Das Thema Schraubverbindungen und Drehmoment ist eine komplexe Sache. Wir werden euch in diesem Artikel die Zusammenhänge, wo nötig vereinfacht, erklären, die Prinzipien zum Verständnis aufzeigen und im zweiten Teil Praxistipps zum richtigen Umgang mit Schraubverbindungen und dem Drehmoment geben.
Eines gleich vorweg: Die Entscheidende Maßnahme zur Herstellung einer haltbaren Schraubverbindung ist das richtige Drehmoment zu verwenden. Wenn irgendwo ein Drehmoment für eine Verbindung angegeben wurde, sollte es auch angewandt werden. Insbesondere bei hoch-belasteten Verbindungen, beispielsweise Zylinderköpfe, Radbolzen und Muttern oder Anhängerkupplungen. Dort sind Drehmomente angegeben und das hat Gründe. Bei gering-belasteten Verbindungen klappt es oft ohne Vorgabe, weil die „aus dem Handgelenk“ angezogene Schraube bereits so viel Drehmoment abbekommen hat, dass sie mehr als genug Klemmkraft erzeugt, um alles zusammen zu halten.
Apropos, es gibt immer wieder Schrauber, die so ein Drehmoment „aus dem Handgelenk erspüren“ können. Sagen sie jedenfalls. Tests, auf die große Hersteller und Anwender von Schraubverbindungen verweisen, wie z.B. AJAX (Australien) oder der NASA (USA), haben ergeben, dass bei zig Wiederholungen mit Berufsschraubern die Drehmoment-Abweichung beim Anziehen ohne Messmittel bei +/- 35% lag. In Anbetracht der Tatsache, dass die Hersteller von Schrauben, das sichere Drehmomentfenster bei 65% bis 75% unterhalb des Punktes festsetzen, ab dem sich die Schraube dauerhaft längt, eine nicht akzeptable Abweichung. Wenn ihr jetzt noch nicht entnervt weitergeklickt habt, könnt ihr die Zusammenhänge nachlesen und erfahren wie es richtig gemacht wird.
Wie das mit dem Anziehen und dem Drehmoment richtig geht, lest ihr bald in Teil 2, dem Praxisteil.
Die Essenz für eine Schraubenverbindung: Klemmkraft
Was ist das Funktionsprinzip hinter einer Schraubverbindung? Um zu verstehen, warum das Drehmoment wichtig ist, müssen wir erst verstehen, wie eine geschraubte Verbindung funktioniert. Generell gibt es zwei Arten von Schraubverbindungen: die auf Zug oder auf Scherung beanspruchte. Wir fokussieren uns hier auf erstere, denn dort ist das Drehmoment sehr wichtig und auch am schwersten festzulegen.
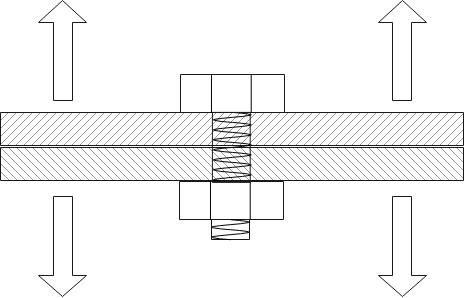

Die Verbindung funktioniert durch ein einfaches Prinzip, das mit Federn vergleichbar ist, die entgegengesetzt arbeiten. Die eingedrehte oder mit einer Mutter gehaltene Schraube wird leicht gedehnt, wodurch eine Zugkraft entsteht. Diese Kraft will die Schraube wieder auf ihre ursprüngliche Länge zusammenziehen. Dabei presst sie die Bauteile aufeinander.
Durch die Klemmung entsteht eine Gegenkraft in den zusammengedrückten Teilen. Das ist die zweite Feder, sie will die Teile auseinander drücken und übt somit eine umgekehrt wirkende Kraft zur Schraube aus. Fertig ist ein System von im Material gespeicherten Kräften die alles zusammenhalten.

