Welch passender Vergleich, den wir bei unserer Recherche hörten: Der Turbolader ist eine Diva. Leistet viel, ist aber unheimlich empfindlich. Besonders wenn in seinem Umfeld etwas nicht stimmt. Wie er funktioniert und wie ihr einen Turbolader-Defekt vermeiden könnt, haben wir bei Motair, einem der größten Turbo-Spezialisten Europas, für euch erfragt.
Der Turbolader ist eines der am höchsten beanspruchten Aggregate heutiger Motoren. Vergleichsweise filigrane Teile sind hohen Temperaturen und extrem hohen Drehzahlen ausgesetzt. Ein Turbolader kommt auf gut 300.000 U/min-1. Je kleiner, desto schneller. Auf der Turbinenseite werden 850 bis über 1.050° Celsius erreicht, wohingegen nur wenige Zentimeter daneben die Verdichterseite auf circa 250° Celsius kommt. Dazwischen ist eine Welle mit nur wenigen Millimetern Durchmesser. Diese Werte machen klar, welchen hohe Belastungen ein Turbolader ausgesetzt ist.
Trotzdem ist der Turbolader kein Verschleißteil. Er kann durchaus ein Motorleben lang halten. Warum sahen wir dennoch so viele Turboladerschäden, als wie bei Motair in Köln durch die Hallen der Instandsetzung gingen? Die Antwort ist einfach und vielleicht die wichtigste Erkenntnis dieser Recherche. Weil sie kaputt gehen, wenn etwas anderes im Bereich des Motors nicht stimmt. Sollten sie ein zweites Mal kaputt gehen, wurde dieses Problem nicht behoben oder ein neues eingebaut.

Natürlich kann auch bei einem Turbolader ein Problem während Produktion aufgetreten sein, aber um diese Fälle geht es nicht. Uns geht es um fehlerfreie Turbolader. Solltet ihr einen defekten Turbolader haben, lohnt es sich durchaus, jemand erfahrenen zu Rate zu ziehen. Anhand des Schadensbildes kann oft ziemlich genau gesagt werden, was passiert ist und ob ein Materialfehler vorlag oder eben die Ursache woanders liegt. Der solltet ihr dann dringend nachgehen.
Wir wollen euch im Folgenden die Funktion und den Aufbau eines Turboladers erklären, häufige Ursachen von Turboladerschäden aufzeigen und Tipps für den richtigen Umgang geben.
Ungeduldige können gleich zu den Abschnitten springen, die sie interessieren:
- Wozu der Turbolader dient
- Aufbau eines Turboladers
- Funktion des Turboladers
- Selbstdiagnose – Darf die Welle Spiel haben?
- Häufige Ursachen für einen Turbolader-Defekt
- Was für ein langes Turbolader-Leben wichtig ist
- Was bei einer Reparatur und einem Austausch zu beachten ist
Wozu der Turbolader dient
Motoren werden in Saugmotoren und aufgeladene Motoren unterteilt. Der Saugmotor zieht seine Verbrennungsluft durch den Unterdruck selbst ein, der während des Herunterschnellens des Kolbens im Ansaugtakt im Zylinder entsteht. Anders der mit einem Turbolader zwangsbeatmete Motor. Bei diesem presst der Turbolader die Frischluft mit Überdruck in den Zylinder. Dadurch können mehr Anteile Luft mit dem für die Verbrennung wichtigen Sauerstoff in den Zylinder gelangen. Die Verbrennung wird effizienter und in Folge entsteht mehr Leistung.
Dazu entnimmt der Turbolader dem Abgas Energie über das Turbinenrad. Die Drehung wird über eine Welle auf das Verdichterrad übertragen. Auf der Verdichterseite wird dann die gefilterte Luft verdichtet und der Verbrennung zugeführt.
Aufbau eines Turboladers
Der Turbolader kann grob in vier Bereiche geteilt werden, dem Turbinengehäuse mit der Abgasturbine, dem Verdichtergehäuse mit dem Verdichterrad und dem Lagergehäuse mit der Lagerung zwischen Turbine und Verdichter. Der vierte Teil ist nicht bei allen Turboladern vorhanden, die Ladedruckregelung, wenn der Turbo variabel ist. In dem Lagergehäuse zwischen beiden Teilen befindet sich die Wellenlagerung und Kühlung.
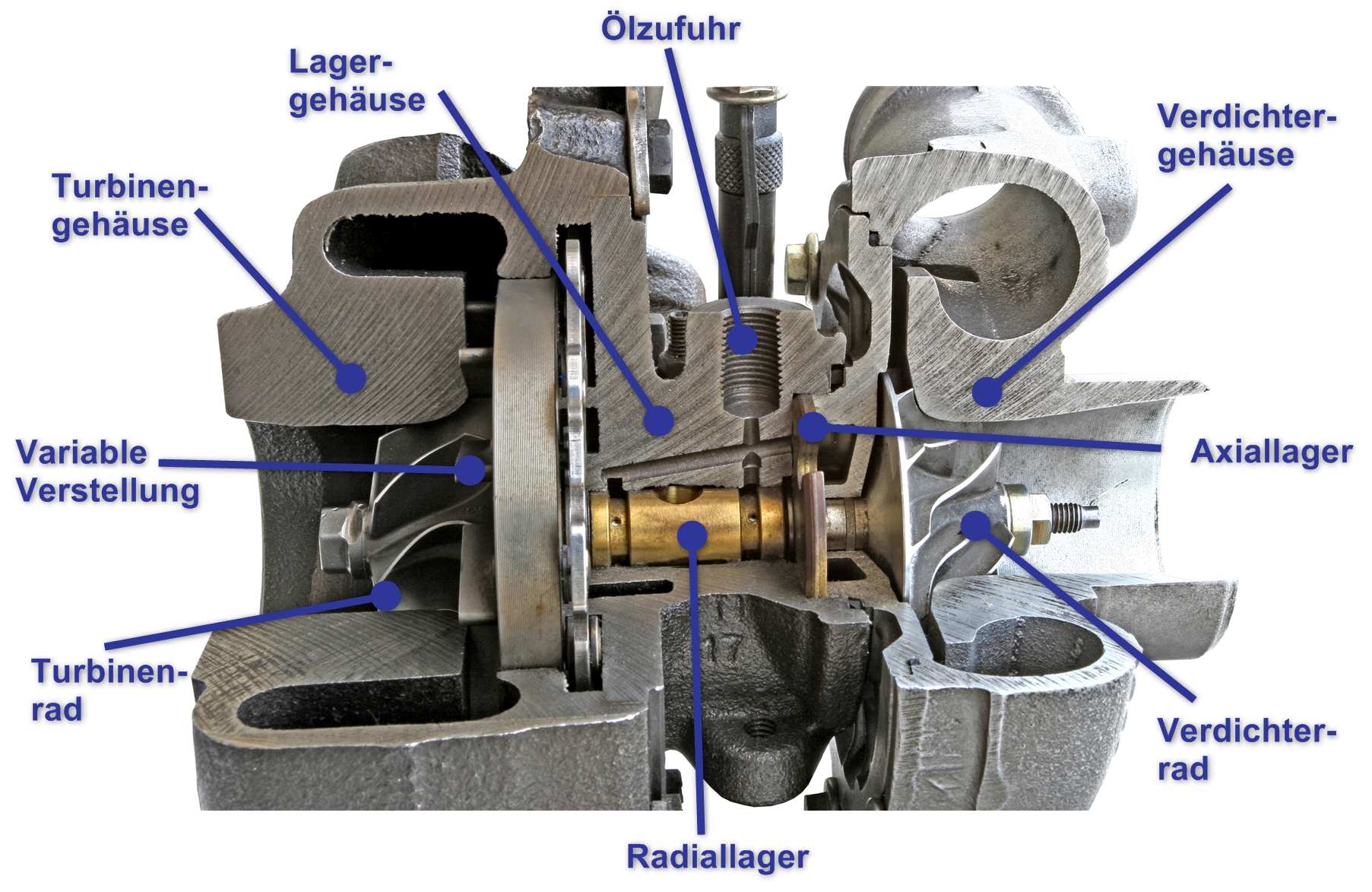
Funktion des Turboladers
Die Abgasturbine wird von den ausgestoßenen Abgasen in schnelle Rotation versetzt. Über die Welle ist die Turbine mit dem Verdichter verbunden. Dort wird die Verbrennungsluft komprimiert und dabei erwärmt. Die typischen Drücke, die ein Diesel-Turbo aufbaut, liegen zwischen ein und zwei Bar.
