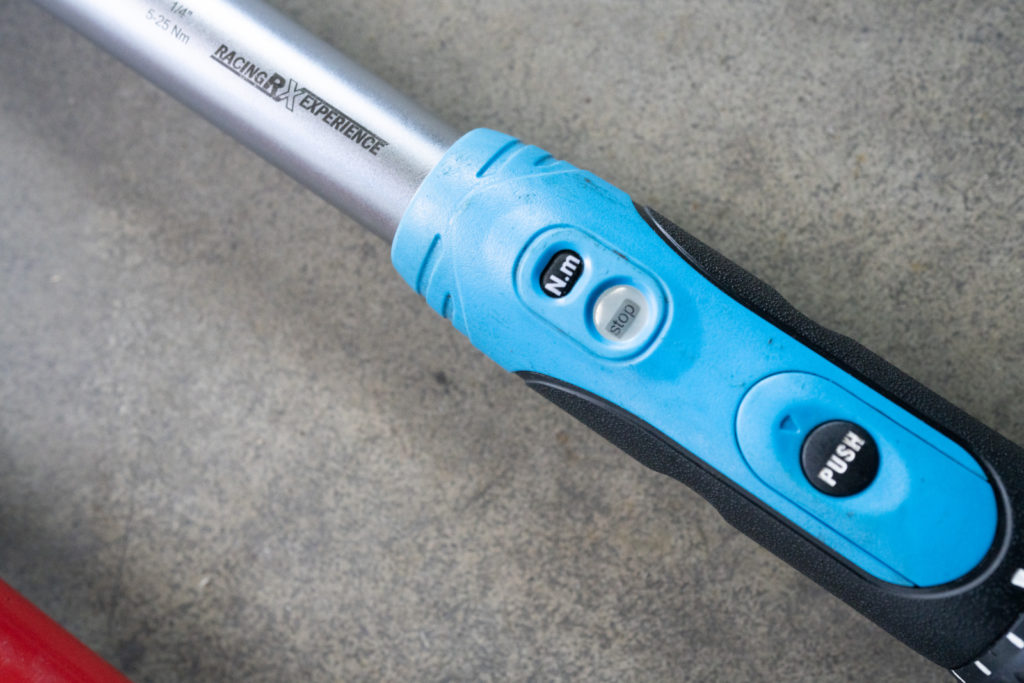
Präzision des Materials und der Bauteile
Je nachdem wie gut die Gewinde gefertigt wurden, kommt es zu mehr oder weniger Kontaktfläche, die für das Maß an Reibung mitverantwortlich ist. Die Unterschiede können in den Abständen und Form der einzelnen Gewindegänge, des Lochdurchmessers und der Tiefe liegen. Auch der Winkel, mit dem das Gewinde oder der Schaft für die Schraube gebohrt wurde hat Auswirkung. Denkt an die 50% Reibwirkung des Schraubenkopfes. Ist das Gewinde schräg zur Anpressfläche angelegt, liegt der Schraubenkopf auch nicht vollflächig auf und kann den geforderten Reibwiderstand nicht erzeugen.
Je genauer, sauberer und präziser die Gewinde sind, desto genauer kann das Drehmoment der Schraube erreicht werden.
Oberflächen
Schrauben kommen mit sehr unterschiedlichen Oberflächen. Sie sind in irgendeiner Form behandelt oder beschichtet worden, um sie vor Korrosion zu schützen oder sie zeigen schon deutliche Spuren eines langen Lebens. Das hat ebenfalls einen Einfluss auf die Reibung und das Spiel im Gewinde. Daher sollten alle Gewinde frei von Dreck, Rost und weiteren Materialien wie alte Sicherungslacke, Dichtmasse, Fett usw. sein.
Schrauben und Muttern bzw. Gewindelöcher entfetten (Bremsenreiniger), mit der Drahtbürste abbürsten und spülen, wenn möglich danach mit Druckluft frei- bzw. ausblasen. Lässt sich störendes Material nicht aus einem Gewindeloch entfernen, kann mit einem Gewindeschneider das Schraubenloch vorsichtig „saubergeschnitten“ werden. Das Ausblasen nicht vergessen!

Kleiner Schrauben-Hack
Habt ihr öfters alte Schrauben, die gereinigt und wieder schön gemacht werden sollen? Wenn ihr dann noch einen alten Exzenterschleifer und eine alte Plastikschüssel habt, könnt ihr euch schnell einen Schraubenreiniger bauen. Auch für andere Teile funktioniert das.
