Wieder eine Fehlermeldung im Display? Der Motor ist gerade in den Notlauf gegangen? Oft stehen diese Dinge im Zusammenhang mit den Motor- oder Abgassensoren. Sei es weil sie ein Problem entdeckt haben oder selbst das Problem sind. Daher werden sie gerne verflucht, sind aber in modernen Motoren unverzichtbar. Welche Sensoren es gibt, wozu sie da sind, wie sie funktionieren und für welche Fehler sie verantwortlich sein können könnt ihr hier nachlesen.
Unser Fahrzeugpark erstreckt sich von 1971 bis 2024. Wir können über diesen Zeitraum von über einem halben Jahrhundert gut nachvollziehen, wie die elektronische Fahrzeugsteuerung sukzessive Einzug hielt. In unseren Fahrzeugen vor den 1980er Jahren gibt es nicht einmal elektrische Sensoren. Temperatur und Druck werden noch direkt über Kapillarleitungen an die Anzeige gegeben, die Geschwindigkeit per drehender Welle an den Tacho übertragen. Die einzige Ausnahme ist der Tanksensor, der schon elektrisch funktioniert. Mitte bis Ende der 1980er kamen dann Benzin-Einspritzer mit elektronischen Steuergeräten. Für den amerikanischen Markt mussten jetzt bestimmte Abgaswerte eingehalten werden. Dort finden wir nun schon die ersten Motorsensoren, die Motorstellung, Luft und Temperatur überwachen.
Unser Fahrzeug aus den frühen 2000er Jahren besitzt nicht viel mehr Sensoren als diese älteren Fahrzeuge und auch nur einen einzigen Sensor (Kurbelwellensensor), der den Motor wirklich stilllegen kann. Aber die strengeren Abgasnormen verlangen eine zunehmend engere Überwachung und erfordern bereits eine elektronische Steuerung der Einspritzung. Es gesellen sich Kraftstoff-, Kühlmittel- und Ansauglufttemperatur als Eingangssignale für die Steuerung dazu.
In den Fahrzeugen von Mitte der 2010er Jahre bis heute ist dann das volle Programm zu finden. Dieselpartikelfilter, Katalysator und weitere Abgasnachbehandlungssysteme sowie elektrische Motorkühlung brauchen die ganze Palette an Mess- und Regeltechnik, denn das ist es letztendlich: Messen & Regeln.
Die Sensoren sind die Augen und Ohren der Elektronik. Ohne die Sensoren kann sie nicht Motor und Zusatzaggregate steuern. Darauf wollen wir uns hier auch beschränken, den Motor und das Abgassystem, welches dazu gehört. Denn wenn alle Sensoren aufgezählt werden würden, die es ansonsten außerdem im Auto gibt, würde die Liste schier unendlich werden.
Ich habe ein geteiltes Verhältnis zu dieser Technik. Lassen wir den Umweltaspekt einmal außen vor und sehe ich mir meinen Land Rover Td5 Motor von 2002 mit Steuergerät an, so finde ich das sehr gelungen. Nur mittels der elektronischen Steuerung sind mehr Leistung, weniger Verbrauch und bessere Abgaswerte möglich. Auf der anderen Seite bedarf es nur eines funktionierenden Sensors, damit der Motor läuft. Die Elektronik schützt sogar, wie ich aus eigener Erfahrung weiß. Unbemerkt wurde der Motor des öfteren zu heiß und die ECU setzte ihn in den Notlauf, was einen Schaden vermied. Das kann nicht schlecht sein. Ohne die ECU wäre es vielleicht zu spät aufgefallen. Bei dieser Generation Fahrzeug sage ich noch, ein Steuergerät ist leichter zu tauschen als ein Differential zu reparieren ist.
Aber in den Fahrzeugen der letzten zwei Jahrzehnte finde ich, dass es zu viele Abhängigkeiten und zu viel Komplexität gibt. Aber hier greift vielleicht der Status-quo-Bias-Effekt: Jede Generation akzeptiert den Status-quo und zieht ihn Veränderungen vor. Somit schleichen sich diese Dinge ein, werden akzeptiert und gelten von nun an als normal.
Einführung in die Thematik
Ein aktuelles Fahrzeug bringt es locker auf 50 bis 60 Sensoren und mehr.
Eine Klassifizierung der Sensoren sieht wie folgt aus (in Klammern die übliche Anzahl):
- Positions- und Winkelsensoren (11)
- Drehzahlsensoren (5)
- Schwingungssensoren/Gyrometer
- Durchflusssensoren(1)
- Beschleunigungs – und Vibrationssensoren (7)
- Drucksensoren (22)
- Temperatursensoren (viele)
- Drehmomentsensor
- Kraftsensoren
- Konzentrationssensoren(2)
- Optoelektronische Sensoren (2)
Die meisten Sensoren finden sich im Bereich der Motorsteuerung, primär für die Abgasreduzierung und Nachbehandlung. Sie messen Zustände, überwachen sie, regeln nach und ggf. alarmieren sie auch. Hier soll es um diese Sensoren gehen. Sie sind im Folgenden in die o.a. Kategorien eingeteilt und es wird erklärt wie sie funktionieren. Manche Sensoren haben sich weiterentwickelt, sind präziser und robuster geworden (z.B. beim Wechsel von Potentiometern auf Hall-Sensoren) oder es sind mehrere Prinzipien parallel im Einsatz.
Nicht jeder Sensor findet sich in jedem Auto und gerade bei der Abgasnachbehandlung können unterschiedliche Verfahren im Einsatz sein, die auf unterschiedliche Arten geregelt und überwacht werden. Grundsätzlich lässt sich aber klar der Trend aufzeigen, dass mit steigenden Anforderungen an die Abgasnachbearbeitung die Sensorik deutlich zugenommen hat, um die Regelung noch enger und genauer zu fassen.

DTC Fehlercodes
Im Folgenden geben wir die DTC Fehlercodes zu den einzelnen Sensoren an. Das sind neben den herstellerspezifischen Codes einheitliche Fehlernummern, die über die OBD-Schnittstelle ausgelesen werden können, z.B. mittels eines OBD2-Adapters. Es existieren derzeit ca. 11.000 Fehlercodes, die in den Normen SAE J2012 und ISO 15031-6 definiert sind.
Die Fehlercodes sind in Obergruppen eingeteilt:
Der erste Buchstabe steht für die DTC-Familie:
- P: Powertrain / Antriebsstrang – Dazu zählen Motor und Getriebe
- C: Chassis / Fahrgestell
- B: Body / Karosserie
- U: User Network / fahrzeugnetzwerk
Auf den Buchstaben folgt die erste Zahl, die die weiteren Stellen in allgemeine oder herstellerspezifische Fehler unterteilt.
- 0: Allgemeiner Fehler
- 1: Herstellerfehler
Die letzten drei Stellen führen dann zu dem einzelnen betroffenen System. Das können hexadezimale Zahlen sein, die von 0 bis 9 und dann von A bis F gehen.
- 0, 1, 3: Luft- und Kraftstoff Dosierung
- 3: Zündung
- 4: Emissionskontrolle
- 5: Motorleerlaufsteuerung
- 6: ECU
- 7, 8, 9: Getriebe
- A, B, C: Hybridantrieb
Drehzahlsensoren
Kurbelwellensensor
Einer der wichtigen Sensoren ist der Kurbelwellensensor. Er teilt dem Steuergerät mit, wie die Kurbelwelle steht und welche Drehzahl sie hat. Was er nicht wissen kann ist, wann welcher Kolben gezündet werden muss, also gerade im Kompressionstakt auf dem Weg zum Arbeitstakt ist. Das liegt daran, dass bei einem Viertaktmotor zwei Kurbelwellenumdrehungen für alle vier Takte nötig sind. Der Kurbelwellensensor weiß dann zwar, wann eine Umdrehung abgeschlossen ist, aber nicht, ob diese Umdrehung nun beispielsweise den Kolben „1“ in Zündposition bringt oder doch der Ausstoßtakt dran ist. Bei beiden Takten geht der Kolben von unten nach oben, aber welcher Takt nun folgt, kann der Sensor nicht melden.
Bei Motoren, wie beispielsweise einem Pumpe-Düse-Motor, bei dem eine mechanisch mit der Kurbelwelle verbundenen Nockenwelle entscheidet wann und welche Düse einspritzt, reicht der Kurbelwellensensor aus. Er gibt die Drehzahl an und hilft bei der Berechnung der Einspritzlänge. Welche Düse wann einspritzt, ist mechanisch über die Nockenwelle für die Pumpenelemente geregelt.