Ladedruckregelung
Üblicherweise gibt es zwei Ladedruckregelungen. Die eine arbeitet mit einem Bypass. Der begrenzt den maximalen Ladedruck, indem er eine Teilmenge des Abgases an der Turbine vorbei leitet, wenn der maximal erlaubte Ladedruck erreicht wurde. Der Bypass funktioniert über eine Druckdose und eine Hebelmechanik.
Besitzt der Turbolader eine elektronische Ladedruckregelung, wird der Strömungsquerschnitt des Kanals zum Turbinenrad verändert. Bei niedrigen Drehzahlen wird der Querschnitt verengt und somit die Strömungsgeschwindigkeit des Abgas erhöht. Auf diese Art, kann auch bei geringer Drehzahl und wenig Last ein Ladedruck erzeugt werden, der mehr Kraft erzeugt. Bei höheren Drehzahlen und höherer Last wird der Querschnitt wieder vergrößert.
Ladeluftkühlung
Da in erwärmter Luft weniger Sauerstoff pro Volumeneinheit vorhanden ist, als in kühlerer Luft, ist dem Turbolader ein Ladeluftkühler nachgeschaltet. Damit der leistungssteigernde Effekt durch die höhere Luftmenge nicht durch deren Erwärmung zunichte gemacht wird, kühlt der Ladeluftkühler die Luft wieder ab, so dass der Sauerstoffanteil steigen kann.
Die Welle und ihre Lagerung
Die am stärksten belasteten Teile des Laders sind seine Welle und deren Lager zwischen Turbinenrad und Verdichterrad. Gerade den Lagern kommt eine besondere Bedeutung zu. Sie müssen die Welle in axialer und radialer Richtung nahezu spielfrei führen. Die hydrodynamischen Lager nutzen das Prinzip des Öldruckpolsters, sobald sich die Welle dreht. Das Motoröl sorgt für die Schmierung, Dämpfung und Kühlung des Lagersystems.

Turbolader verwenden dazu mindestens zwei Lager, eines für die radiale und das andere für die axiale Führung. Das Radiallager ist heutzutage meist als Schwimmbuchsenlager ausgeführt. Das Gehäuse bildet den stehenden Teil des Lagers. Durch einen kleinen Spalt getrennt, dreht darin eine gelochte Messingbuchse mit circa der halben Wellengeschwindigkeit mit. In der Buchse läuft die Welle. In dem Spalt zwischen Lager und Buchse und Buchse und Welle, die beide nur wenige Hundertstelmillimeter breit sind, ist ein Ölfilm. Der verhindert zu jeder Zeit, dass es zu einem Kontakt zwischen Welle, Buchse und Lager kommt. Ein weiterer Effekt dieser Konstruktion ist es, dass sich die Welle automatisch mittig zentriert. Die Welle dreht so vollkommen verschleißfrei. Ein Effekt, den wir später beim Thema Selbstdiagnose noch einmal ansprechen.
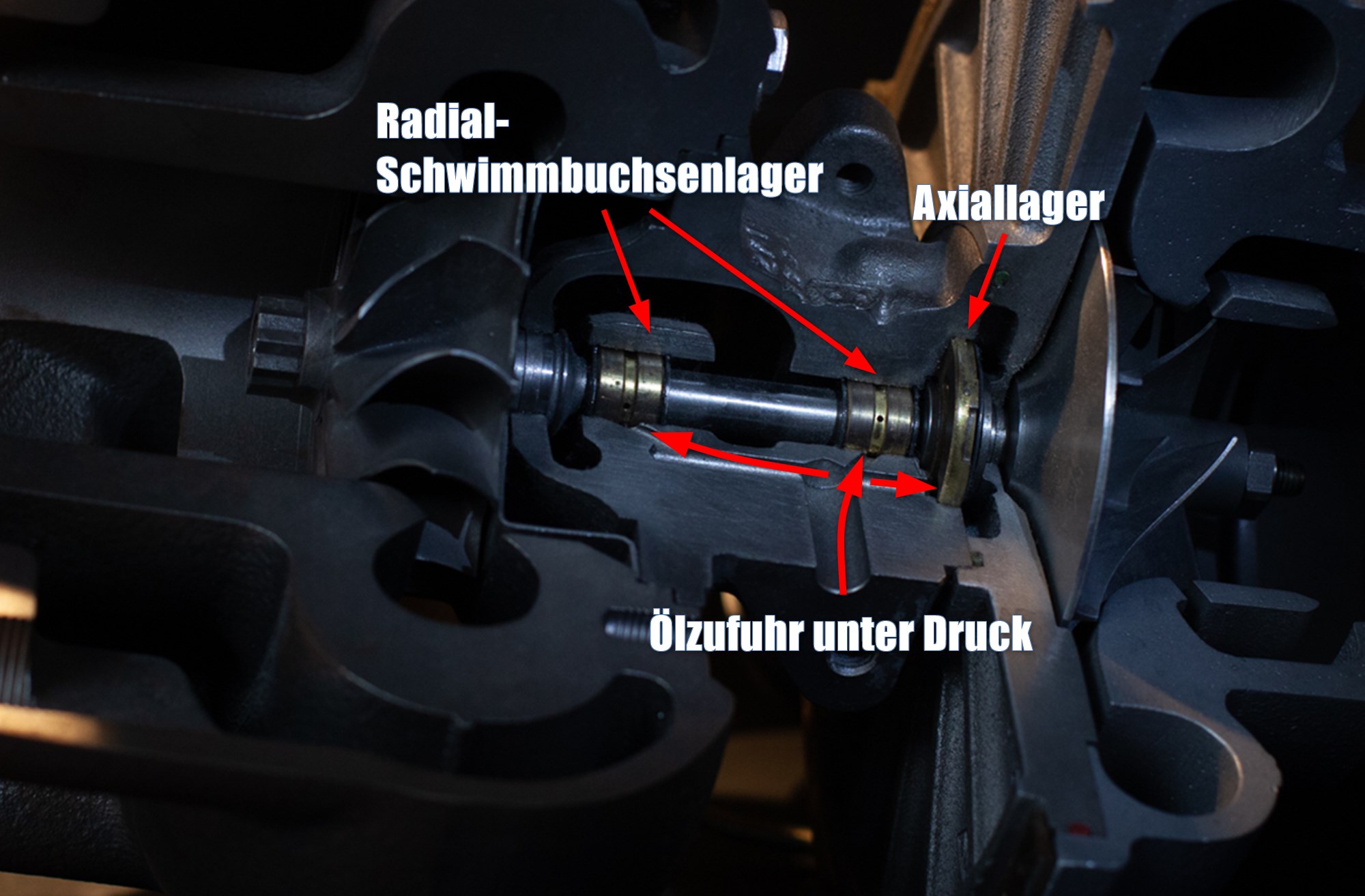
Eine weitere Form der Lagerung ist die Einbuchsenlagerung, bei der sich die Welle innerhalb einer stehenden Buchse dreht, die von außen mit Öl umspült wird. Auch hier läuft die Welle durch den geschmierten Spalt zwischen ihr und der Buchse verschleißfrei. Diese Bauart ist platzsparender.
Das axiale Lager verhindert, dass sich die Welle mit den Schaufelrädern je nach Gasdruck auf den beiden Seiten seitwärts verschiebt. Das Lager ist als gleitendes Mehrkeilflächenlager ausgelegt, das die seitwärts wirkenden Kräfte aufnimmt und am Gehäuse abstützt. Das Lager ist entweder als ein einzelnes Lager zentral oder zu beiden Seiten des Lagergehäuses angeordnet und wird ebenfalls von Öl umspült.
Die Abdichtung der Welle
Zur Abdichtung gegen austretendes Öl aus dem Lagergehäuse und eintretende Abgase in das Lagergehäuse werden mit dem Gehäuse verspannte Kolbenringe eingesetzt. Zusammen mit nach innen laufenden Nuten auf der Welle bilden sie ein Labyrinth, dass das Öl immer wieder nach innen führt und so einen Austritt verhindert.
Der Schmiermechanismus ist so ausgelegt, dass er kein Öldruck auf diese Dichtungen erzeugt. Das Öl wird zwar mit Druck in das Lager gepresst, sobald es aber das Lager verlässt, ist es druckfrei und läuft der Schwerkraft folgend wieder zurück in die Ölwanne. Es wird kein Öl im Lagergehäuse gegen die Lagerdichtungen nach außen gedrückt. Das bedeutet auch, dass ein Turbolader kein Öl aktiv nach außen fördert, wie es häufig angenommen wird.
Manchmal werden weitere Dichtmaßnahmen eingesetzt, so beispielsweise Gleitringdichtung (nur auf der Verdichterseite möglich). Dichtungen, die Kontakt zu der Welle haben, sind auf Grund der hohen Drehzahlen immer noch nicht realisierbar.