Befestigt die Plastikschüssel auf dem Exzenter. Arretiert dann den Schleifer und füllt Katzenstreu mit den Schrauben in die Schüssel. Eine Weile das Gerät laufen lassen und euer Material ist wieder blank.
Schraube vorbereiten
Benutzt eine Montagepaste für Schraubverbindungen oder ölt die Schraube ganz leicht ein. Das dient der Reduzierung der Reibung und ist ein Schritt, der verständlicherweise vielen widerstrebt. Im ersten Teil schreiben wir noch, dass die Schrauben sich keinesfalls selbst lösen sollen und jetzt schmieren wir etwas drauf, was die Reibung reduziert und ein Lösen wohl wahrscheinlicher macht. Die Befürchtung ist aber unbegründet.
Warum Schrauben geschmiert werden sollten
Gehen wir kurz darauf ein, wozu das Schmieren, neben der Vermeidung von Korrosion und dem besseren späteren Lösen, dient. An dieser Stelle möchte ich noch einmal auf John H. Bickford verweisen. Er schreibt in seinem Buch „An Introduction to the Design and Behavior of Bolted Joints“, dass die Reibung entscheident dafür ist, wie effizient und gleichmäßig die eingebrachte Kraft bei der Montage in die Vorspannung der Schraube umgesetzt wird. Damit ist Reibung ein entscheidender Faktor beim erreichen des geforderten Drehmoments und dafür, dass es bei mehreren Schrauben auch gleichmäßig erreicht wird.
Genauer gesagt spielt hier der Reibungskoeffizient eine Rolle. Normalerweise wird mit dem Gesamtreibungskoeffizienten µG gearbeitet, der sowohl die Reibung des Schraubenkopfes als auch des Gewindes wiederspiegelt. Trockene, rauhe Oberflächen haben einen höheren Reibungskoeffizienten als glatte und geschmierte. Je höher der Reibungskoeffizient ist, desto mehr Energie wird beim Eindrehen der Schraube zur Überwindung dieser Reibung verbraucht und desto weniger bleibt resultierend als Vorspannung in der Schraube zurück. Anders gesagt, je schwerer die Schraube einzudrehen ist, desto geringer ist die Vorspannkraft respektive die Klemmkraft bei erreichen des Drehmoments.
Abweichungen reduzieren
Bei einem Test wurden 280 M12 Schrauben bis zur Zugkraftgrenze eingedreht und das dafür notwendige Drehmoment gemessen. Die Hälfte der Schrauben wurden leicht geölt verwendet, die andere Hälfte entfettet und trocken eingesetzt. Bei den geölten Schrauben lagen die resultierenden Vorspannkräfte näher beieinander, wenn auch nicht extrem nah. Das war dem für diese Zwecke weniger geeignetem Öl geschuldet. Raymond Engineering, ein globaler Dienstleister für Industrie- und Infrastrukturprojekte, hat ähnliche Versuche an Dampfturbinen gemacht. Dabei wurde eine Paste auf Molybdändisulfid-Basis verwendet. Dort sah das Ergebnis schon sehr viel anders aus und die Vorspannkräfte der geschmierten Schrauben lagen sehr dicht beieinander, wohingegen die trockenen Schrauben eine große Streuung aufwiesen.
Andere Tests, von denen beispielsweise das Maschinenbaumagazin Schweizer Maschinenmarkt berichtet, kamen zu gleichen Ergebnissen. Dort wurde eine M12 8.8-Schraube mehrfach angezogen und dann die Vorspannung gemessen. Gemäß Richtlinie VDI 2230 (Verein Deutscher Ingenieure e.V.) sollen für diese Schraube im ungeschmierten Zustand bei 84 Nm Anzugsdrehmoment 43 kN Vorspannkraft erzeugt werden. Beim ersten Anziehen der ungeschmierten Schraube wurden 44 kN und beim vierten anziehen nur noch 19 kN Vorspannung erreicht, obwohl der Drehmomentschlüssel auf 84 Nm eingestellt war. Das ist dem Abrieb der Zinkoberfläche und der daraus resultierenden Erhöhung der Reibung zuzuschreiben. Das Ergebnis war also eine zunehmend geringere Vorspannung und Klemmkraft trotz gleichen Drehmoments.