Motoren, die den Zünd- oder Einspritzzeitpunkt nicht mechanisch gekoppelt sondern nur elektronisch regeln, benötigen einen weiteren Sensor, um zu wissen wann welcher Zylinder zur Zündung ansteht: den Nockenwellensensor. Nur so kann das Steuergerät den richtigen Zünd- bzw. Einspritzzeitpunkt für die einzelnen Zylinder ermitteln.
Kurbelwellensensoren sind in zwei Varianten vorzufinden. Entweder als Hall-Effekt-Sensor, zu erkennen an drei Anschlusskabeln, oder als Magnetwiderstand mit zwei Kabeln. Dem Sensor gegenüber dreht sich ein Zahnrad, dem ein Zahn fehlt. Durch die regelmäßige Anordnung der Zahnräder kann der Sensor überhaupt erst feststellen, dass der Motor dreht und was die aktuelle Drehzahl ist. Der fehlende Zahn löst dann ein Signal aus, das der ECU eine bestimmte Position mitteilt. Das ist üblicherweise Kolben Zylinder 1 am oberen Totpunkt (OT). Das Signal des fehlenden Zahns kann auch wie ein regelmäßiges Zurücksetzen, ein Synchronisationspunkt, gesehen werden.
Das Geberrad muss irgendwo mit der Kurbelwelle verbunden sein und mit ihr drehen. Der Sensor muss nah am Geberrad liegen. Das Ganze findet sich entweder am Schwungrad, an der Riemenscheibe der Kurbelwelle oder an ihrem Steuerketten bzw. Riemenrad, das normalerweise hinter dem Steuergehäusedeckel sitzt. Es lohnt sich in jedem Fall diesen Sensor als Ersatzteil mitzuführen.
Übliche Fehlersymptome sind:
- Motor startet nicht oder geht nach dem Start sofort wieder aus
- Fehlzündungen
- Ruckelige Beschleunigung
- Unruhiger Leerlauf
- Erhöhter Verbrauch
Typischer Fehlercode: P0335
Nockenwellensensor
Da die Nockenwelle mit halber Geschwindigkeit der Kurbelwelle dreht, entspricht eine Umdrehung allen vier Arbeitstakten. Daher weiß der Nockenwellensensor genau, wo jeder Kolben steht und welches der nächste Takt für ihn ist. Er bestimmt über den Zünd- bzw. Einspritzzeitpunkt. Zudem können über ihn Werte des Kurbelwellensensors validiert werden. Ist die Nockenwelle verstellbar sind oft mehrere Sensoren vorhanden, ansonsten reicht einer.
Technisch funktioniert der Nockenwellensensor wie der Kurbelwellensensor. Der Sensor ist in der Nähe der Nockenwellen zu finden, üblicherweise im Ventildeckel oder dem Steuergehäusedeckel. Mit Hall-Sensoren lässt sich sofort beim Einschalten bereits die Position genau bestimmen, es bedarf keiner Drehung um zunächst die Position zu ermitteln.
Übliche Fehlersymptome sind:
- Motor startet nicht oder schlecht.
- Fehlzündungen
- Ruckelige Beschleunigung
- Unruhiger Leerlauf
- Erhöhter Verbrauch
Typischer Fehlercode: P0340
Positions- und Winkelsensoren
Drosselklappensensor
Egal ob die Drosselklappe noch mechanisch oder elektrisch gestellt wird, ihre Position sagt dem Steuergerät etwas über die aktuelle Last. Die Drosselklappe bestimmt den möglichen Luftdurchfluss zu den Zylindern (nicht den tatsächlichen). Je weiter sie offen ist, desto mehr Luft kann in die Zylinder strömen. Wenn ihr 80 km/h ohne Anhänger fahrt, drückt ihr das Gaspedal weniger durch um die Geschwindigkeit zu halten als wenn ihr einen Anhänger mit 2 Tonnen zieht. Das gibt der ECU einen Rückschluss über die zu bewältigende Last.
Der Drosselklappensensor ist ein einfacher Potentiometergeber, also ein veränderbarer Widerstand. Je nach Stellung wird die eingehende Spannung reduziert und wieder ausgegeben. Die Spannungshöhe sagt dann der ECU wie der Öffnungsgrad der Klappe ist.
Der Sensor sitzt immer an der Drosselklappe. Die Drosselklappe ist zwischen Luftfilter und Ansaugbrücke zu finden. Durch sie muss der gesamte Luftstrom hindurch, weshalb sie meistens nah am Motor kurz vor der Auffächerung zu den einzelnen Zylindern angeordnet ist. Die Klappe hat eine Welle über die sie gestellt wird. Diese Welle ist mechanisch mit dem Gaspedal oder mit einem elektrischen Stellglied verbunden, das vom Gaspedal gesteuert wird. Der Potentiometergeber ist ebenfalls mit der Welle verbunden und wird von ihr gedreht. In modernen Fahrzeugen, bei denen die Drosselklappe elektrisch gestellt wird, ist der Sensor in das Stellglied integriert.
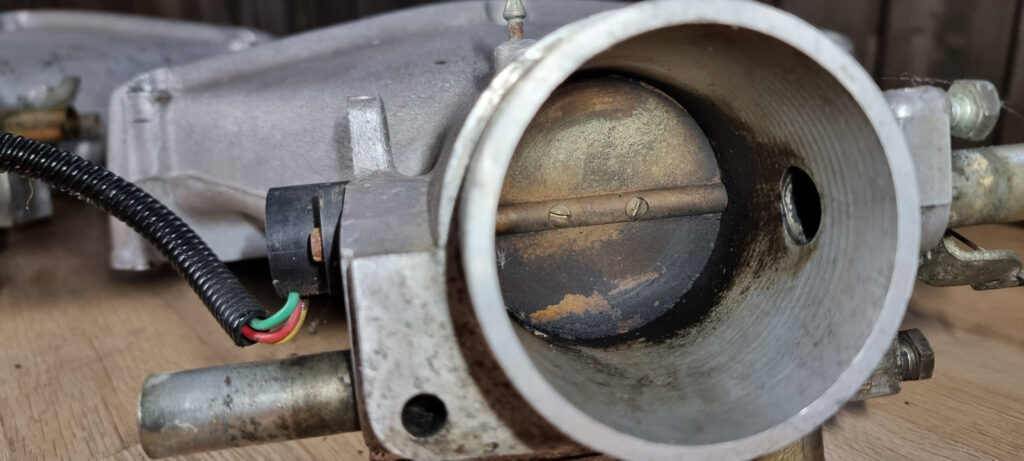
Übliche Fehlersymptome sind:
- Ungewollte Beschleunigung
- Schwerer Motorstart
- Leerlauf zu niedrig oder zu hoch
Typische Fehlercodes: P0122, P2135.

Dieselmotoren und Drosselklappen
Jetzt mag sich der eine oder andere gefragt haben, wieso es bei einem Dieselmotor eine Drosselklappe gibt? Kurz für diejenigen, die das nicht einordnen können: Ein Benzinmotor wird über die Drosselklappe gesteuert. Wenn ihr Gas gebt, macht ihr die Drosselklappe auf und mehr Luft kann in den Zylinder gelangen. In Folge beschleunigt der Wagen. Bei einem Diesel steuert ihr mit dem Gaspedal zur Beschleunigung aber die Einspritzung, nicht die Luft. Und dennoch habe Dieselmotoren Drosselklappen.
Die Drosselklappe hat bei Dieselmotoren aber erst mit der Abgasrückführung Einzug gehalten. Sie erzeugt mehr oder weniger Unterdruck, der zur Steuerung des AGR-Ventils benötigt wurde, als diese noch unterdruckgesteuert waren. Heute geschieht das alles über elektrische Stellglieder und die Drosselklappe steht beim Diesel fast die ganze Zeit komplett offen. Sie dient nur noch ein wenig dem leiseren Motorlauf im Standgas und im Schubbetrieb, als auch dem sauberen Abstellen des Motors. Dann gibt es noch den Fall, das jeder Zylinder zwei Lufteinlassöffnungen im Zylinderkopf hat, von denen jeweils eine eine Klappe besitzt, die auf und zu gemacht werden kann. Der Unterdruck für diese Steuerung kommt auch von der Drosselklappe.