Die Klemmkraft
Die Höhe der Klemmkraft wird durch das Maß an Dehnung der Schraube bestimmt. Die Dehnung wird durch das Gewinde erzeugt, das wie eine Rampe arbeitet. Durch die Drehung der Schraube und der erzwungenen Bewegung entlang der „Gewinderampe“ dehnt sie sich und es entsteht die Zugkraft im Material, aus der die Klemmkraft resultiert. Um die Klemmkraft durch Dehnung der Schraube zu erzeugen, müsst ihr eine Kraft aufbringen. Diese Kraft ist sehr viel größer, als zur Dehnung der Schraube benötigt wird, da es viele Verluste gibt.
Es gibt steile und weniger Steile „Rampen“, sprich Gewindesteigungen. Je steiler die Steigung ist, je leichter und schneller ist die Schraube einzudrehen und je leichter löst sie sich auch wieder. Die Selbsthemmung über die Reibung der Gewindeflächen, die letztendlich für den dauerhaften Halt sorgt, ist geringer als bei einer weniger steilen Gewindesteigung. Das kann sich jeder leicht bildlich vorstellen. Eine Kiste rutscht eine steile Rampe leichter und schneller runter als auf einer flachen Rampe. Gerade hoch belastete Schrauben haben ein weniger steiles Gewinde, ein sogenanntes Feingewinde. Dort wird die Steigung mit dem Nenndurchmesser angegeben, wie beispielsweise „M8 x 0,25“ oder „M8 x 0,50“. Im Unterschied zum Regelgewinde, bei der eine Schraube „M8“ eine Steigung von 1,25 hat. Die Steigung gibt den Abstand zweier benachbarter Windungen in Millimeter an.
Wichtig zu wissen ist, dass eine korrekt erstellte Schraubverbindung, auf die keine anderen Faktoren einwirken, keine zusätzliche Sicherungsmaßnahmen benötigt. Die Selbsthemmung durch Gewinde und Kopf reichen vollkommen aus. Mehr dazu später unter den zusätzlichen Sicherungsmaßnahmen.
Wichtige Kenndaten einer Schraube

Jede Schraube hat einen elastischen Bereich. Wird sie innerhalb dieses elastischen Bereichs gedehnt, kehrt sie immer wieder nach der Entlastung auf ihre Ursprüngliche Länge zurück. Die Grenze, ab der die Schraube sich plastisch (dauerhaft) verformt, ist die Streckgrenze (bei vergüteten Stählen mit anderen Eigenschaften in diesem Bereich Dehngrenze genannt). Das Drehmoment einer Schraube wird vom Hersteller bei ca. 65% bis 75% unterhalb dieser Grenze festgelegt. So besteht noch Luft nach oben. Das ist gerade dann wichtig, wenn im Betriebszustand weitere Kräfte die Schraube auf Zug belasten. Im elastischen Bereich kann die Schraube im Grunde immer wieder festgezogen und gelöst werden, ohne Einbußen zu haben. Allerdings, wenn dies sehr, sehr oft passiert, ist das vergleichbar mit einer zyklischen Last und kann langfristig zu einem Ermüdungsbruch führen.
Wenn ihr nun über die Streckgrenze hinaus dreht, verformt sich die Schraube dauerhaft. Nach dem Lösen kehrt sie nicht mehr zu ihrer ursprünglichen Länge zurück. Wichtig an dieser Stelle ist es zu wissen, dass solange die Last anliegt, erzeugt die Schraube weiterhin die gewünschte Klemmkraft. Diesen Effekt macht man sich bei Dehnschrauben zu nutze.
Dann folgt die Zugkraftgrenze. Darüber hinaus ist selbst bei gewollt gedehnten Schrauben (Dehnschrauben) keine bessere Verbindung mehr zu erzielen. Die Schraube dehnt sich nur weiter ohne die Klemmkraft zu erhöhen. Ab jetzt kann die Schraube anfangen sich einzuschnüren, d.h. sie wird an bestimmten Stellen dünner. Die Spannung in der Schraube nimmt ab. Als letztes erfolgt dann der Abriss und die Zerstörung der Schraube.
Dehnschrauben
Schrauber kennen Dehnschrauben von Zylinderköpfen. Und die sind auch ein gutes Beispiel für den Einsatz von Dehnschrauben. Sie kommen dort zum Einsatz, wo es an Platz mangelt, um Klemmkräfte zu erreichen, die einen größeren Durchmesser benötigen. Mit anderen Worten, Dehnschrauben sind hochfeste Schrauben und sie machen das gleiche wie andere Schraubverbindungen, nur mit einem kleineren Durchmesser im Bereich des Schafts, der ohne Gewinde ist.