Bei geschmierter Schraube hielt sich die Vorspannkraft auch nach mehrmaligem Anziehen nah an 40 kN. Da sich der Reibungskoeffizient reduziert, wird in der Tabelle der VDI 2230 nur noch 63 Nm Anzugsdrehmoment gefordert, um die gewollten 43 kN Vorspannkraft zu erreichen. Auch dieses Ergebnis zeigt, dass geschmierte Schrauben weniger Kraft in der Reibung verpuffen lassen und so besser die geforderte Vorspannung mit weniger Abweichungen zwischen den Schraubverbindungen erreicht wird, auch nach mehrmaligem Anziehen. Allerdings ist dann das Drehmoment ebenfalls zu reduzieren, da die Schraube sonst übermässig angezogen wird.
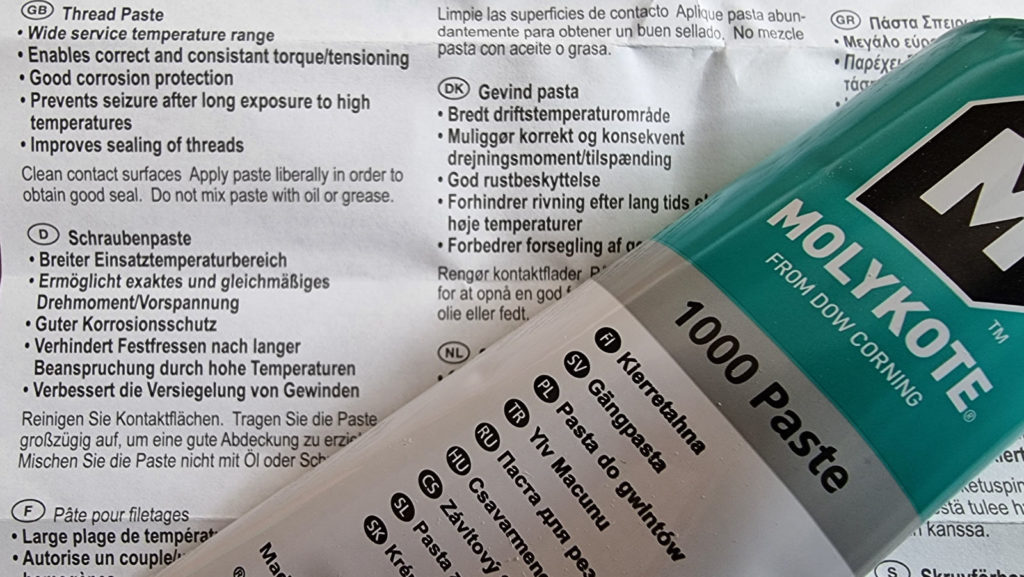
Widerspricht Einfetten nicht dem Ziel der Selbsthemmung?
Die Angst, dass geschmierte Schrauben sich lösen könnten, ist unbegründet. In der Industrie ist das Schmieren selbstverständlich, auch weil je nach Gewerk Schrauben sich in jedem Fall wieder problemlos lösen lassen müssen, was am zweiten positiven Effekt liegt: Korrosionsschutz. In Werstatthandbüchern findet sich üblicherweise die Anweisung, die hochbelasteten Zylinderkopfschrauben zu schmieren. Bei Edelstahlschrauben ist es sogar Pflicht mit passender Paste zu arbeiten, um ein Kaltverschweissen zu verhindern.
Neue vorgeölte Schrauben so einsetzen, oder wenn später ein Lösen leicht machbar sein soll Paste verwenden, da sich das Öl verflüchtigt. Trockene oder bereits verwendete Schraube neu schmieren. Bei kleinen Durchmessern und Feingewinde ein Sprühöl verwenden, bei größeren die entsprechenden Pasten für Schraubverbindungen. Die Schraube so einschmieren, dass die Paste gleichmäßig alle Rillen des Gewindes füllt. Auch unter dem Kopf sollte geschmiert werden, da er ja für ca. 50% der Reibung verantwortlich ist. Geht es um Edelstahlschrauben empfiehlt sich eine Paste auf Keramikbasis, z.B. das Liqui Moly Keramikspray oder die Paste. Nicht zu viel nehmen, überschüssiges Material abwischen.