Fahrpedalsensor
Der Fahrpedalsensor ersetzt den Seilzug oder davor noch das Gestänge über den vormals mechanisch die Drosselklappe im Vergaser oder der Stellhebel an der Diesel-Einspritzpumpe betätigt wurde. Der Fahrwunsch des Fahrers wird über Potentiometer ermittelt, die durch das Treten des Pedals gestellt werden. Um Fehler auszuschließen werden zwei gegenläufige Potentiometer zur Validierung des Signals verwendet. Beim Treten des Pedals wird durch das eine Potentiometer die Spannung reduziert während beim anderen in gleichem Maße die Spannung erhöht wird. Dadurch bleibt die Kontrollspannung bei korrekter Funktion immer auf Höhe des Eingangssignals. Das Eingangssignal liegt üblicherweise bei 5 V und beide Signalspannungen müssen in Summe immer 5 V ergeben. Dann sind die Signale korrekt und die Pedalstellung kann einwandfrei erkannt werden.
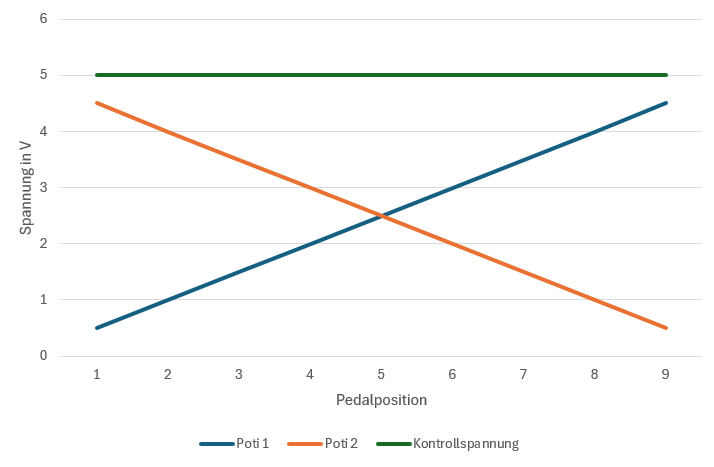
Da Potentiometer Schleifkontakte sind, unterliegen diese einem mechanischen Verschleiß. Deshalb wurden diese durch kontaktlose Hallsensoren ersetzt, bei denen ein Rotor gegenüber einer Spule bewegt wird und so ein Signal erzeugt.
Durch die mechanische Entkopplung des Fahrpedals von der Drosselklappe, kann das Steuergerät auch unseren Fahrwunsch übersteuern. Unser Wunsch wird nicht mehr direkt und unmittelbar übertragen, sondern an das Steuergerät übergeben. Hat dieses beispielsweise den Motor in den Notlauf versetzt, ignoriert es unseren Wunsch und begrenzt die Drehzahl, egal wie weit wir das Pedal durchtreten. Auf die Art kann auch die Drehzahl nach oben begrenzt werden oder in kritischen Fahrsituationen die Beschleunigung nicht so erfolgen wie vom Fahrer erwünscht.
Durch den Einsatz elektronischer Fahrpedale erfolgt zudem eine Glättung. Bei einer mechanischen Verbindung, insbesondere bei einem Gestänge, wirken Motorbewegungen und leichte Fußbewegungen direkt auf die Drosselklappe. Bei Vergasern kann das den Verbrauch steigern, da diese eine Pumpe haben, die zusätzlich Sprit in den Ansaugtrakt pumpt, wenn das Pedal getreten wird, um kurzfristige Leistungsanforderungen zu ermöglichen. Bei einem elektronischen Signal kann das Steuergerät diese unerwünschten kleineren Bewegungen aus dem Signal herausnehmen und es so glätten. Der Motorlauf wird dadurch beruhigt und sparsamer.
Übliche Fehlersymptome sind:
- Keine Gasannahme
Typische Fehlercodes: P0120 bis P0124, P0220 bis P0229.
Durchflusssensoren
Luftmassenmesser (MAF)
Während der Nockenwellensensor dem Steuergerät sagt wann zu zünden oder Treibstoff einzuspritzen ist, sagt der Luftmassensensor wie viel es sein muss. Das Steuergerät versucht immer die richtige Menge Kraftstoff zur Luftmenge zu geben, um das jeweilige beste Verhältnis je nach Last und Treibstoffart zu geben. Um die Luftmenge zu kennen, wird der Luftmassensensor benötigt.

Stöchiometrisches Verhältnis
Um die bestmögliche Verbrennung zu erzielen, muss ein bestimmtes Verhältnis (Lambda λ) von Luft zu Kraftstoffmolekülen hergestellt werden. Das ideale Verhältnis nennt sich das „stöchiometrische Verhältnis“. Es ist eine Massenangabe und ist bei Lambda λ = 1 erreicht. Ist dieses eingestellt, findet jedes Molekül Kraftstoff genau die richtige Menge an Sauerstoff-Reaktionspartnern. Das ideale Verhältnis Luft zu Kraftstoff beträgt bei Benzin 14,7:1 und bei Diesel 14,5:1. Verbrennungsmotoren sollten immer eng um λ = 1 betrieben werden, da dies die Abgasreinigung erlaubt. Darauf kommen wir beim O2-Sensor noch zurück.
Das lässt erkennen, dass nicht das Luftvolumen oder die Dichte alleine wichtig sind, sondern die Masse. Die Masse hängt mit dem Volumen und der Dichte zusammen, weshalb ältere Messverfahren (AFM, Vortex und Temperatur) diese Parameter messen, dann aber auf die Masse schließen müssen. Nur der MAF misst tatsächlich die Masse und ist am besten für diesen Zweck geeignet.
Technisch wird die Luftmasse über zwei Verfahren gemessen. Beide Verfahren basieren auf der Veränderung des elektrischen Widerstands eines Metalls wie Tungsten oder Platin. Das eine Verfahren arbeitet mit einem Draht und heißt deshalb „Hot Wire“. Es ist das ältere Verfahren. Dabei ist ein Draht dem Luftstrom ausgesetzt und ein zweiter liegt als Referenz geschützt. Das zugrundeliegende Prinzip ist, dass die Luftmoleküle den Draht abkühlen und seinen elektrischen Widerstand verändern. Der Widerstand bestimmt den Stromfluss durch den Draht und das ergibt das Signal.
Das zweite Prinzip benutzt einen Film mit Leiterbahnen, deshalb „Hot-Film“ genannt. Diese werden auch durch Strom aufgeheizt und durch die Luftmoleküle abgekühlt. Dadurch dass mehrere Leiterbahnen und somit zwei Sensoren nebeneinander liegen,kann dieser Sensor sogar die Richtung des Luftstroms bestimmen. Je nachdem welcher der beiden Sensoren zuerst abkühlt, strömt die Luft gerade hinein oder heraus. Bei Verbrennungsmotoren gibt es eine Pulsation. Dabei geht die Luft nicht nur zum Motor hin, sondern sie pulsiert und bewegt sich in Stößen, auch von ihm weg. Auch diese Information kann von der ECU für eine bessere Steuerung der Verbrennung genutzt werden.

Das Gute dabei ist, dass im Gegensatz zu den beiden folgenden, älteren Verfahren die Luftmasse zu bestimmen, der Luftmassenmesser automatisch Höhenänderungen und Temperaturänderungen mit einbezieht bzw. von deren Werten unabhängig ist, da beides sich auf die Luftmasse auswirkt. Es ist keine gesonderte Temperaturmessung nötig, um die Luftmasse zu bestimmen.
Ihr findet den MAF-Sensor direkt nach dem Luftfiltergehäuse. Das Gitter vor der Messeinheit ist übrigens nicht nur zum Fernhalten von Schmutz gedacht, sondern glättet den Luftstrom, so dass der sehr kleine Teil, der am Sensor vorbeiströmt, auch tatsächlich auf die gesamte Luftmasse hochgerechnet werden kann.
Übliche Fehlersymptome sind:
- Motor startet nicht
- Hoher Verbrauch
- Schlechte Beschleunigung
- Stotternder Motor, kurze Aussetzer
Typische Fehlercodes: P0101, P0102.