Selbstdiagnose – Darf die Welle Spiel haben?
Grundsätzlich hat ein Turbolader nur Spiel, wenn sich kein Öl in den Lagern befindet und er steht. Wenn er öldurchflossen arbeitet und dreht, hat er kein Spiel mehr, sondern definierte Spaltmaße zwischen den Rädern und den Gehäusen.
Könnt ihr aber selbst feststellen, ob euer Turbo zu viel Spiel hat oder nicht? Jain, das ist sehr schwierig. Natürlich gehört dazu viel Erfahrung. Gerade wenn der Turbo noch eingebaut ist. Wer zum ersten Mal an der Welle zieht und drückt kann nicht sicher beurteilen ob das Spiel nun viel oder wenig ist. Auch messtechnisch ist da nicht viel zu machen, da für die meisten PKW-Lader gar keine Sollwerte bekannt gegeben werden.
Wenn wirklich schon deutlich ein Spiel zu fühlen ist, dürften auf jeden Fall auch Schleifspuren am Gehäuse und den Rädern zu sehen sein, denn die berühren eher das Gehäuse, als dass so einfach Spiel zu spüren ist.
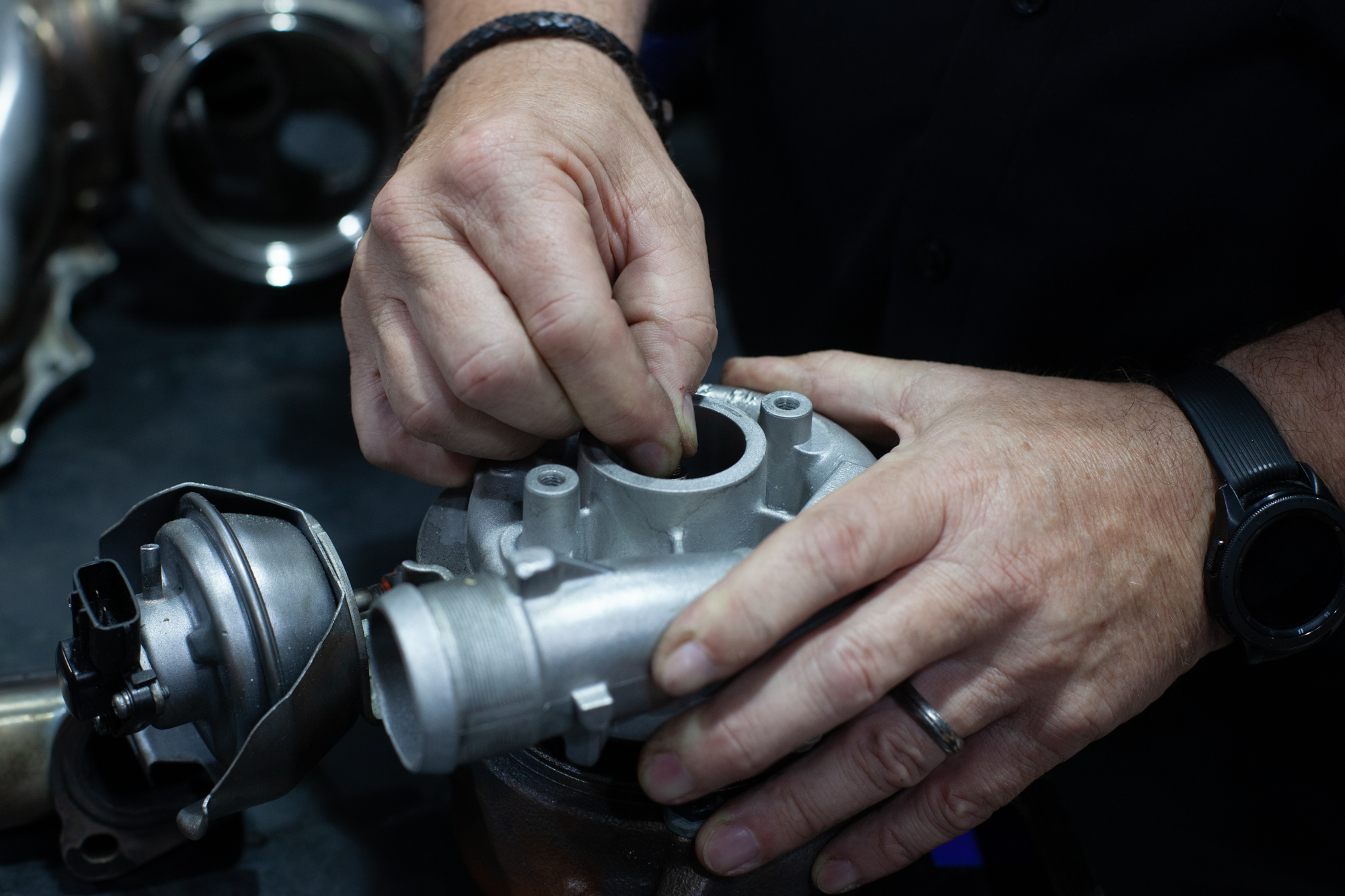
Radiales Spiel
Trotzdem gucken wir uns zunächst das radiale Spiel (auf und ab) an. Da ist immer etwas Spiel zu fühlen. Warum? Wie oben beschrieben, besitzt das Radiallager ein oder zwei kleine Spalten. Dazwischen ist Öl. Was passiert nun, wenn ihr die Welle auf- und abdrückt, um das Spiel festzustellen? Zunächst ist kaum eines zu spüren. Dann wird es mehr. Vielleicht ruft ihr einen Freund, der fühlt dann auch und merkt gleich das größere Spiel. Nur um sicher zu gehen, wird der Dritte zu Rate gezogen und der merkt noch mehr Spiel. Alle sind sich einig, der Turbo muss getauscht werden.
Was aber in Wirklichkeit geschah ist, dass ihr mit dem ersten Wackeln, den dünnen Ölfilm aus dem Radiallager gedrückt habt und neues kommt jetzt nicht mehr nach. Mit jedem weiteren Wackler drückt ihr mehr Öl aus dem Lager, bis es leer ist und dann fühlt ihr das Spiel des Lagers ohne Öl. Festzustellen, ob es sich dann um Verschleiß handelt oder nicht erfordert mindestens sehr viel Erfahrung und dazu müsst ihr schon ein einige intakte als auch kaputte Lager „gefühlt“ haben.
Axiales Spiel
Das axiale Spiel (ziehen und drücken) darf im Grunde gar nicht zu fühlen sein. Einfach, könnte man meinen. Im Selbstversuch musste ich allerdings feststellen, dass die Sache nicht so leicht ist. Ich musste im Blindtest bei verschiedenen Ladern sagen, ob axiales Spiel da ist oder nicht. Ich fühlte überall ein axiales Spiel, obwohl zwei von dreien keines hatten. Das liegt daran, dass mit den Fingern schon sehr exakt gefühlt werden muss. Nur allzu leicht bewegt man die Welle auch auf und ab und fühlt dann das kleine radiale anstatt des axialen Spiels.
Ist der Lader ausgebaut, drückt ihr vor dem Test besser etwas Öl über den Versorgungsanschluss in die Lager. Packt die Welle an an beiden Enden, um ein genaueres Gefühl zu haben.
Auf Schleif- und Pfeifgeräusche achten
Aussagekräftiger als nach dem Wellenspiel zu suchen, ist es mit der Welle das Verdichterrad zu drehen und zu hören und zu fühlen, ob das Rad schleift. Bei heutigen Turboladern beträgt der Abstand zwischen Schaufelrad und Gehäuse nur einen Bruchteil eines Millimeters (circa 6/10 mm). Hört ihr Schleifgeräusche, muss der Lader getauscht werden, dann berührt das Schaufelrad das Gehäuse und eines der beiden Spiele ist zu groß. Auch nach verbogenen oder auch (sehr sauber) ausgeschliffenen Schaufelblättern oder Schleifspuren am Gehäuse sollte gesehen werden. Ist der Lader ausgebaut, solltet ihr vor dem Test manuell Öl in die Lager drücken, damit die Welle sich zentriert, bevor ihr sie dreht.
Hört ihr beim eingebauten Turbolader während des Motorlaufs ein auffälliges Pfeifgeräusch, zumal wenn es vorher nicht da war, das leicht verzögert mit der Motordrehzahl mitgeht, ist das ein Zeichen für ein Problem. Normalerweise laufen Turbolader nahezu geräuschfrei. Ist ein Pfeifen zu hören, deutet das auf verbogene oder beschädigte Schaufeln oder eine Undichtigkeit hin. Das muss einen Grund haben und der sollte schleunigst behoben werden.