Achtung! Keine allgemeinen Montagepasten oder Fette verwenden, die nicht explizit für Schraubverbindungen geeignet sind. Sie können die Reibung so stark reduzieren, dass die Schraube trotz korrekt eingestelltem Drehmoment überzogen wird. Gerade Hochleistungsfette können den Reibwert erheblich absenken. Vorschädigung, Abriss oder Gewindeschäden können die Folge sein.
Eine Montagepaste für Schrauben ist als solche deklariert und weißt auch Angaben zum Reibungskoeefizienten aus. Beispielsweise Molykote 1000 von DuPont.

Edelstahlschrauben und Muttern
Wenn ihr Edelstahlschrauben und Muttern verwendet, nutzt zwei unterschiedliche Edelstahl-Güten, z.B. A2 Schraube und A4 Mutter. Das reduziert die Gefahr des Kaltverschweissens. Trotzdem immer eine passende Schraubenpaste nutzen, wie oben bereits erwähnt.
Kaltverschweissen kann schon beim einfachen Aufdrehen der Mutter ohne jegliche Last auf die Verbindung passieren. Jeglicher Löseversuch macht es nur noch schlimmer. In der Regel muss die Schraube dann zerstört werden.
Drehmoment ermitteln
Entweder findet ihr das Drehmoment und die Anzugsreihenfolge im Werkstatthandbuch oder ihr müsst es selbst aus einer Tabelle wie der VDI 2230 ermitteln. Dazu müsst ihr das Material und die Oberfläche der Schraube gut kennen, um für sie den richtigen Reibungskoeffinzienten bestimmen zu können. Auch hier hilft das Einschmieren, denn es vereinheitlicht die Reibung. Schmiert ihr die Schraube ist der Wert einfacher aus dem Datenblatt zu entnehmen, wie beispielsweise 0,1 µG bei der Molykote 1000 Schraubenpaste.
In der Tabelle könnt ihr dann über den Nenndurchmesser und die Festigkeitsklasse das Anzugsdrehmoment ablesen. Einen Einblick in diese Tabelle bekommt ihr z.B. hier: Bossard.
Tests haben ergeben, dass für ungefettete, blanke Schrauben, also ohne Zinkschicht, der Reibungekoeffizient 0,1 µG sehr gut passt. Schaut man nun in die Tabelle der VDI 2230 findet man für genau diese Schraube ein Anzugsdrehmoment von 108 Nm für diesen Reibungskoeffizienten.
Für verzinkte Schrauben wird meistens 0,12 µG angesetzt. Dann wäre das Anzugsdrehmoment 123 Nm, bis die Zinkschicht weg ist.
Richtig anziehen
Das ist ein entscheidender Punkt. Kommen wir noch einmal kurz auf die Widerstände beim Festziehen zurück: gut 90% der Kraft geht durch Reibung verloren, davon ca. 40% im Gewinde und 50% unter dem Schraubenkopf, bzw. der Mutter.
Es spielen aber noch weitere Effekte hinein, die im Zusammenhang mit der Montage stehen. Zum einen, solange ihr Dreht habt ihr es mit kinetischer Reibung zu tun. Die ist geringer als die statische und auf die kinematische Reibung ist das Anzugsdrehmoment bezogen. Jeder kennt den Effekt: Wenn ihr etwas schiebt, ist es schwerer den Gegenstand in Bewegung zu setzen (statische Friktion), als ihn in Bewegung zu halten (kinetische Friktion). Das muss beim Anziehen berücksichtigt werden.
Das Drehmoment wird aus einer gleichmäßigen Drehung eingestellt, nicht aus der ruhenden Lage. Nur am Griff anfassen, nicht mit einer oder beiden Händen unterhalb des Griffs packen und auch nicht den Schlüssel verlängern! Am Griff sollte eine Markierung, z.B. eine Nut, sein. Das ist der Punkt, an dem beim Kalibrieren die Kraft eingeleitet wird. Dort solltet ihr mittig greifen. Im Bild ist die Markierung auf dem Griff gut zu sehen. Auf die Angabe der Drehrichtung des Schlüssels achten.