Wenn ihr eines der Symptome bemerkt, lohnt es sich, gerade bei den Hot-Wire oder Hot-Film Sensoren diesen mit Bremsenreiniger und ein wenig Luftdruck zu reinigen. Oft sind die Sensoren nur verschmutzt. Darauf reagieren sie sehr empfindlich, jegliche Verschmutzung verfälscht die Messung erheblich. Es ist sehr davon abzuraten vor diesen Sensoren einen Nachrüst-Luftfilter zu verwenden, der geölt werden muss. Schon kleinste mitgerissene Öltropfen verschmutzen den Sensor.
Normalerweise benötigt die ECU das Signal vom Luftmassenmesser. Es gibt Motoren, bei denen der Sensor stillgelegt werden kann und der Motor funktioniert immer noch. Das ist oft bei Motoren der Fall, bei denen der Sensor nicht unbedingt zur Motorsteuerung sondern primär zum Einhalten der Emissionswerte nötig ist, wie bei Fahrzeugen der Schadstoffklassen 2/3. Wenn ihr einfach den Stecker abzieht, nutzt die ECU einen Standardwert. Als Folge verschlechtern sich die Abgaswerte, aber der Motor bleibt voll funktionsfähig.
Luftmengenmesser (AFM)
Der Luftmengenmesser dient dem selben Zweck wie der Luftmassenmesser, allerdings liegt ein anderes Prinzip zu Grunde. Dieser Typ wurde beim Aufkommen der ersten Einspritzmotoren in den 1980er Jahren verwendet, ist aber schon seit vielen Jahren durch den MAF-Sensor ersetzt worden, da letzterer die Luftmasse direkt misst.
Beim Luftmengenmesser strömt die Luft durch eine Kammer und bewegt dabei eine federbelastete Klappe. Insofern reagiert die Klappe auf die Luftgeschwindigkeit und deren Dichte. Um die Genauigkeit zu erhöhen, ist der AFM oft mit einem Temperatursensor gekoppelt, um so besser auf die Dichte der Luft schließen zu können, was wieder besser auf die Luftmasse schließen lässt. Der Zweck ist ja die richtige Menge Kraftstoff der Luft beizumischen und dieses Verhältnis bezieht sich eben auf die Luftmasse, nicht das Volumen oder die Dichte.
Die Klappe besitzt einen zweiten Flügel, der in eine geschlossene Kammer einfährt. Durch das dabei entstehende Luftpolster wird die Klappenbewegung abgedämpft. Dieser Klappenmechanismus ist über einer Welle mit einem Potentiometer verbunden, an dem sich entsprechend der Luftmenge ein Spannungswert einstellt.
Er befindet sich zwischen Luftfilter und Drosselklappe und muss immer waagerecht montiert sein. Eine andere Lage würde die federbelastete Klappe auch noch mit der Schwerkraft beaufschlagen. Man stelle sich nur vor, der Wagen würde über eine schlechte Strecke fahren und jeder Stoß würde zu einer Bewegung der Klappe führen. Ein weiterer Nachteil dieses Systems ist, dass die Klappe wie eine Drosselklappe wirkt. Sie beschränkt den Luftstrom und setzt ihm einen Widerstand entgegen, wenn auch einen kleinen.
Da der AFM vor der Einführung der ODB2-Schnittstelle genutzt wurde, gibt es keine einheitlichen Fehlercodes.

Exot: Luftmengenmesser Karman Vortex
Ebenfalls in den 1990er Jahren wurden in einige Fahrzeuge Vortex-Sensoren eingebaut, um die Luftmasse zu bestimmen. Sie basieren auf dem Prinzip Luftwirbel zu erzeugen. Dazu wurde ein zumeist dreieckiges Hindernis in den Luftstrom gebaut, der die Wirbel verursacht. Die Frequenz der entstehenden Wirbel ist proportional zur durchströmenden Luftmenge. Die Wirbel werden nach dem Hindernis, dem „Vortex Generator“, durch ein Ultraschallsignal oder eine Metallfolie gemessen. Diese bewegen eine LED, die einen Fototransistor bestrahlt. Durch den wechselnden Lichteinfall erzeugt der Transistor ein Signal für das Steuergerät. Das Signal gibt die Geschwindigkeit der Luft an. Zusammen mit dem bekannten Volumen des Gehäuses kann die Luftmasse bestimmt werden.
Drucksensoren
Viele Drucksensoren arbeiten nach dem gleichen Prinzip, welches ein große Freiheit bei der Größe und Form erlaubt. Zudem kann es für die Messung eines Drucks oder als Differenzdrucksensor ausgelegt werden, der mit zwei Drücken beaufschlagt wird.
Das Prinzip ist eine dünne Membran mit vier aufgeätzten Dehnmesswiderständen. Davon werden bei Druckänderungen je zwei gedehnt und zwei gestaucht. Die Widerstände sind zu einer sogenannten Wheatstone-Brücke zusammengeschaltet, die sehr präzise Messergebnisse zulässt. Auf der einen Seite ist ein Siliziumchip, in das das Membran bei steigendem Druck eingedrückt wird. Auf der anderen Seite befindet sich das Medium, dessen Druck es zu messen gilt.
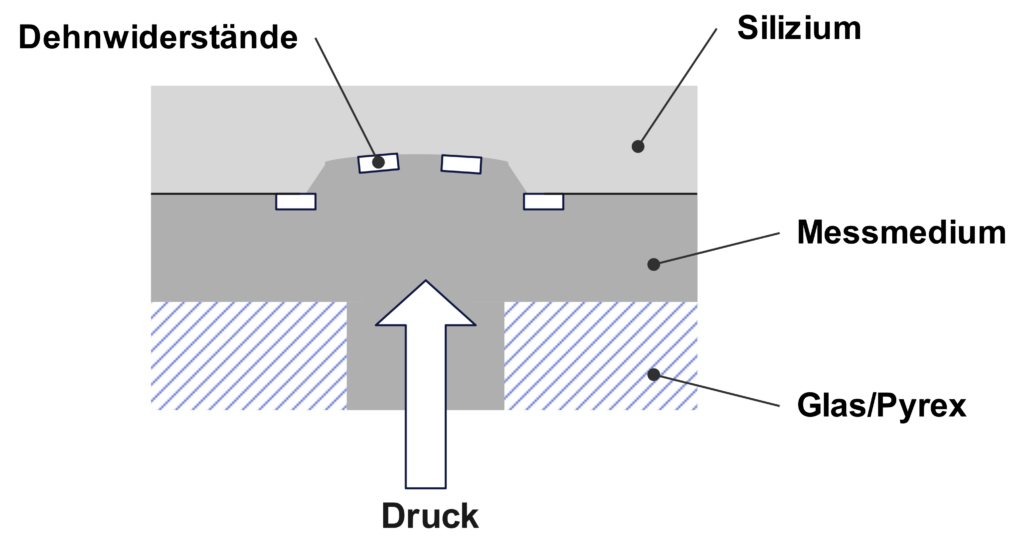
Andere Drucksensoren wirken mit dem Membran auf ein Piezo-Element, dass entsprechend des Drucks eine elektrische Spannung erzeugt.
Ansaugluft-Drucksensor (MAP)
MAP steht für „Manifold Absolute Pressure“. Dieser Sensor misst über den Luftdruck die Luftdichte in der Ansaugbrücke. Genau wie der MAF kompensiert der MAP Temperatur und Höhe und benötigt dafür keine separate Messung, um die Luftmasse zu bestimmen.
Da der MAP-Sensor das Gleiche macht wie der MAF, stellt sich die Frage, warum Motoren beide besitzen? Bei Saugmotoren wird die Messung schlichtweg noch genauer. Bei aufgeladenen Motoren (Turbo) dient es einmal der Überwachung der Ansaugleitungen, denn eine Differenz zwischen der eingehenden und ankommenden Luft deutet auf ein Problem hin. Zusätzlich entstehen bei aufgeladenen Motoren sehr komplexe Luftbewegungen durch die Drosselklappe, den Turbolader und den Pulsationen des Motors. Um davon ein besseres Bild zu bekommen und beispielsweise einen Turbolader mit variabler Geometrie besser zu steuern, benötigt es beide Sensoren. Bei Dieselmotoren kommt zusätzlich noch das AGR-Ventil dazu, dessen Funktion ebenfalls durch die Kombination beider Sensoren überwacht wird.
Da der Druck im Ansaugstutzen gemessen wird, ist der Sensor auch immer dort zu finden.
Übliche Fehlersymptome sind:
- Motor startet nicht
- Hoher Verbrauch
- Schlechte Beschleunigung
- Stotternder Motor, kurze Aussetzer
Typischer Fehlercode: P0106.