Sie funktionieren genau so wie normale Schrauben. Sie werden durchaus bis in den plastischen Bereich angezogen und erlangen so materialbedingt hohe Festigkeiten. So erreichen sie die geforderten Klemmkräfte, bei geringerem Durchmesser. Sie sind selbstsichernd und unempfindlicher gegen Zugspannungverlust bei Setzungen.
Solange sie beansprucht werden, also Zug auf ihnen lastet ist das kein Problem, sie entwickeln die gewollte Klemmkraft und halten sie. Wird die Last durch Herausdrehen reduziert, bleiben sie gelängt und können die geforderten Klemmkräfte nicht erneut erzeugen. Deshalb müssen Dehnschrauben nach der einmaligen Benutzung ersetzt werden.
Das besondere bzw. die Nachteile an ihnen sind, dass sie zum einen sehr sorgfältig und meistens unter Verwendung zweier Angaben angezogen werden müssen. Für die erste Angabe gibt es in vielen Werkzeugkästen das richtige Werkzeug: den Drehmomentschlüssel. Bei der zweiten Angabe wird es schon schwieriger, denn das ist meistens ein Winkel. So können die Vorgaben z.B. sein, dass in mehreren Durchgängen verschiedene Drehmomente angelegt werden müssen, um dann die Schraube noch einmal um einige Grad weiter zu drehen. Und das sollte ziemlich genau erfolgen. Der andere Nachteil ist eben die einmalige Verwendung bei vergleichsweise hohen Kosten.
Das Drehmoment
Kommen wir jetzt zum A und O einer geschraubten Verbindung. Es klang eingangs schon an: die Klemmkraft. Das richtige Drehmoment ist essentiell, diese zu erreichen und zu erhalten. Wir wissen bereits, dass die Klemmkraft durch die Dehnung der Schraube entsteht. Diese Dehnung erzeugt ihr beim Festdrehen durch das Einbringen von Kraft, dem Drehmoment. Während es für den Schraubenhersteller ein leichtes ist, das Drehmoment seiner Schraube zu bestimmen, hat der Konstrukteur, der die richtige Schraube für seinen Zweck finden muss, mit vielen unbekannten Variablen zu kämpfen.

Was ist das Drehmoment?
Das Drehmoment ist eine Bewegungskraft, die drehend auf ein Zentrum wirkt. Es ist eine Funktion der Kraft F und des Radius r. Der Radius ist nichts anderes als die Länge des Hebels, mit dem das Drehmoment erzeugt wird. Daher ist es nicht egal, wo ihr am Drehmomentschlüssel anpackt und drückt. Aber darauf gehen wir im zweiten Teil zur Praxis näher ein.
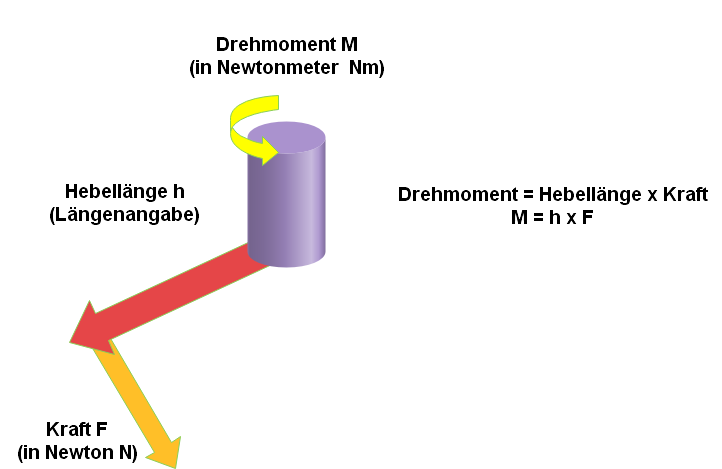
Warum ist die Sache mit dem Drehmoment so schwierig?