Ursache kann auch eine Winternacht mit Frost gewesen sein. Wenn sich im Turbolader Kondenswasser gebildet hat, können die Schaufelräder festfrieren. Beim Motorstart reißt sich das Schaufelrad los und dabei können sich Schaufeln verbiegen. Eine weitere Ursache für Pfeifgeräusche kann ein dünner Ölfilm sein, der sich am Verdichtergehäuse durch die Fliehkraft gebildet hat.
Häufige Ursachen für einen Turbolader-Defekt
Was sind die Ursachen für einen Turbolader-Defekt? Herr Jüngling, Technischer Leiter bei Motair in Köln, der seit vielen Jahren Turboladerschäden für Industrie und gewerbliche Kunden analysiert, sagte uns, dass in den allermeisten Fällen gar nicht der Turbo selbst ein Problem hatte. Meistens sind es Dinge, die vom Motor oder den Anschlüssen herrühren. Kurz gesagt, ein Turbolader hat sechs oder, wenn er wassergekühlt ist, acht Anschlüsse. Diese Anschlüsse und alles was darüber den Turbo erreicht, müssen in Ordnung sein. Was bedeutet das in der Praxis?
Mangelnde Schmierung führt zum Turbolader-Defekt
Da wäre zuallererst die Schmierung zu nennen, die auch für die Kühlung verantwortlich ist. Das Öl muss stetig zu der Welle gefördert werden und ablaufen können. Es gibt mehrere Gründe für ein Problem bei der Schmierung. Das reicht von verstopften Filtersieben in den Ölkanälen, über falsches, verdünntes oder veraltertes Öl bis hin zu defekten Ölpumpen.
Verstopfte Siebe können durch mangelnde Wartung entstehen. Wird das Öl nicht regelmäßig gewechselt, können sich am Boden der Ölwanne zunehmend Partikel absetzen, die irgendwann der Pumpe Probleme machen oder eben Siebe verstopfen. Werden die Ölfilter nicht gewechselt, setzen diese sich irgendwann so zu, dass ein Bypass-Ventil im Filter das Öl ohne Filterung weiter zirkulieren lassen muss. Die Partikel bleiben im Kreislauf.
Bei den Pumpen können Probleme durch eingelaufene und verschmutze Pumpenräder auftreten, wodurch die Förderleistung reduziert wird. Bleibt das Überdruckventil der Ölpumpe im geöffneten Zustand hängen, entweicht zu viel Öl über das Ventil und der Öldruck wird zu niedrig. Der Motor toleriert das, sogar Aussetzer der Pumpe machen ihm in der Regel nichts. Der Turbolader wird im Falle des Falles jedoch zuerst den Schaden erleiden. Bei elektrischen Pumpen, wie sie Stopp-Start-Fahrzeuge verwenden, kommen dann noch sämtliche Mysterien der KFZ-Elektrik als Ursache für einen Turbolader-Defekt in Frage, inklusive der unvermeidlichen Alterung von Kabeln.
Ölverdünnung
Verdünntes Öl tritt gerade bei Dieselfahrzeugen auf, die viel Kurzstrecke fahren. An den Kolben vorbei gelangt immer etwas Treibstoff in den Ölkreislauf. Heutige Steuergeräte berechnen anhand des Fahrprofils, wann ein Ölwechsel fällig wird. Das dient auch dem Zweck, durch Diesel verdünntes Öl auszutauschen. Bei Benzinern tritt das Problem seltener auf, da das Benzin sich schneller verflüchtigt, ebenso bei Fahrzeugen, die regelmäßig über längere Strecken bei Betriebstemperatur gefahren werden.
Durch Kraftstoff oder Wasser verdünntem Öl fehlt die Schmierfähigkeit und Druckfestigkeit.
Das Öl selbst als Ursache
Das Öl muss der verlangten Spezifikation entsprechen, damit es in dem dünnen Schmierspalt der Lager funktioniert und auch mit den Temperaturen klarkommt. „Vernachlässigte Wartung und falsches Öl“ sind die häufigsten Ursachen, erklärt der Chef der Instandsetzung Jüngling.
Insbesondere zwei Angaben sind beim Öl entscheidend. Das ist zum einen die Viskosität. Heute werden fast ausschließlich Mehrbereichsöle gefahren, die einen unteren und einen oberen Viskositätswert haben. Im Zweifel solltet ihr darauf achten, dass zumindest der obere Viskositätswert stimmt, da dieser über die Zeit absinkt. Wird das Öl zu flüssig, kann es immer weniger Druck aufnehmen und es kann zum Abriss des Schmierfilms kommen.
Der zweite Wert ist die Spezifikation. Sie ist gerade bei Fahrzeugen mit Turbolader, Katalysator oder Partikelfilter wichtig, denn die Öle sind so abgestimmt, dass sie mit den hohen Temperaturen und Scherwirkungen im Turbo klarkommen und weder Katalysator oder Partikelfilter beschädigen. Gerade auch was die Aschelast im Partikelfilter angeht, ist das richtige Öl wichtig. Die Aschelast kann, wie weiter unten beschrieben, ebenso zu einem Turbolader-Defekt führen.
Motorentlüftung mit geregeltem Unterdruck
In den 1960er Jahren wurden geschlossene Motorentlüftungen eingeführt. Blow-By-Gase, die bei der Verbrennung in den Zylindern zwischen Kolbenring und Zylinderwand entweichen, müssen abgeführt werden. Vor der Einführung der geschlossenen Systeme ließ man die Blow-By-Gase einfach in die Atmosphäre entweichen. Seitdem werden diese ölhaltigen Gase dem Frischluftstrom zum Turbolader zugeführt und anschließend verbrannt. Zunehmend arbeiten diese Systeme mit genau geregeltem Unterdruck. Sie müssen über eine große Bandbreite unterschiedlichster Druckverhältnisse sicher funktionieren, wobei der Grat zwischen Funktion und Störung weniger als ein Millibar betragen kann.
Funktioniert das Regelsystem nicht mehr einwandfrei, kann es zu einem Ölrückstau im Rücklauf des Turbos kommen. Die Druckverhältnisse im Turbo stimmen dann nicht mehr, die Folge sind Ölleckagen. Eine gestörte Druckregelung der Entlüftung macht sich aus verschiedenen Gründen durch einen erhöhten Ölverbrauch bemerkbar, u.a. weil die Abscheidung des Öls aus dem Ölnebel nicht mehr ordentlich funktioniert und mehr Öl verbrannt wird.
Axiallagerschaden durch Überdruck
Das Axiallager nimmt den axialen (seitlichen) Druck, der auf der Welle lastet, auf. Ist der Druck auf der Turbinenseite dauerhaft zu groß, wird das Turbinenrad ständig Richtung Lagergehäuse gedrückt. Das führt zunächst zum Einlaufen des Axiallagers und in Folge tritt axiales Spiel auf. Das wiederum ermöglicht zum einen, dass das Verdichterrad das Gehäuse berührt und anfängt dort zu schleifen. Zum anderen, dass das Turbinenrad Kontakt zu dem Hitzeschild bekommt und dort durch die Reibung zusätzlich thermisch und mechanisch belastet wird. Als Resultat wird die Ölabdichtung beschädigt, es kommt zum Ölübertritt und letztendlich führt das Ganze zu defekten Rädern und möglicherweise auch zu einem Wellenbruch.
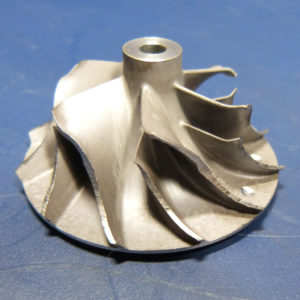
Auch Dieselpartikelfilter führen zum Turbolader-Defekt
Eine versteckte, aber zunehmend anzutreffende Ursache für eine einseitige Belastung ist ein verstopfter Dieselpartikelfilter. Entweder, weil er nicht frei gebrannt wurde oder durch die Aschelast bei zunehmender Laufleistung. Die Asche wird nicht verbrannt, sondern bleibt im Partikelfilter zurück und erzeugt über die Jahre einen steigenden Gegendruck. Daher sollte auch dem Dieselpartikelfilter bei der Wartung Aufmerksamkeit geschenkt werden. Auch andere Motorbereiche, wie Zylinderkopf und Ventile, können Schaden nehmen, wenn der Motor durch einen verstopften Partikelfilter nicht mehr in der Lage ist, genügend Hitze abzuführen.
Overspeeding
Turbolader reagieren sehr empfindlich auf zu hohe eigene Drehzahlen. Die Folge zu schnellen Drehens ist, dass das Verdichterrad regelrecht wächst. Die überhöhte Drehzahl sorgt für stärkere Fliehkräfte, die das Rad anwachsen lassen, bis es das Gehäuse berührt. Das ist teilweise überhaupt nicht zu erkennen, da die Kanten so sauber abgeschliffen werden, dass es wie „ab Werk“ aussieht.