Wer seinen Motor in der Leistung steigert und dazu den Ladedruck erhöht, muss oft auch einen anderen MAP-Sensor haben, wenn der Druck den Bereich des Originalsensors übersteigt.
Dieselpartikelfilter-Differenzdrucksensor
Das Abgas strömt auf der einen Seite in den Partikelfilter hinein und auf der anderen heraus. Sowohl auf der Eingangs- wie auch auch der Ausgangsseite ist ein Drucksensor. Wird die Differenz zwischen beiden zu groß (durchaus > 1 bar), muss eine Partikelfilter-Regenerierung eingeleitet werden.
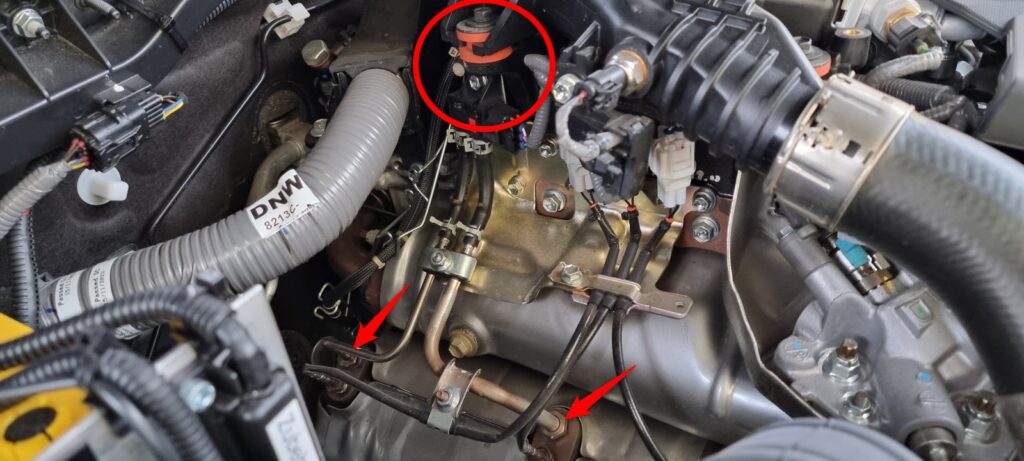
Es gibt noch ein zweites Verfahren, dass oft mit dem Differenzdruckverfahren gekoppelt wird. Es ist ein rein rechnerisches Verfahren, bei dem von den Fahrsituationen und der Abgasmenge auf die Rußbelastung umgerechnet wird.

Aschelast
Es ist wichtig zu wissen, dass trotz Regeneration des Partikelfilters, dieser irgendwann getauscht oder gereinigt werden muss. Während die Rußpartikel durch die Anhebung der Abgastemperatur vollständig verbrennen, bleiben aber Rückstände von Ölverbrennung, Motorpartikeln und anderen Stoffe permanent als Asche im Filter zurück. Das führt irgendwann zu einer dauerhaften Verstopfung, die Folgeschäden, beispielsweise beim Turbolader, nach sich ziehen. Daher sollte auch der Partikelfilter im Auge behalten werden.
Öldrucksensor
Das ist einer der wichtigsten Sensoren im Motor. Er ist nicht für den Betrieb erforderlich, der Motor läuft auch ohne ihn und verwendet seine Werte nicht zur Regelung, aber er ist für die Kontrolle extrem wichtig. Steht nicht genug Öldruck zur Verfügung, wofür es verschiedene Gründe geben kann, kommt es zu schadhaftem Verschleiß oder in sehr kurzer Zeit zu erheblichen Schäden bis zum Totalschaden des Motors.
Während früher der Öldruck als Wert auf einer Messuhr angezeigt wurde, sind heutzutage leider nur noch Öldruckschalter zu finden. Der Öldruckschalter alarmiert wenn ein vordefinierter Wert, in der Regel um die 0,5 bis 0,7 bar, unterschritten wird. Dieser Wert ist oft sehr niedrig gewählt, fast schon zu niedrig. Geht die Öldruckkontrollleuchte an, solltet ihr sehr schnell reagieren, anhalten und den zügig Motor abstellen. Keinesfalls weiterfahren!
Wer noch eine Messanzeige hat, darf sich glücklich schätzen. Hier könnt ihr den Öldruck über eine Fahrt, verschiedene Jahreszeiten und Außentemperaturen und der Ölnutzungsdauer beobachten und eure Schlüsse daraus ziehen. Ihr könnt eure Motordrehzahl immer so anpassen, dass ihr genug Öldruck habt. So lässt sich auch feststellen, wenn das Überdruckventil der Ölpumpe beschädigt ist und der Öldruck deshalb dauerhaft zu niedrig liegt. Wer keine Öldruckanzeige hat, dem sei gesagt, es ist eine sinnvolle Maßnahme einen Öldruckmesser mit kombiniertem Warnschalter nachzurüsten. Mit diesem Messinstrument lassen sich aufkommende Probleme in der Motorschmierung früh erkennen.
Mehr dazu und warum ein Öldruckmesser sehr sinnvoll ist, findet ihr in unserem Artikel zu Zusatzinstrumenten: Zusatzinstrumente.
Der Öldrucksensor kann überall am Motor angebracht sein. Wenn nur ein Kabel dort hingeht, ist es ein Öldruckschalter, der beim Auslösen einfach auf die Masse der Batterie über den Motorblock durchschaltet. Es kann auch ein Geber ohne Warnkontakt sein. Gehen zwei Kabel hin, ist es ein Öldruckmesser mit einem Geber und Warnschaltung.
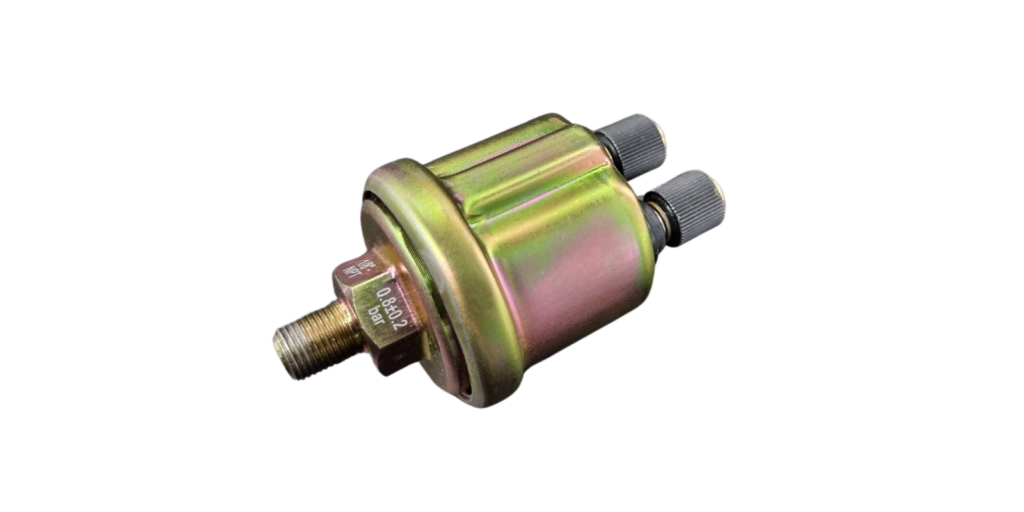
Auf einem Nachrüst-Öldruckgeber sind Angaben zum Gewinde (z.B. 1/8″ NPT), zum Messbereich (z.B. 0-5 bar) und wenn ein Warnkontakt vorhanden ist, wann dieser alarmiert: (z.B. 0,8 bar)
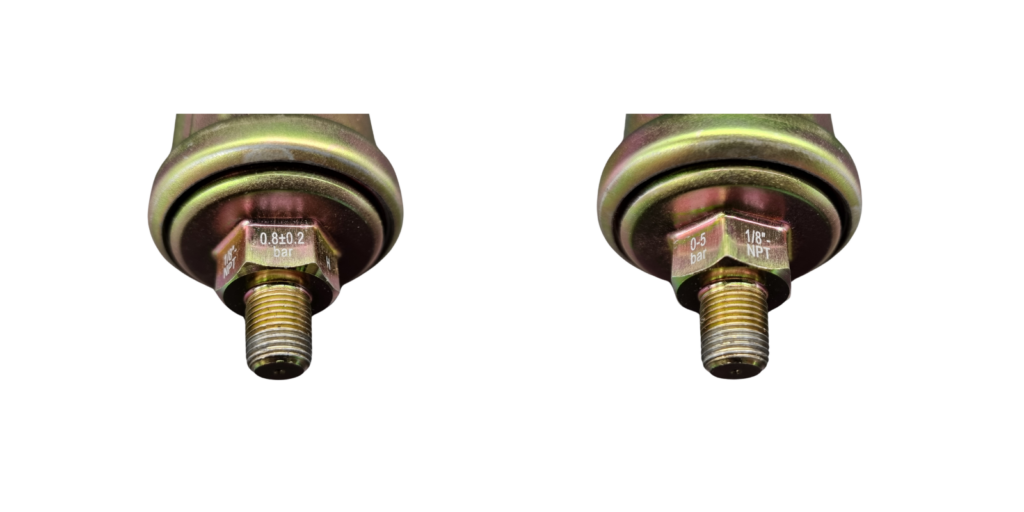
Typische Fehlersymptome gibt es nicht. Zu wenig Öldruck äußert sich in Schäden, die sich langsam aufbauen oder eben dem sofortigen Versagen des Motors. Achtet darauf, dass die Öldruckkontrollleuchte angeht, wenn ihr die Zündung einschaltet. So könnt ihr überprüfen, ob sie funktioniert. Solange der Motor nicht läuft, ist kein Öldruck vorhanden. Nach den ersten paar Umdrehungen muss sie ausgehen.