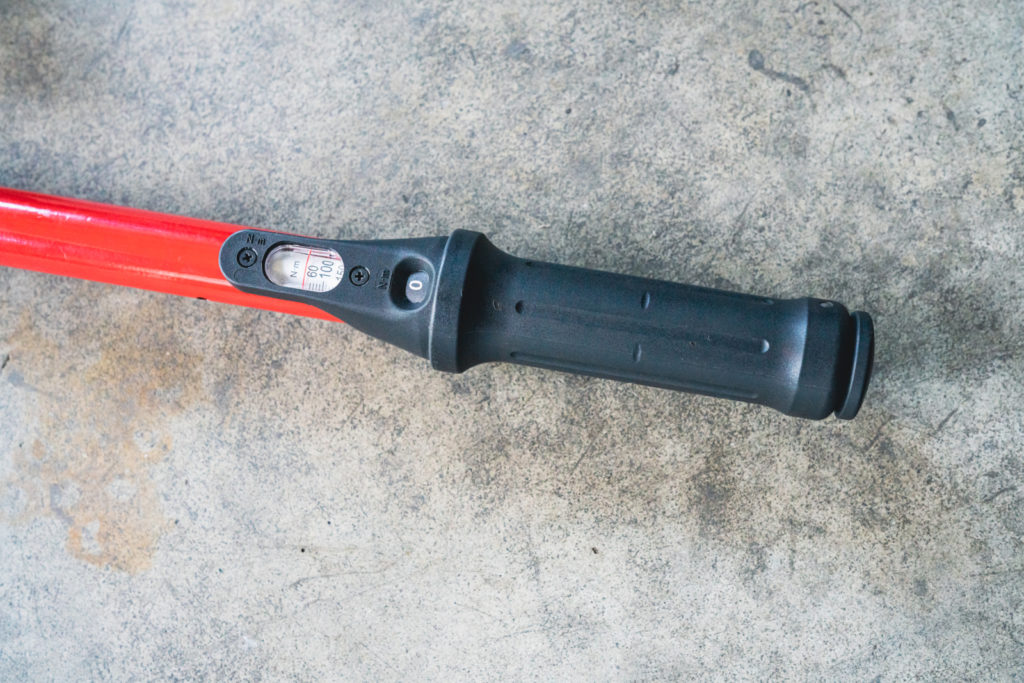

Warum genau am Griff angefasst werden muss
Auch wenn es zunächst komisch klingt, aber beim Drehmomentschlüssen wirken zwei Drehmomente. Das erste Drehmoment wird über den Hebel der Länge A erreicht. Dieser wirkt auf den Vierkant des Schlüssels und ist derjenige, den ihr nutzen wollt. Diesen Wert stellt ihr am Drehmomentschlüssel ein. Es ist aber nicht das Drehmoment, der tatsächlich am Klick-Mechanismus wirkt.
Auf den Klick-Mechanismus, der euch sagt das Drehmoment am Vierkant ist erreicht, wirkt das Drehmoment des Hebels mit Länge B. Da das Drehmoment bei gleicher Kraft bei einem längeren Hebel größer ist als bei einem kleineren, ist also das Drehmoment am Vierkant immer größer als das am Klick-Mechanismus.
Möchtet ihr also 100 Nm am Vierkant erreichen, muss der Klick-Mechanismus schon bei einem kleineren Drehmoment auslösen, sagen wir einmal bei 90 Nm. Diese Differenz ist mechanisch vom Hersteller unveränderlich eingestellt und zu 100% abhängig vom Verhältnis der beiden Hebellängen!
Der Klick-Mechanismus ist also mechanisch auf die Kräfte ausgeleget, die das Verhältnis der Längen Hebel A zu Hebel B bewirken. Bei Hebellängen von der Griffmarkierung zum Vierkant von 500 mm und 450 mm zum Klick-Mechanismus ist das ein Verhältnis von 1,1:1. Die Kraft am Vierkant ist also um den Faktor 1,1 größer als am Klick-Mechanismus. Wieder anders gesagt, liegen beim Vierkant die gewünschten 100 Nm an, klickt der Mechanismus schon bei 90 Nm.
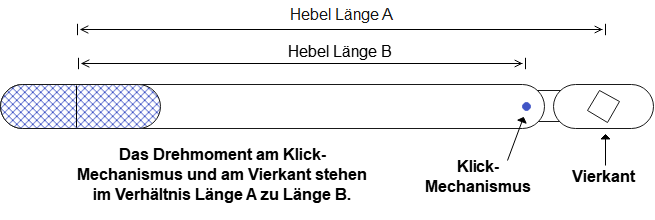
Verkürzt oder verlängert ihr Hebel B durch Umgreifen, passt das in der Mechanik eingestellte Verhältnis nicht mehr zu dem neuen Verhältnis der Hebellängen. Verkürzt ihr beispielsweise vom Griff unseres Beispiels auf 300 mm, verändert sich das Verhältnis zu 1,6:1. Bei unserem Beispiel würdet ihr, wenn der Klick-Mechanismus bei 90 Nm auslöst am Vierkant 160 Nm anliegen haben. Umgekehrt, verlängert ihr den Hebel, zieht ihr mit zu wenig Drehmoment an.