Ein Symptom kann ein Pfeifen sein, da die Schaufeln nun eine andere Form haben, aber es muss nicht pfeifen. Ein anderes Symptom sind Schleifgeräusche nach längerer Fahrt mit hohen Drehzahlen. Dass Verdichterrad hat sich ausgedehnt und schleift sich noch aus, bis es wieder auf Originalgröße schrumpft. Das Schleifen verschwindet irgendwann, der Schaden bleibt. Es ist möglich, dass das Verdichterrad in Folge komplett zerreißt.
Overspeeding kann man erkennen, wenn man sich die Rückseite des Verdichterrades betrachtet und anstatt einer makellosen glatten Oberfläche kleine Dellen und Unregelmäßigkeiten in der Farbe erkennt, wie bei einer Orangenschale. Dann kam es zu einem Materialfluss, der die Oberfläche verformt hat.
Im Folgenden führen wir einige Ursachen für Overspeeding auf:
Defekte Verstellung
Wenn der Mechanismus für die variable Turboladereinstellung klemmt oder durch elektrische/elektronische Probleme keine Ansteuerung mehr erfolgt, kann es zu zwei Problemen kommen. Bleibt die Verstellung im offenen Zustand stehen, verliert ihr Leistung im unteren Drehzahlbereich. Das ist nicht schön, aber zumindest ungefährlich. Bleibt die Verstellung aber im geschlossenen bzw. verengten Zustand stehen, wird auch bei höheren Drehzahlen das Abgas zusätzlich beschleunigt. Das führt dann zum Overspeeding. Auch hier können wieder lose Partikel die Ursache für ein Festklemmen der Verstellung sein.
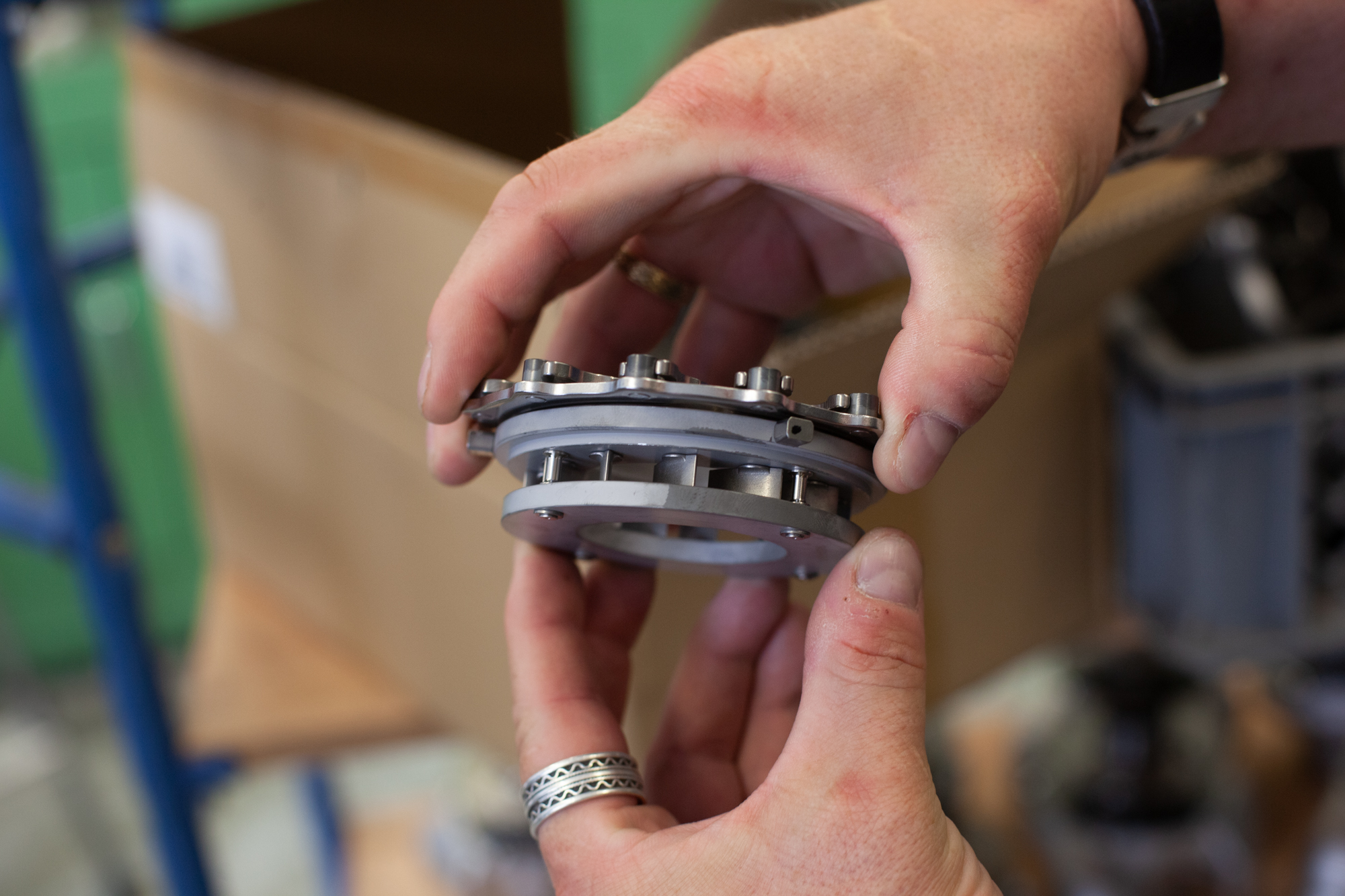
Undichte Schläuche Ladeluftseite
Poröse oder geplatze Schläuche auf der Ladeluftseite sind mit die häufigste Ursache für einen Turbolader-Defekt. Auch hier spielt die Verstellung wieder eine Rolle. Entweicht unmerklich auch nur wenig Luft auf der Ladeluftseite, also bei der Frischluft zwischen Turbolader und Motor, stellt die Steuerelektronik einen zu geringen Ladedruck fest und regelt nach. Sie verengt über die Verstellung den Querschnitt und die Turbine läuft schneller. Irgendwann läuft sie dann zu schnell.
Platzt ein Schlauch, kann es auch zu einem kurzzeitigen, aber extremen Hochdrehen des Laders kommen. Bei Motoren ohne Elektronik, hilft dann nur sofort den Fuß vom Gaspedal zu nehmen. Bei Fahrzeugen mit Steuergerät schaltet es in dem Notlauf und kappt die Leistung. Dennoch kann es in beiden Fällen zu spät sein, insbesondere wenn die Fahrzeugelektronik vor dem Notlauf erst die Turbo-Drehzahl hochgeregelt hat.
Eine weitere Folge kann auch der oben beschriebene Axiallagerschaden sein, da der Gegendruck auf der Verdichterseite fehlt, wenn ein Schlauch kaputt geht. Allerdings gehen Fahrzeuge mit Steuergeräte in solchen Fällen in den Notlauf und nehmen die Leistung raus, um die Drehzahl zu begrenzen und eine längere Weiterfahrt zu verhindern.
Tuning
Wurde dem Motor zusätzlich Leistung per Chiptuning verpasst, kann das die Lebensdauer des Turboladers verkürzen. Durch das Tuning kann nicht nur die Drehzahl des Turbos in unzulässige Bereiche gesteigert werden, es kann auch die Abgastemperatur zu heiß werden. Je nachdem wie hoch sie ansteigt und wie oft ihr den Turbo damit belastet, ist auch hier die Folge ein frühzeitiges Ableben. Daher gehört zu einem vernünftigen Tuning, gerade wenn es erheblich die Leistung steigert, auch eine Abgastemperaturmessung. Sie ist letztendlich der einzige Indikator. Noch besser ist es, wenn ihr die Abgastemperaturen eures Fahrzeugs unter normalen Bedingungen kennt. Dann könnt ihr besser einordnen, wie hoch die Temperatursteigerung durch das Leistungsplus ist. Nur schwer und nur mit viel Erfahrung ist daraus abzuleiten, was dem Turbolader zugemutet werden kann.
Lose Bruchteile, Partikel und Staub
Alles was, außer Luft, den Turbolader auf der Abgas- oder Verdichterseite erreicht, kann zu Schäden führen. Ein unachtsam vergessenes Stück Putzlappen im Luftfilterkasten, eine kleine Schraube die dort hineingefallen ist oder Sand und Staub, der durch undichte Verbindungen am Luftfilter vorbei ins Innere dringt. Diese Teile können ein Pfeifen verursachen, weil sie ein Schaufelrad verbogen haben. In Folge entsteht eine Unwucht, die langsam das Lager kaputt macht. Sie können sich aber auch stetig durchschleifen und das Schaufelrad regelrecht wegarbeiten. Oder sie führen zu einer Blockade, dann bleibt der Lader abrupt stehen, mit der Gefahr, dass Teile brechen.