Es gibt technische Bereiche wo die Lasten und das Risiko gering sind. Und es gibt Bereiche, denke man nur mal an die Luftfahrt oder kritische Industrieanlagen, wo hochbelastete und kritische Verbindungen bestehen. Dort kann man sich keine wagen Abschätzungen oder eine schlechte Montage erlauben. In solchen Bereichen besteht sogar eine Dokumentationspflicht für das Anziehen von Schrauben. Heutzutage wird das durch sehr teure elektronische Schlüssel unterstützt, die den gesamten Schraubvorgang protokollieren. Hier müssen die Konstrukteure und Monteure sehr gewissenhaft arbeiten.
Überall lauern Ungewissheiten
Typischerweise wird davon ausgegangen, dass nur ca. 10% der eingebrachten Kraft als Längendehnung in der Verbindung verbleiben. Geschätzt verschwindet 90% der Kraft als Wärme. Diese entsteht durch Reibung. Einige der Reibungsfaktoren können quantifiziert werden, andere sind lediglich bekannt. So gibt es einen Effekt, dass sich bei neuen Schrauben die Oberflächen bildlich gesprochen gegenseitig „abschleifen“. Das bedeutet, dass sich beim ersten Eindrehen die reibenden Oberflächen von Schraube und Gewindeloch bzw. Mutter zunächst glätten und so ihren Reibungskoeffizienten verändern. Ein Punkt auf den wir später noch zurück kommen werden, wenn es um die Praxis geht.
Weiter geht es mit seitlichen Belastungen die auf die Schraube wirken und sich so auf die resultierende Reibung auswirken. Auch die Genauigkeit und Form mit der die Gewinde gefertigt wurden unterliegen Schwankungen, die sich ebenfalls auf die resultierende Kontaktfläche und somit wieder auf die Reibung auswirken.
Aber das sind nicht die einzigen Dinge, die zur Ungenauigkeit beitragen. Zahlreiche Effekte, die als Setzen (Relaxation) bezeichnet werden, können in der Praxis wirken. Das ist beispielsweise der Fall, wenn zwei Teile durch mehrere Schrauben verklemmt werden und das Anziehen der nächsten Schraube durch Setzungen die vorherigen Schrauben entspannen. Ein Versuch des Instituts für Werkzeugmaschinen und Betriebswissenschaften der Technischen Universität München hat gezeigt, dass die resultierenden Drehmomente dabei bis zu 30% auseinander liegen können.
Ein weiteres Beispiel sind Verbindungen, in denen Dichtungen vorhanden sind. Diese können der Pressung nachgeben und auf diese Art die Schrauben entspannen. Wurde die Kombination Schraube/Drehmonent so gewählt, dass dann die Klemmkraft nicht mehr reicht, löst sich die Verbindung.
Aus diesen Gründen findet ihr oft in den Werkstatthandbüchern die Anweisung, in mehreren Durchgängen verschiedene Drehmomente anzubringen und bei mehreren Schrauben in bestimmten Reihenfolgen anzuziehen. Die meisten kennen das von den Radbolzen bzw. Radmuttern, die sternförmig angezogen werden sollen. Das soll u.a. ein späteres Setzen verhindern und ein möglichst gleichmäßiges Drehmoment über alle Schrauben einer Verbindung ermöglichen, denn das ist wichtig.