Typische Fehlercodes: P0520, P0521, P0522.
Fahrzeuge ohne Ölmessstab
Ihr solltet so oder so den Ölstand regelmäßig kontrollieren, da er nicht nur wichtig ist, sondern diese Kontrolle auch über andere Probleme informieren kann. Es ist also besser, wenn Euer Motor noch einen Ölmessstab besitzt. Das ist leider immer öfter nicht mehr der Fall. Denn geht die Öldruckkontrollleuchte an, ist der Ölmessstab die einzige und sicherste Kontrollmöglichkeit, die ihr ohne weitere Hilfe und Technik nutzen könnt.
Wer nur noch eine digitale Anzeige in seinem Fahrzeug vorfindet, muss sich auf die Messergebnisse verlassen. Es gibt leider genug Beispiele, in denen Fehlalarme ausgelöst wurden oder die Besitzer zum Nachfüllen einer Menge X aufgefordert wurden. Nur, zu viel Öl kann ebenfalls sehr schädlich sein. Wer nicht mit diesem sehr simplen und absolut sicheren Messstab den wahren Zustand prüfen kann, der muss einen Ölwechsel vornehmen, um die korrekte Ölmenge sicherzustellen.
Stellen Sensoren fest, dass zu wenig Öl da ist, verhindern sie in der Regel das Weiterfahren. Der Wagen muss abgeschleppt werden. Sehr ärgerlich, wenn es sich dabei um einen Fehlalarm handelt. Auch das Überprüfen mittels der Sensoren geht nicht einfach so. Im Handbuch und auch auf dem Display werden Anweisungen gegeben, wie der Wagen zu stehen hat (waagerecht) und ob beispielsweise eine vorgegebene Drehzahl im Stand eingehalten werden muss usw. Dabei könnte es so einfach sein.
Kraftstoffdrucksensor
Auch der Druck des Kraftstoffs muss gemessen werden. Das hängt allerdings vom Motortyp ab. Common-Rail-Einspritzer benötigen den Sensor, um den Druck im Rail zu bestimmen. Alle Einspritzdüsen sind an dieser „Schiene“ angeschlossen, die permanent mit Kraftstoff und Druck versorgt wird. Nur so sind die verschiedenen Einspritzungen möglich. Bei einem modernen Motor können das bis zu acht(!) pro Arbeitstakt sein.
So wird beispielsweise bei der Reinigung des Dieselpartikelfilters sehr spät noch einmal Diesel in den Zylinder eingespritzt, so dass dieser erst spät verbrennt. Das lässt die Abgastemperatur auf den benötigten Wert ansteigen. Diese Vor- und Nacheinspritzungen funktionieren nur, wenn die Einspritzung von der Motordrehzahl mechanisch entkoppelt ist und immer ein hoher Dieseldruck anliegt.
Damit das Steuergerät bei gegebenen Druck, Last und allen anderen Werten weiß, wie lange die Einspritzung erfolgen muss um das beste Luft-Kraftstoffverhältnis zu erreichen, muss der Druck bekannt sein. Ihr findet daher den Sensor immer am Rail, also an der gemeinsamen Leitung oberhalb der Einspritzdüsen.
Übliche Fehlersymptome sind:
- Schlechter Motorstart
- Hoher Verbrauch
- Schlechte Bechleunigung
Typische Fehlercodes: P0190, P0193.

Der Wahnsinn in Zahlen
Um sich vorstellen zu können, was ein heutiger Common-Rail- Direkteinspritzer so leistet, hier eine kleine Rechnung:
Ihr fahrt mit einer Drehzahl von 2.500 Umdrehungen pro Minute. Das ist ein gängiger Wert für einen Dieselmotor. Das bedeutet, das jede Motorumdrehung (360°) 0,024 Sekunden = 24 Millisekunden dauert. Bei einem Viertakt-Vierzylindermotor gibt es alle 180° einen Taktwechsel: Ansaugen > Kompression > Arbeit > Ausstoßen. Bei 2.500 Umdrehungen findet der Taktwechsel dann alle 12 Millisekunden statt.
Die Einspritzung bei einem Direkteinspritzer startet frühestens in der zweiten Hälfte des Kompressionstakts und hat daher maximal 6 Millisekunden Zeit für die Einspritzung des gesamten benötigten Kraftstoffs. Bei 3.500 Umdrehungen reduziert sich das weiter auf 4 Millisekunden. Zum Vergleich, ein Augenaufschlag dauert ca. 100 bis 150 Millisekunden.
Das ist übrigens auch der Grund, warum Direkteinspritzer auf Drehzahlen von rund 6.500 Umdrehungen pro Minute begrenzt sind. Danach gibt es einfach nicht mehr genug Zeit, bei den derzeitig möglichen Einspritzdrücken, die benötigte Menge Kraftstoff einzuspritzen.
Temperatursensoren
Die meisten Temperatursensoren arbeiten mit Thermistoren, elektrische Widerstände, deren Widerstandswert sich in Abhängigkeit von der Temperatur verändert. Diese Widerstände nutzen dazu Metalle, Metalloxide oder Silizium, je nach Bauart. Deshalb gehen wir im Folgenden nur den Einsatzzweck durch.
Ansaugluft-Temperatursensor (IAT)
Um ein noch effizienteres Gemisch und dadurch auch weniger Abgase und Verbrauch zu erzielen, kann den Daten über die Luftmasse (MAP, MAF, AFM) noch die Temperatur hinzugefügt werden. Da kältere Luft mehr Sauerstoff enthält als die gleiche Menge wärmerer Luft, kann die Einspritzmenge weiter optimiert werden.
Die gemessene Temperatur lässt Rückschlüsse auf die Dichte der Luft zu. Oft ist er im AFM oder MAF integriert. Ist er dort nicht zu finden, ist er an einer anderen Stelle im Ansaugstrang angebracht, meistens in der Nähe der Drosselklappe.
Übliche Fehlersymptome sind:
- Rauher Motorlauf
- Leistungsverlust
- Ruckeln
Typische Fehlercodes: P0113.
Öltemperatursensor
Außer dem Druck ist auch die Öltemperatur von Interesse. Übrigens auch in den Getrieben, aber darum geht es hier nicht. Öl wird mit zunehmender Temperatur dünnflüssiger, was ihr mittels des Öldrucksensors beobachten könnt, denn der Öldruck nimmt nach dem Motorstart eine Weile ab, bis das Öl seine Betriebstemperatur erreicht hat. Meldet der Öltemperatursensor seine Werte an die ECU, können diese, genau wie beim Kühlmittel, den Motor in den Notlauf versetzen oder den Motorstart unterbinden.
Ursache für zu hohe Öltemperaturen kann zu wenig Öl, eine zu heiße Verbrennung oder eine gestörte Ölkühlung sein. Das sollte sich dann auch in der Kühlmitteltemperatur widerspiegeln. Direkt lassen sich am Motorlauf oder Fahrverhalten des Fahrzeugs keine Symptome erkennen.