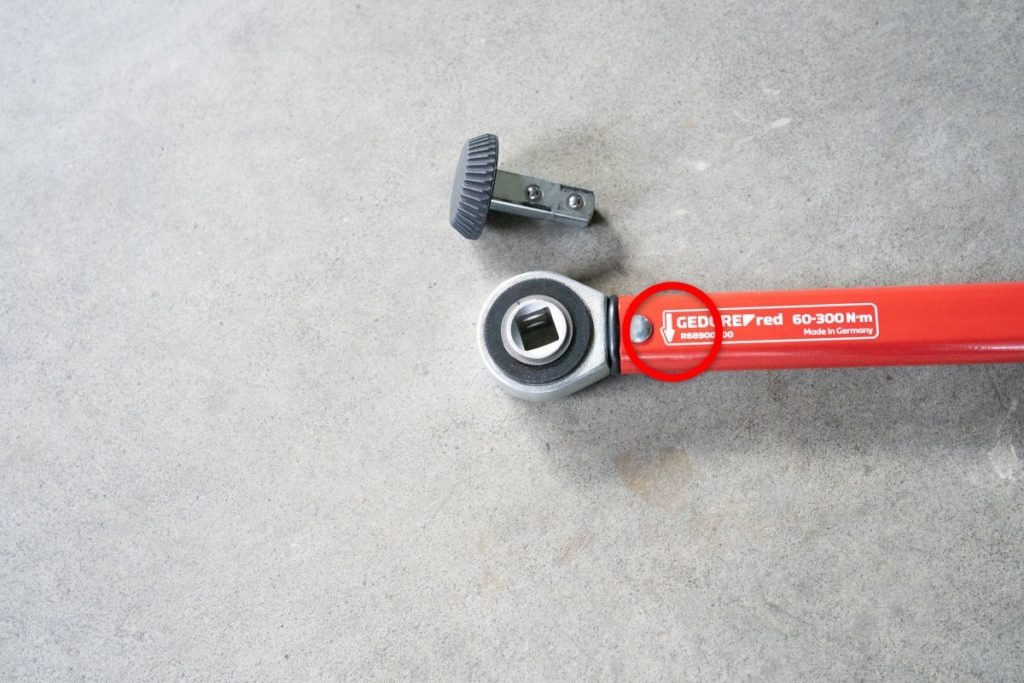
Was in einem gewissen Rahmen kein Problem darstellt ist eine Verlängerung für die Nuss, beispielsweise wenn ihr sonst nicht an Felge und Reifen vorbeikommt, um die Radmutter anzuziehen. Zu lang sollte die Verlängerung aber auch nicht sein, gerade wenn sehr hohe Drehmomente gefordert werden, da dann wieder Torsionsverluste in der Verlängerung auftreten und generell die Handhabung schwieriger wird.