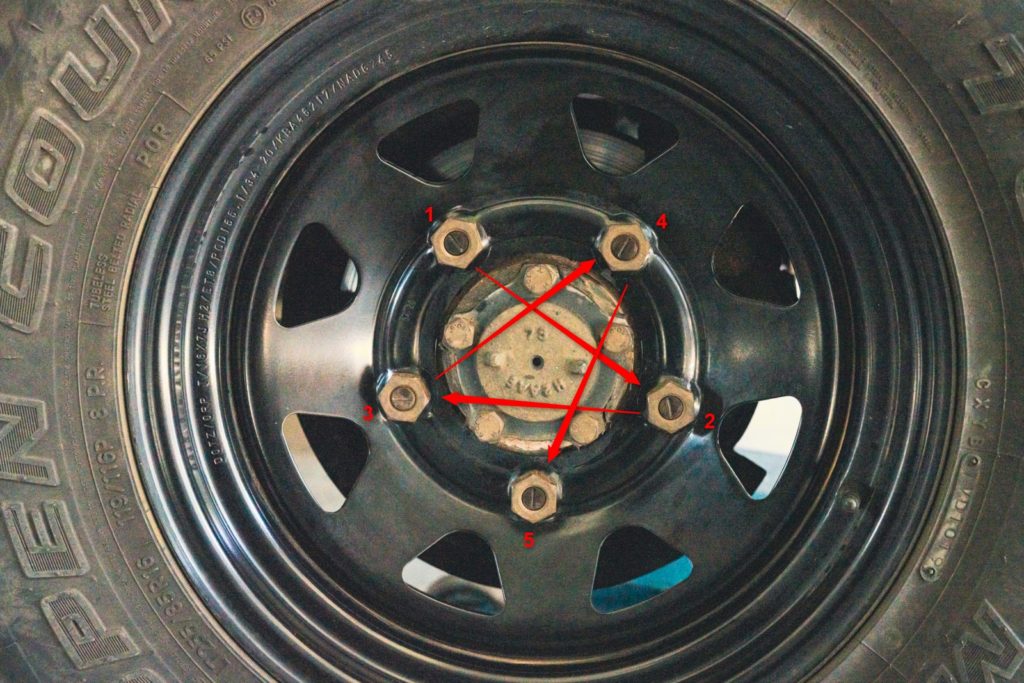
Wenn ihr mit dem Drehmomentschlüssel eine Schraube festzieht, dann „spürt“ der Drehmomentschlüssel die Summe aller Widerstände und er klickt wenn er das eingestellte Drehmoment erreicht. Egal wieviel von der Kraft dann für die Dehnung aufgewendet wird und wieviel davon als Reibungswärme verschwindet.
Das alles wäre gar kein Problem, wenn die tatsächlich eingebrachten Vorspannkräfte exakt zugeordnet werden könnten. Das können aber die bestehenden Messverfahren nicht, schon gar nicht ein Drehmomentschlüssel. Das Drehmoment kann so nur indirekt ermittelt werden und es gibt immer Streuungen.
Im Betrieb kommen weitere Unwägbarkeiten hinzu
Damit wären aber auch erst die Effekte angesprochen, die der Verarbeitung und der Montage geschuldet sind. Im Betrieb geht es dann munter weiter. Dort wirken möglicherweise sich ändernde Lasten, deren Größe hoffentlich bekannt sind. Das kann zu einer Überdehnung der Schraube in den plastischen Bereich oder gar bis zum Bruch führen. Oder umgekehrt, zu einer ungewollten Entlastung, so dass die Teile sich gegeneinander bewegen können. Letzteres endet dann in losgerüttelten Schrauben.
Man hilft sich mit Überdimensionierung und Bereichen
Daher ist es üblich, gerade hochfeste Schraubverbindungen, um den Faktor 2,5 größer zu dimensionieren, um ja im sicheren Bereich zu bleiben. Das geforderte Anzugsdrehmoment wird dann an den Anfang eines Drehmomentfensters gelegt, innerhalb dessen die Verbindung sicher ist und die Unschärfen aufgefangen werden.
Ihr seht, einiges kann der Konstrukteur vorhersehen, vieles nicht und schon gar nicht, wie und womit ihr die Montage durchführt. Und letzteres ist mit einer der entscheidenden Faktoren für die Haltbarkeit einer korrekt dimensionierten Verbindung.

Beispiel einer Dimensionierung
Das folgende zeigt einen üblichen Ansatz, wie Konstrukteure die richtige Schraube für ihren Zweck suchen. Ausgangspunkt ist die Zugkraftgrenze, von der heruntergerechnet wird. Auf sie folgt ein Bereich von ca. 15% der vollkommen unbrauchbar ist, da er zwischen der Streckgrenze und dem Bruch liegt. Der Bereich in dem die Dehnung stattfindet und für Verluste durch Torsion der Schraube wurden jeweils 5% veranschlagt. 6% setzt der Konstrukteur noch für die Belastungsgrenze seiner Teile an und gibt noch einen Sicherheitsfaktor von 4% dazu. Er ist kleiner als der untere Sicherheitsfaktor, da er lieber mehr Klemmkraft haben möchte, als zu wenig. Dann folgt das gesuchte Fenster von gut 14%. In diesem liegt das gesuchte Drehmoment, dass ihr später erreichen müsst. Dann folgt der untere Sicherheitsfaktor mit 7%. Die minimale Klemmkraft macht einen Bereich von 12% aus. Sie ist mindestens nötig, um Vibrationen, Undichtigkeiten oder Ermüdung zu verhindern. Die ersten 30% sind dann wieder nicht zu nutzen, da sie zu wenig Klemmkraft bedeuten.