Übliche Fehlersymptome sind:
- Motornotlauf
Typische Fehlercodes: P0196, P0197, P0198.
Kraftstofftemperatursensor
Wie bei der Luft auch hat die Temperatur des Kraftstoffs Einfluss auf seine Dichte. Kühlerer Kraftstoff ist weniger dicht als wärmerer. Daher muss bei kühlerem Kraftstoff etwas mehr in die Verbrennung gegeben werden.
Der Temperatursensor befindet sich irgendwo im Kraftstoffsystem, zumeist an der Pumpe oder dem Filter. Es können auch zwei Sensoren vorhanden sein. Fehler sind nur schwer zu erkennen, da sich ein Fehler nicht deutlich auf das Fahren auswirkt.
Übliche Fehlersymptome sind:
- Abgastest wird nicht bestanden
- Erhöhter Verbrauch
Typischer Fehlercode: P0183.
Kühlwassertemperatursensor
Früher diente der Sensor lediglich zur Anzeige für den Fahrer und die Interpretation lag alleinige bei ihm. Gut, bis weiße Dampfwolken aus dem Motor aufstiegen. Bei Fahrzeugen mit Steuergerät wird die Kühlwassertemperatur in das Motormanagement mit einbezogen. Die Temperatur beeinflusst die Menge an Kraftstoff die gegeben wird, steuert aber auch Dinge wie den Kühlerlüfter, wenn er elektrisch läuft. Ist das Kühlwasser zu heiß, versetzt der Sensor den Motor auch in den Notlauf um so Schäden wie eine kaputte Zylinderkopfdichtung, zu verhindern. Er kann auch den Motorstart unterbinden.
Der Sensor steckt in den meisten Fällen direkt im Kühlwasserkreislauf. Es gibt auch Fahrzeuge die mehrere Sensoren haben. Bei manchen Motoren hat der Sensor keinen Kontakt zur Flüssigkeit. In den Fällen wird in Abhängigkeit von der gemessenen Temperatur die Wassertemperatur berechnet.
Übliche Fehlersymptome sind:
- Zu hoher Verbrauch
- Schwarzer Rauch im Abgas
Typische Fehlercodes: P0116, P0117, P0118.
Abgastemperatursensor (EGT)
Diesen Sensor finden wir zumeist in Dieselmotoren. Er misst die Temperatur des Abgases und gibt es nur einen, sitzt dieser möglichst nah am Motor im Abgaskrümmer. Heutige Fahrzeug haben zumeist mehr Abgastemperatursensoren, durchaus vier oder sogar mehr. Die Abgastemperatur steht im direkten Zusammenhang mit der Änderung des Kraftstoff-Luftgemischs, was sich so überwachen lässt. Der Sensor kann den Turbo als auch den Katalysator vor Schäden durch Überhitzung schützen. Gerade bei Motoren mit Leistungssteigerung ist es der wertvollste Sensor, um dem Fahrer wichtige Informationen zu geben. Im Motorsport werden oft „nicht gasfeste“ Tunings eingesetzt. Die volle Leistung des Motors darf dabei nicht bedenkenlos über längere Zeiträume eingesetzt werden. Erfahrene Fahrer nutzen die Abgastemperaturanzeige dazu, um zu entscheiden, wann und wie lange sie mit hoher Leistung fahren.
Beim Partikelfilter wird der Sensor eingesetzt, um dessen Regeneration zu ermöglichen. Steht eine Regeneration an, wird durch spätes Einspritzen von Kraftstoff die Abgastemperatur erhöht. Erreicht sie die notwendige Temperatur, kann der Sensor den Prozess starten lassen.
Übliche Fehlersymptome (beim Diesel) sind:
- Leistungsverlust
- Hoher Verbrauch
- Lange DPF-Regeneration
- Häufige DPF-Regeneration
Typische Fehlercodes: P0405, P0546, P2032.
Vibrationssensoren
Klopfsensor
Das „Klopfen“ (auch „Klingeln“ genannt) ist ein gefürchteter Zustand von Benzinmotoren, da er in kurzer Zeit zu Motorschäden führt. Umgangssprachlich werden zwei Ursachen mit „Klopfen“ bezeichnet, da beide dieses Geräusch verursachen. Das Geräusch ist wahrnehmbar und erinnert an einen kleiner Hammer, der auf den Motor geschlagen wird.
Die erste Ursache ist das unkontrollierte und ungewollte Selbstzünden des Benzins an verschiedenen Stellen des Brennraums. Das erzeugt extremen Druck und Stress für Kolben, Pleuel und Kurbelwelle. Ein Grund dafür ist die falsche Benzinsorte (Oktanzahl) für den jeweiligen Motor und sein Verdichtungsverhältnis. Je stärker ein Motor verdichtet desto heißer wird das Gemisch und desto eher neigt es zur Selbstentzündung. Die Klopffestigkeit von Benzin wird über dessen Oktanzahl definiert. Je höher die Oktanzahl ist, desto weniger neigt der Kraftstoff zur Selbstzündung. Deshalb müssen hochverdichtete Motoren auch Kraftstoffe mit hohen Oktanzahlen fahren.
Die zweite Ursache ist die vorzeitige externe Zündung. Das Benzin zündet also nicht durch die Kompression selbst, welche vergleichsweise spät einsetzt. Die zu frühe Zündung kann noch schlimmer sein, da hier die Verbrennung so früh einsetzen kann, dass sie erheblichen Druck gegen den heransausenden Kolben ausübt. Sie macht sich ebenfalls durch Klopfgeräusche bemerkbar. Vorzeitige Zündung kann insbesondere bei Direkteinspritzung erfolgen, wenn der Motor eine niedrige Drehzahl bei hoher Last hat. Glühende Rußpartikel, die beispielsweise an versotteten Ventilen hängen oder herabfallen oder kleine Ölspritzer, die ungewollt in Brennraum während der Kompressionsphase gelangen, können zur verfrühten Zündung führen. Erhebliche Schäden, die schnell auftreten, sind die Folge.
Ein weiterer Grund für eine zu frühe Zündung ist die dynamische Verstellung des Zündzeitpunkts. Die Zündung des Benzins erfolgt immer bevor der Kolben den höchsten Punkt (OT – Oberer Totpunkt) erreicht hat. Das ist notwendig, da auch die Verbrennung einen Moment braucht um Kraft zu entwickeln. Je schneller der Kolben also nach oben rast, desto eher muss das Gemisch gezündet werden. Dann liegt der Punkt der größten Kraftentfaltung nach dem OT und kann den Kolben nach unten drücken. Deshalb wird der Zündzeitpunkt mit zunehmender Drehzahl automatisch immer weiter in Richtung Frühzündung verstellt. Der Zündzeitpunkt wird in Grad vor oder nach dem OT angegeben. Übliche Werte liegen zwischen 10° im Leerlauf bis über 34° vor OT (Frühzündung) bei maximaler Drehzahl. 34° mag sich viel anhören, bedeutet aber praktisch nur wenige Millimeter Abstand des Kolbens vom OT. Dagegen wären 50° oder 60° vor OT ein erheblich größerer Abstand, da 1° Drehung nicht überall die gleiche Distanz bedeutet.
Wird über die maximalen Werte hinausgegangen oder passt der aktuelle Zündzeitpunkt nicht zum Kraftstoff (Oktanzahl) oder der Drehzahl kann es zum Klopfen kommen.
Der Klopfsensor ist ein Mikrofon, der auf das spezifische Geräusch des Klopfens reagiert. Sobald er feststellt, dass es zum Klopfen kommt, sorgt er dafür, dass die Zündung wieder etwas später stattfindet oder mehr Kraftstoff gegeben wird, was ebenfalls einer Frühzündung entgegen wirkt. Dabei spielt der Kühlungseffekt und das fettere Gemisch eine Rolle.
Während früher das Klopfen durch die richtige Einstellung des Zünderverteilers bzw. bei ECU’s durch eine entsprechende Zündkurve (Verhältnis Frühzündung zu Drehzahl) verhindert wurde, kann mit Klopfsensoren der Zündzeitpunkt dynamisch immer nah an die Grenze gebracht werden. Das ermöglicht es eine hohe Leistung zu erzielen, ohne Gefahr zu laufen, den Motor durch Klopfen zu beschädigen.