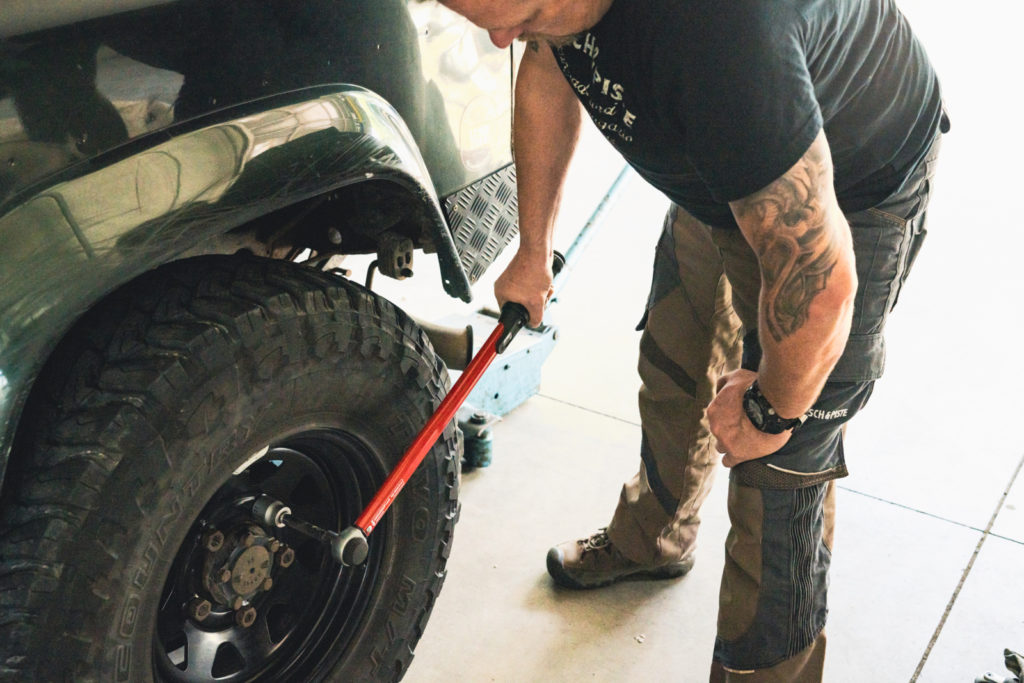
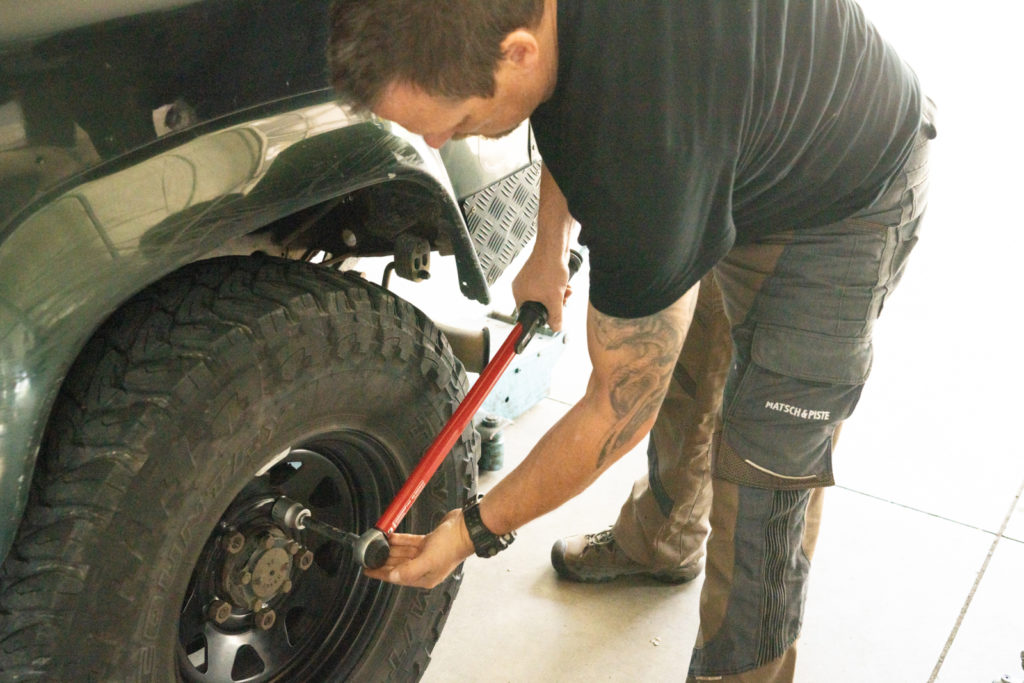
Dann wäre da noch der erwähnte Einschleifprozess, gerade bei neuen Schrauben und das Setzen der Teile, insbesondere wenn mehrere Schrauben zum Einsatz kommen.
Gerade bei hochfesten oder neuen Schrauben/Muttern in mindestens drei Durchgängen alle Schrauben in der vorgegebenen Reihenfolge anziehen:
- 1. Auf 2/3 des Drehmoments anziehen.
- 2. Auf das geforderte Drehmoment anziehen.
- 3. Dann 1/4 bis 1/2 Umdrehung zurück und dann wieder mit dem geforderten Drehmoment anziehen.
Selbstverständlich gilt: Gibt der Hersteller die Durchgänge mit den entsprechenden Drehmomenten vor, diesen Angaben folgen.