Aber auch Schäden im Motor wie kaputte Ventile, AGR-Klappen und Kolbenringe zerstören den Turbolader, wenn deren lose Bruchstücke ihn erreichen. Davor könnt ihr euch nicht wirklich schützen, aber wenn die Reparatur erfolgt, müssen alle Fragmente entfernt, der Motor gereinigt und alle Wege zum Turbo sauber sein.
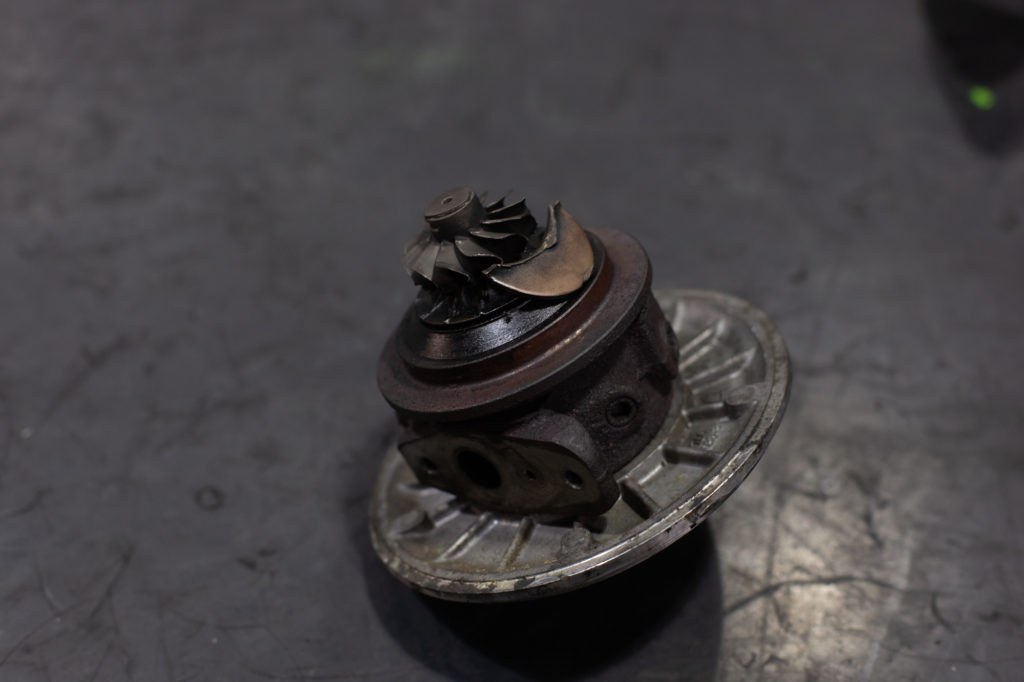
Sogar wenn an anderen Teilen als dem Turbo gearbeitet wird, können unbemerkt abfallende Beläge, harte Verkrustungen oder Rostpartikel später für einen Turbolader-Defekt sorgen. Dazu muss nur jemand den Abgaskrümmer mit dem Gummihammer lösen und ihn ohne zu reinigen wieder montieren und schon können lose Fragmente (Verzunderungen) in die Turbine gelangen.
Luftspaltisolierte Krümmer
Ein weiteres Problem auf der Abgasseite droht dem Turbo durch luftspaltisolierte Abgaskrümmer. Diese Abgaskrümmer bestehen aus einem äußeren und einem inneren dünnen Blechgehäuse. An den Öffnungen sind diese Gehäuse zusammengeschweißt. Zwischen beiden ist ein Luftspalt. Sinn und Zweck dieser Konstruktion ist es, das Abgas möglichst schnell auf eine Temperatur zu bekommen, die die Abgasreinigungssysteme zum Funktionieren brauchen. Ein Krümmer aus massivem Material benötigt dazu, nach heutigen Maßstäben, zu lange.
Das Problem des luftspaltisolierten Krümmers ist, dass er gerne an den Schweißnähten von Rost befallen wird. In Folge lösen sich kleine Rostplättchen, die so in die Turbine gelangen und das Turbinenrad zerstören.
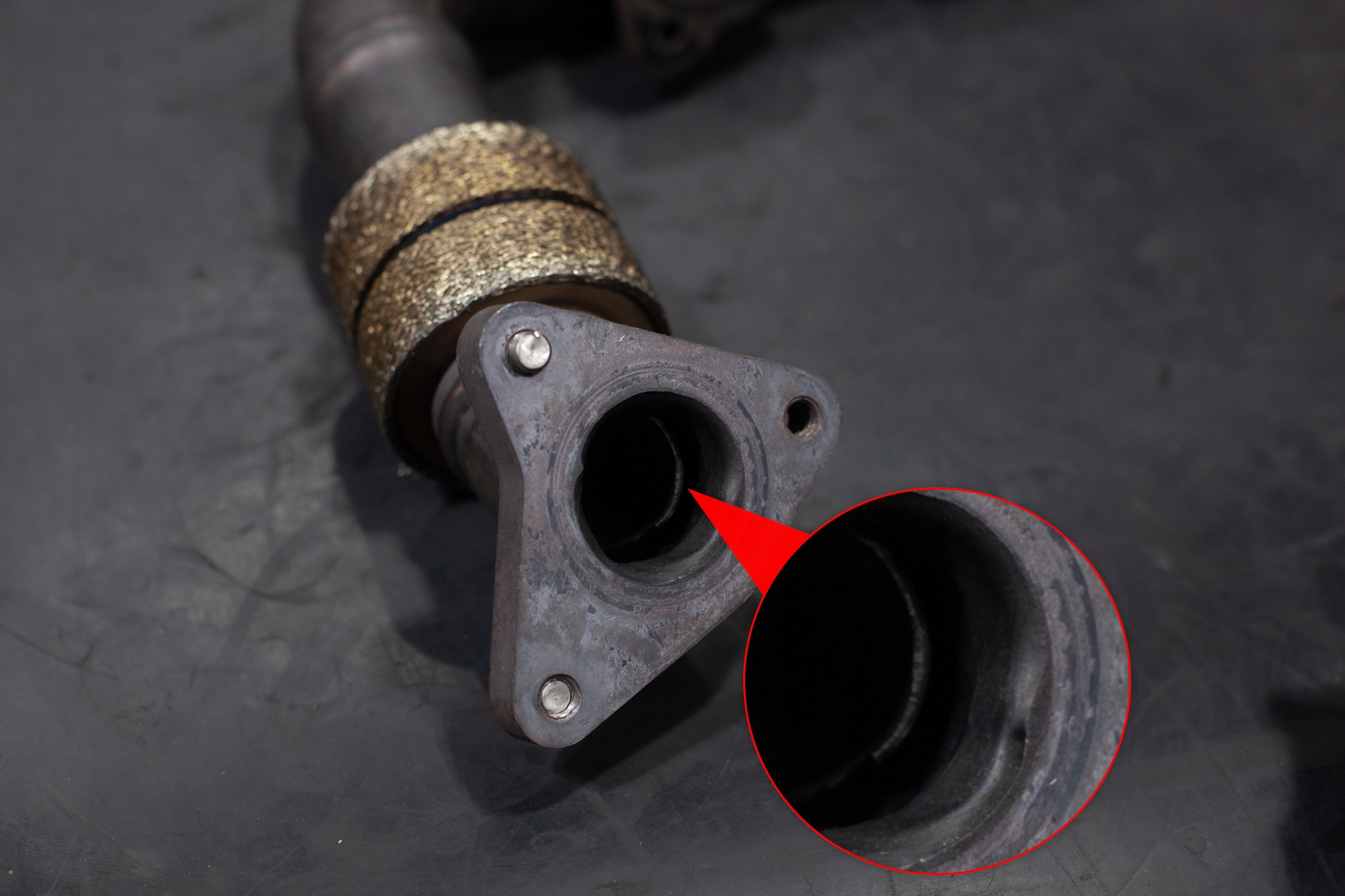
Was für ein langes Turbolader-Leben wichtig ist
Das richtige Öl und Wartung
Das Motoröl schmiert, dämpft, kühlt und zentriert die Welle des Turboladers. Dabei ist der Ölfilm, der das bewerkstelligt, nur hauchdünn. Deshalb muss es zum einen das richtige Öl sein. Welches das ist sagt euch das Handbuch eures Wagens. Dort stehen die Spezifikationen, die das Öl erfüllen muss.