Diesel können nicht durch ungewollte Frühzündung klopfen, denn sie komprimieren nur Luft und kein Luft-Kraftstoffgemisch. Die Einspritzung wird gesteuert und kommt zum richtigen Zeitpunkt. Bei einem Dieselmotor ist das Problem eher eine verspätete Zündung. Deshalb besitzen Dieselmotoren in aller Regel keine Klopfsensoren. Es gibt einige Modelle, die einen ähnlichen Sensor haben um den Zündbeginn zu messen und ggf. den Einspritzbeginn in einem engen Rahmen nachzuregeln.
Der Sensor muss fest mit dem Motor verschraubt sein. In ihm ist eine ringförmige Masse. Da sie träge ist, wird sie im Rhythmus der Motorvibrationen mitbewegt. Dabei drück sie auf ein ebenfalls ringförmiges Piezo-Element. Diese haben die Eigenschaft, bei Druck eine Spannung zu erzeugen, die gemessen werden kann. Das Vibrationsmuster des Motors ist dem Steuergerät bekannt. Fängt der Motor an zu Klopfen, erzeugt der gestörte Brennraumdruck Vibrationen und Körperschall. Das überträgt sich auf den Ring im Sensor, der dort einen entsprechend unruhigen Spannungsverlauf abgibt.
Der Sensor befindet sich immer direkt am Motorblock. Vierzylindermotoren haben einen, Motoren mit sechs oder mehr Zylindern können mehrere Sensoren haben, um alle Zylinder sicher zu erfassen.
Übliche Fehlersymptome sind:
- Klopfgeräusche wahrnehmbar
- Warnleuchte (wenn vorhanden)
- Motor schaltet in den Notlauf
Typischer Fehlercode: P0325.
Gas- und Konzentrationssensoren
O2-Sensor (Lambda-Sonde)
Wie der Name es vermuten lässt, misst ein O2-Sensor den Sauerstoffgehalt. Das geschieht bei Autos vor (Upstream) und nach dem Katalysator (Downstream). Der Sensor vor dem Katalysator lässt über den gemessenen Sauerstoffanteil im Abgas einen Rückschluss auf das Kraftstoff-Luftgemisch (Lambda) zu. Entsprechend der Messung wird der Verbrennung mehr oder weniger Kraftstoff zugemischt.
Ziel ist es das ideale Verhältnis Luft zu Kraftstoff (λ = 1) einzuhalten. Das Verhältnis von Luft und Kraftstoff ist für die Leistung und die Schadstoffmengen extrem wichtig. Der Sauerstoffsensor dient somit der Kontrolle, ob das von der ECU gewünschte Verhältnis auch so eingesetzt wurde und die Werte im gewünschten Bereich liegen.
Es gibt zwei Arten von O2-Sensoren, den Schmalband- und den Weitband-Sensor. Der Schmalbandsensor kann der ECU lediglich eine Rückmeldung darüber geben, ob das Gemisch „fett“ oder „mager“ war. Der Breitbandsensor kann zusätzlich das Verhältnis melden. Er ist also viel genauer.
Der Aufbau des Sensors ist einigermaßen kompliziert und es gibt verschiedene Typen. Das Grundprinzip ist, dass der Sauerstoffanteil im Abgas (0,3 bis 3%) mit dem der Außenluft (ca. 20,8%) verglichen wird. Verschiedene Beschichtungen (Zirkondioxid, Titandioxid) erzeugen je nach Differenz eine elektrische Spannung, die das Signal ausmacht. Bei einem Restgehalt von 3% gilt das Kraftstoff-Luftgemisch als „mager“, bei 0,3% als „fett“.
Für den Betrieb reicht eine Lambda-Sonde aus. Mit der Einführung von EOBD (US-Bezeichnung: OBD-2) muss allerdings die Funktion des Katalysators mit überwacht werden, weshalb es eine zweite Sonde nach dem Katalysator gibt. Durch die Vergleichsmessung kann festgestellt werden, ob der Katalysator noch einwandfrei funktioniert. Dabei wird die Fähigkeit des Katalysators Sauerstoff zu speichern und später wieder abzugeben gemessen. Diese Fähigkeit lässt über die Betriebsdauer nach.
Generell wirken sich Probleme mit dem Sensor bei älteren Fahrzeugen nicht so stark aus, da sie in Bezug auf Leistung und Emissionen größere Abweichungen zulassen. Modernere Fahrzeuge reagieren empfindlicher. Ein defekter Sensor kann zur Zerstörung des Katalysators führen und sollte deshalb nicht ignoriert werden.
Übliche Fehlersymptome sind:
- Abgasprüfung schlägt fehl
- Leistungsverlust
- Höherer Verbrauch
Typische Fehlercodes: P0131, P0132, P0133, P0135, P0138, P0141, P0420, P2238.
NOX-Sensor
Stickoxide sind gesundheitsschädlich und ein typisches Problem von Dieselmotoren. Um die Stickoxide zu reduzieren besitzen Motoren verschiedene Techniken. Eine davon ist die Abgasrückführung (AGR), eine andere der SCR-Katalysator mit AdBlue.
Die Abgasrückführung ist de facto eine Reduzierung des Hubraums, da ein Teil des Zylinders mit inaktivem Abgas gefüllt wird, der nicht von Luft und Kraftstoff belegt werden kann. Der so verringerte Sauerstoffanteil kühlt zudem die Verbrennung ab, was ebenso zur Stickoxidreduzierung führt. AdBlue ist ein Harnstoff, der die gefährlichen Stickoxide im SCR-Katalysator in ungefährliches Stickstoff N2 und Wasser H2O umwandelt.
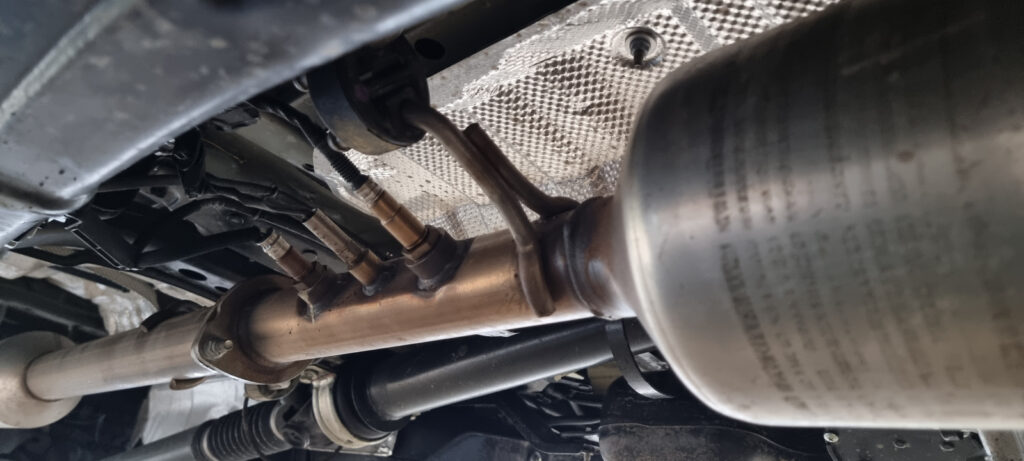
Je nach System gibt es den Sensor einmal vor dem SCR-Katalysator oder zweimal, dann ist ein weiterer hinter dem Katalysator um das Ergebnis der Stickoxidreduzierung zu überwachen. Die Sonde hat einen sehr komplexen Aufbau. Das Abgas gelang durch eine Diffusionsbarriere in eine Pumpkammer. Eine zweite Kammer ist mit der Außenluft verbunden und dient als Referenz für den Sauerstoffgehalt. Diese Sauerstoffdifferenz erzeugt eine Spannung, die das Steuergerät des Sensors nutzt, um den Sauerstoff aus dieser Kammer zu pumpen. Die verbliebenen Stickoxide wandern durch eine zweite Diffusionsbarriere in die zweite Kammer und an einer beschichteten Elektrode vorbei, die die Stickoxide in Stickstoff und Sauerstoff katalytisch spaltet. Der Stickstoff verlässt die Kammer durch eine poröse Schicht. Der Sauerstoff wird nach außen gepumpt, wobei eine Sensorzelle den Sauerstoffstrom erfasst und an das Steuergerät meldet. Das Messergebnis steuert wie viel AdBlue zugegeben wird.
Übliche Fehlersymptome sind:
- Hoher Verbrauch
- Motor schaltet in den Notlauf
- Schlechter Leerlauf
Typische Fehlercodes: P2200, P2202, P229E, P229F62.