Die Reihenfolge beim Anziehen mit dem Drehmomentschlüssel
Wird die Verbindung von mehreren Schrauben gehalten, gibt es oft eine Reihenfolge, in der angezogen wird. Daran solltet ihr euch halten. Der Klassiker hier ist das Rad. Daran lässt sich das Grundprinzip einer Anzugsreihenfolge gut zeigen. Die Reihenfolge dient zur Unterstützung der Setzprozesse und um Verkantungen zu verhindern.
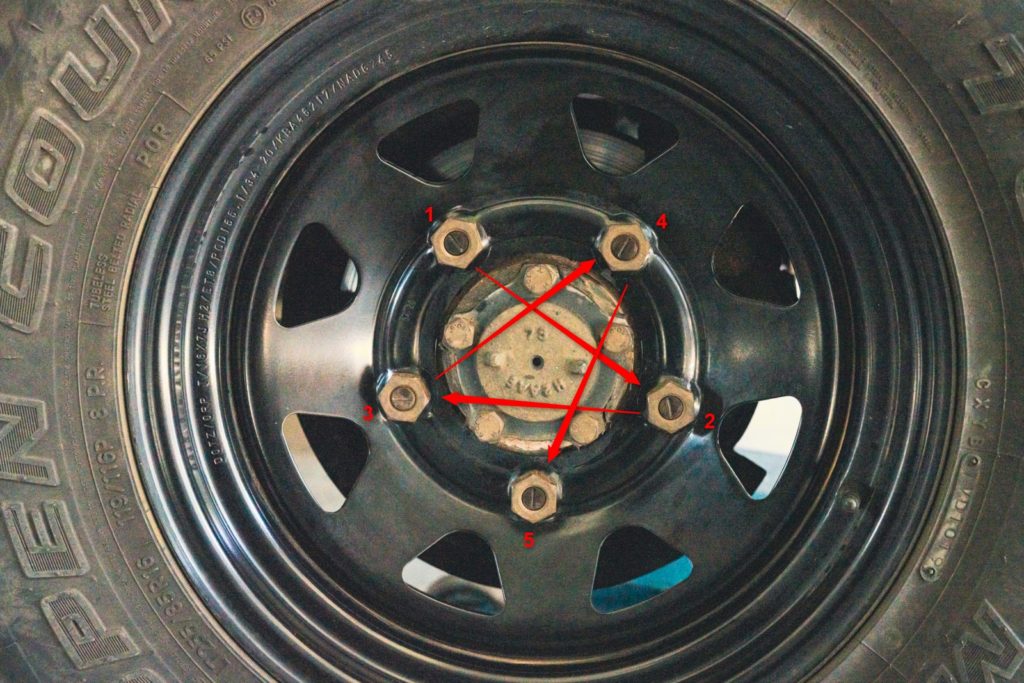
Die Reihenfolge in Bildern
Die kleine Bilderreihe zeigt den grundsätzlichen Vorgang. Je nach Verbindung ist es empfehlenswert, wie oben beschrieben, noch einmal zurückzudrehen oder in mehreren Durchgängen anzuziehen.
Spätere Überprüfung
Zuletzt kommt noch die Nachsorge. Gerade bei hochbelasteten und sicherheitsrelevanten Verbindungen sollte nach einiger Zeit der richtige Sitz der Schrauben nochmals überprüft werden. Wir kennen das vom Reifenwechsel, wenn auf der Rechnung des Reifenhändlers steht, dass nach 50 km die Radmuttern noch einmal überprüft bzw. nachgezogen werden sollen.
Weitere Informationsquellen
In diesem Video der Firma Ludwig Meister GmbH & Co. KG wird der Einfluss von geschmierten Schrauben auf die erreichte Vorspannkraft gemessen und dargestellt: Festsitzende Schrauben vermeiden: Schrauben richtig schmieren und anziehen.
Wer sich weiter Informieren oder in das Thema eintauchen möchte, dem sei diese (englischsprachige) Literatur empfohlen:
- Das NASA-Design-Manual für Schrauben: Fastener Design Manual
- AJAX Schrauben-Handbuch: AJAX Fastener Manual
- John H. Bickfords Werk zu allen Apsekten rund um Schrauben: An Introduction to the Design and Behavior of Bolted Joints
Wir danken Herrn Simon Mayer von der Firma Ludwig Meister GmbH & Co. KG, der uns bei der Erstellung dieses Artikels beraten hat. Die Ludwig Meister GmbH & Co. KG ist ein Vollsortimenthändler für Antriebstechnik, Werkzeugtechnik und Fluidtechnik.