Zum anderen muss Öl in den geforderten Intervallen gewechselt werden. Das Öl bleibt nicht das gleiche, auch wenn hier und da behauptet wird es müsste nur gut genug gefiltert werden. Das ist falsch. Das Öl wird mechanisch, thermisch und chemisch beansprucht. Scherwirkungen zerstören die Molekülketten und senken die Viskosität über die Zeit ab. Die Folge dessen ist, dass das Öl mit zunehmender Kilometerleistung immer weniger Druck aufnehmen kann. Wo Öl dem Druck weicht, kommt es zu Verschleiß. Natürlich hat es Reserven, aber diese machen einen Ölwechsel nicht unnötig. Die thermische und chemische Belastung verändert das Öl ebenfalls. Es entstehen beispielsweise Säuren, die gebunden werden müssen. Sind die Additive im Öl verbraucht, greifen diese Säuren die Beschichtungen und Metalle an.
Achtet darauf, das geforderte Öl zu verwenden und die Wechselintervalle einzuhalten. Dabei müsst ihr insbesondere auf die richtige Spezifikation und die richtige Viskosität achten. Bekommt ihr im Notfall kein Öl in der richtigen Viskosität, sollte zumindest der obere Wert stimmen, also bei einer Angabe von 5W30 die 30.

Mehr über das Thema Öl, Viskosität und Spezifikation findet ihr in meinem Artikel zum Öl.
Beobachtet die Ölmenge im Motor. Je nach Aufbau eines Motors, kann es Stellen geben, die bei einem Defekt zusätzlich Treibstoff in das Öl durchlassen, beispielsweise bei Pumpe-Düse-Motoren, wo der Diesel im Motorblock zirkuliert. Das Öl wird zu stark verdünnt und verliert seine Schmierwirkung. Bei einem Anstieg der Ölmenge oder starkem Treibstoffgeruch des Öls solltet ihr zügig der Ursache auf den Grund gehen.
Warmfahren und Abkühlen
Hier könnte man „Langsam ist gut“ sagen. Nacht dem Starten des Motors dauert es ein paar Sekunden, bis an allen Stellen der Öldruck stabil ist und ein ausreichender Schmierfilm anliegt. Beim Motorstart durchlaufen alle Reibstellen unterschiedliche Schmier- und Reibzustände bis der gewünschte Betriebszustand erreicht ist. Das betrifft nicht nur den Turbolader. Je länger der Motor gestanden hat, desto länger dauert es. Ihr solltet daher nach dem Motorstart nicht gleicht aufs Gas gehen, sondern lasst den Motor ein paar Sekunden im Standgas laufen, bevor ihr abfahrt. Wenn es geht, vermeidet zu früh zu hohe Last vom Motor zu verlangen. Als extremes Beispiel sei eine Übernachtung auf dem Autobahnrastplatz im Winter genannt. Wenn es gleich mit viel Gas losgeht, erzeugt ihr große Temperaturunterschiede im Turbolader. Natürlich sind sie auch für solche Fälle ausgelegt, aber besser ist es, den Motor langsam warm zu fahren.
Gleiches gilt für das Fahrtende. Wenn ihr den Motor hoch belastet und entsprechend hohe Temperaturen erzeugt habt, solltet ihr nicht Anhalten und gleich den Motor abschalten. In diesem Fall kann es zu einer Überhitzung im Bereich der Turboladerwelle kommen. Mit dem Abschalten des Motors stoppt sofort die Schmierung und Kühlung. Es entsteht ein Hitzestau. Da die Welle aber noch eine Weile nachdreht und sehr heiß ist, kann der Schmierfilm abreißen und es kann zu Verkokungen kommen. Beides endet im frühzeitigen Aus für den Turbolader.
Lasst nach dem Stopp den Motor noch 30 bis 60 Sekunden laufen, wenn ihr eine Fahrt direkt nach hoher Last beenden wollt. Manche Fahrzeughersteller haben dazu sogar einen Hinweis im Fahrzeughandbuch und geben dort die Auslaufzeit an. Die Welle kann so ihre Drehzahl auf Leerlaufniveau reduzieren, während sie weiter gekühlt wird. Wer eine Abgastemperaturmessung (Pyrometer) eingebaut hat, kann das Abklingen der Abgastemperatur dort gut beobachten und so besser den Temperaturverlauf kontrollieren.
Wer einen Stopp-Start-Motor hat, kann sich informieren, ob entweder eine elektrische Öl- oder Wasserpumpe (bei wassergekühlten Ladern) vorhanden ist, die nach dem Motorstopp für eine weitere Zirkulation sorgt. Diese können auch als zusätzliche Pumpe eingebaut sein. Ansonsten ist es ratsam bei Fahrten unter hoher Last, den automatischen Motorstopp abzustellen.
Luftfilter
Trotz der hohen Belastungen, die ein Turbo vertragen kann, ist er doch vergleichsweise filigran aufgebaut. Die Schaufeln der Räder sind sehr leicht und dünn, damit bei den hohen Drehzahlen nicht zu viel Masse bewegt wird. Aufgrund der hohen Drehzahlen und ihrer leichten Bauweise sind sie sehr anfällig gegen alles, was etwas fester als Luft ist. Jegliches Eindringen von Feststoffen führt früher oder später zum Tod des Laders. Auch Staubbelastung kann ein Problem werden, da sie die Dichtungen und die Wellenlagerung angreift.
Ihr solltet qualitativ gute Luftfilter einsetzen, die für das Fahrzeug vorgeschrieben sind und diese entsprechend der Wartungstabelle tauschen. Nach besonderen Belastungen, wie beispielsweise nach staubigen oder sandigen Pisten, kann der Luftfilter zunächst mit Druckluft ausgeblasen werden. Sobald möglich, sollte er dann nach außergewöhnlichen Belastungen getauscht werden.
Beim Arbeiten am offenen Luftfilterkasten sehr darauf achten, dass nichts in den Luftfilterkasten oder auf den Luftfilter fällt, was später in den Turbo gesaugt werden kann. Wenn es in der Umgebung staubt, legt einen sauberen Lappen über die Öffnung zum Turbolader.
Ab und an solltet ihr auch mal in den Luftschlauch vom Luftfilter zum Turbolader schauen. Ist dort Staub oder Sand zu sehen? In diesen Schlauch führt auch die Motorentlüftung vom Ventildeckel. Das kann ab der Verbindungsstelle einen leicht schmierigen, dünnen Ölfilm erzeugen. Es sollte aber kein Öl im Schlauch stehen. Kontrolliert auch die Luftschläuche vom Turbolader bis zum Motor. Sitzen sie richtig? Haben sie poröse oder Scheuerstellen, dann tauscht sie aus.
Was bei einer Reparatur und einem Austausch zu beachten ist
Ist es passiert und euer Fahrzeug hat einen Turboladerschaden, sind einige Dinge zu beachten. Wenn das Problem nicht mit Sicherheit direkt vom Turbo ausging, also ein Material- oder Montagefehler, liegt das Problem außerhalb des Turbos. Dieses solltet ihr unbedingt finden, da sonst die Tage des neuen Laders bereits beim Einbau gezählt sind. Allerdings werden diese äußeren Problem auch manchmal still und unbemerkt beseitigt, wenn beispielsweise ein Rohr der Ölversorgung mit getauscht wurde, das verstopft war.
Das Schadensbild sollte euch helfen, die Ursache einzugrenzen. Ist ein Feststoff eingedrungen oder hat die Schmierung versagt? Wurden die Lager überbeansprucht? Drehte der Lader zu schnell? Das Versagen eines Teils, kann natürlich Folgeschäden verursachen. So kann eine gebrochene Welle bis zu einem Bruch des Gehäuses führen. Ein Fachmann versteht sich jedoch auf das Lesen solcher Fehler.
Der alte ist dem Neuen sein Ende
In den allermeisten Fällen, wurde bei einem Schaden Material vom Turbolader selbst abgegeben, meistens von den Schaufelrädern. Dieses Material verteilt sich, entweder im Ansaug- oder im Abgasstrang. Oder in beiden. Daher müssen gerade diese Bereiche genau unter die Lupe genommen werden. Vom Luftfilterkasten, über die Kurbelgehäuseentlüftung bis zum Ladeluftkühler. Überall muss sichergestellt sein, dass keine Fragmente des alten Turbos zurückbleiben. Auf der Abgasseite ist das der Krümmer, die Leitungen zum AGR und das Hosenrohr des Auspuffs.
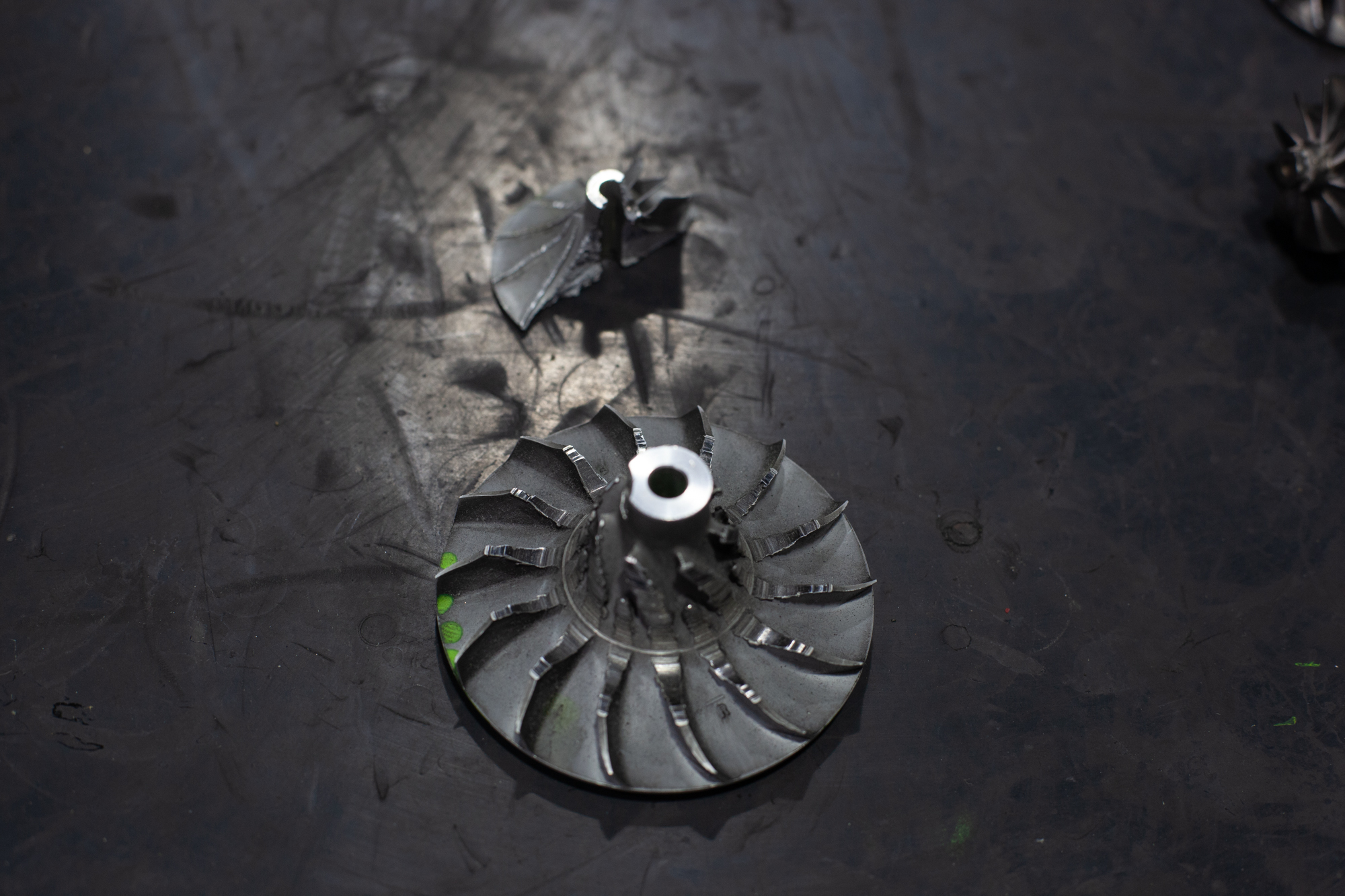
Verlorene Mutter
Ein gar nicht so seltenes Versäumnis ist, sicherzustellen, dass die Mutter der Welle entweder noch an ihrem Platz ist oder gefunden und entfernt wurde. Bei der Montage wird die Verdichterradmutter mit definiertem Drehmoment angezogen. In den allermeisten Fällen hat sie ein Linksgewinde, so dass sie sich auf der rechtsdrehenden Welle nicht lösen kann, sondern weiter festzieht.

Kommt durch eine Blockierung die Welle zu einem abrupten Stopp, kann sich die Mutter durch ihre Massenträgheit selbst vom Wellengewinde drehen und verschwindet irgendwo im Ansaugstrang. Bemerkt niemand beim Ausbau, dass sie fehlt, wird sie vom neuen Lader irgendwann angesaugt und dann ist der neue Schaden da. Die Mutter kann sogar eine lange Zeit unentdeckt herumliegen, bis sie vielleicht durch eine Bodenwelle oder ein Geländehindernis kurz angehoben wird und wieder den Weg in den Turbo findet.
Beim Einbau des Turbos kann schon etwas Motoröl in seine Zuleitung gepresst werden. Dann kann der Motor von Hand oder mit dem Anlasser ohne zu Zünden gedreht werden, um vor dem ersten Motorstart weiteres Öl zum Turbo zu fördern.
Schläuche tauschen
Sind die Schläuche auf der Ladedruckseite schon älter oder gar offensichtlich porös, müssen sie mit getauscht werden. Ansonsten droht ein (erneutes) Overspeeding.
Wenn der Lader durchdreht
Einer der gefürchtetsten Turboladerschäden ist das unkontrollierte Hochdrehen des Motors durch Ölverbrennung. Ein Effekt, der insbesondere vom selbstzündenden Dieselmotor bekannt ist. Ein Diesel wird nur über die Spritzufuhr geregelt und auch abgestellt. Kommt es zu der Situation, dass der Turbolader neben der Luft auch zu viel Öl fördert, kann der Motor nur mit dem Öl weiterlaufen. Da es keine Mengenkontrolle gibt, steigt seine Drehzahl maximal an. Das geht dann so lange bis entweder kein Öl mehr im Motor ist oder etwas anderes kaputt geht. Ein kapitaler Motorschaden ist die Folge.
Ursache kann eine komplett versagende Wellendichtung oder ein mit Öl gefüllter Ladeluftkühler sein. Kommt über den Turbolader zu viel Öl in den Ansaugtrakt, sammelt es sich über die Zeit im Ladeluftkühler, bis es soweit angestiegen ist, dass es mitgerissen wird und in die Verbrennung gelangt. Solange der Wagen fährt, ist das nicht unbedingt zu spüren, und wenn dann eher als positiver Effekt, da der Wagen kraftvoller wirkt. Wird jedoch die Last vom Motor getrennt, da ihr auskuppelt, fängt er an hochzudrehen. Das kann nur noch frühzeitig durch ein schnelles Wiedereinkuppeln und Abbremsen gestoppt werden. Im Stand den zweiten Gang einlegen, zügig die Kupplung kommen lassen, losfahren und dann den Wagen bis zum Abwürgen des Motors bremsen. Könnt ihr nicht weg, dann bei getretener Bremse die Kupplung kommen lassen und hoffen, dass es klappt.
Ein paar Dinge beachten und gute Wartung
Aus der Praxis und den Aussagen der Experten bei Motair können wir sagen: Bei guter Wartung und wenn auf die wenigen oben beschriebenen Dinge geachtet wird, kann ein Turbolader ein Motorleben lang halten. Solltet ihr nicht das Glück haben und müsst ihn früher tauschen, lohnt es sich genau hinzusehen, was den Schaden verursacht hat. Fakt ist auch, dass die zunehmende Umwelttechnologie bei Verbrennungsmotoren immer wieder für zusätzliche Probleme sorgt, an ganz verschiedenen Stellen. Daran können wir jedoch nur eingeschränkt etwas ändern.
Motair Köln – Wir bedanken uns bei Herrn Dipl.-Ing (FH) Solibieda, Geschäftsführer Motair Turbolader GmbH Köln und Herrn Jüngling, Technischer Leiter, für die freundliche und kompetente Unterstützung bei der Erstellung dieses Artikels über Turboladerschäden.
Motair wurde 1971 zur Entwicklung kleiner aufgeladener Flugmotoren entwickelt und seit seit den 1980er Jahren verstärkt im Automotive-Bereich tätig. Seit den 1990er Jahren ist Motair Marktführer für regenerierte Tubrolader in Deutschland. Motair bietet das Vollsortiment und die Instandsezung für alle Turboladerhersteller an (Garrett, 3K, Schwitzer, BorgWarner), Mitsubishi, Holset, IHI (Nationale Vertretung)). Zudem ist Motair Entwicklungspartner für Spezialapplikationen in den Bereichen Industrie, Tuning, und Rennsport. In Köln gibt es dazu ein Prüf- und Reparaturzentrum.