Anzugsverfahren für das Drehmoment
Dem Anzugsverfahren kommt daher bei der genauen Montage eine große Rolle zu, damit sich die unvermeidbaren Unschärfen in Grenzen halten. Für den privaten und auch im Werkstattbereich kommen, schon aus wirtschaftlichen Gründen heraus, nur zwei Anzugsverfahren zum Tragen: Drehmoment und Drehwinkel. Das Drehmomentverfahren dürfte das üblichste sein. Dabei wirkt der Anzugswiderstand und wenn dieser den eingestellten Wert überschreitet gibt der Schlüssel ein Signal.
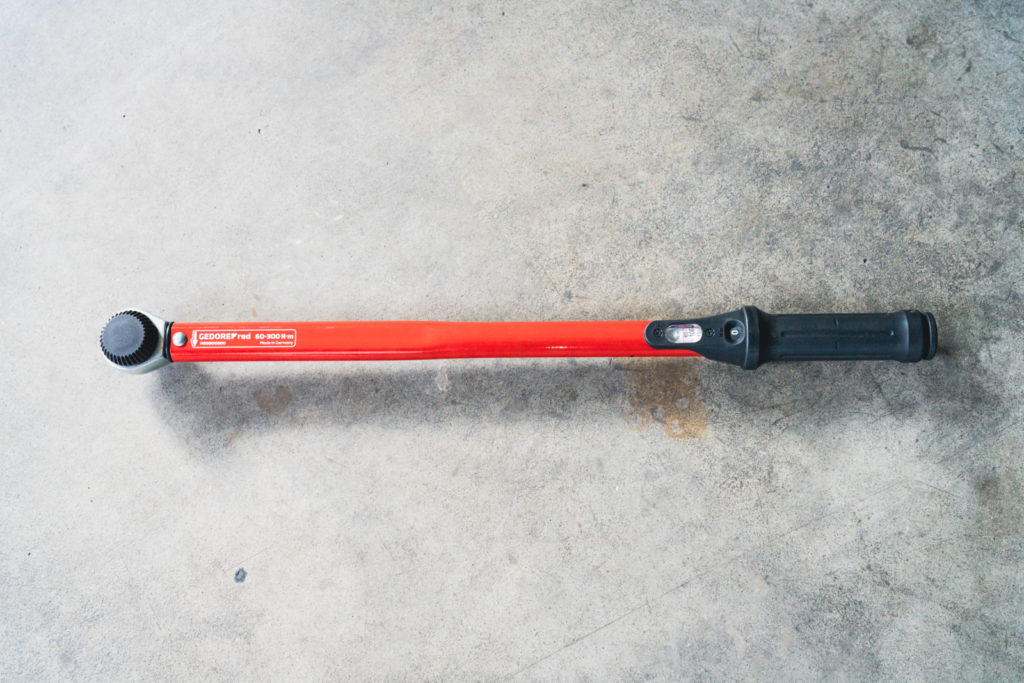
Bei mechanischen Schlüsseln ist das ein Knacken und bei elektronischen kann das eine Leuchte oder ein Signalton sein. Bei diesem Verfahren liegt der mögliche Fehler bei gut +/- 25%. Da hierbei die Reibwiderstände einen Einfluss auf das Ergebnis haben, ist es besser diese zu reduzieren um den Fehler möglichst klein zu halten, aber darauf kommen wir im Praxis-Artikel zurück.
Beim Drehwinkelverfahren wird unabhängig von Reibwiderständen nur der gedrehte Winkel gemessen. Dadurch ergibt sich ziemlich genau das Maß an Dehnung aus der bekannten Steigung des Gewindes. Das klingt jetzt ersteinmal so, als wäre das das ideale Verfahren, da ja die Unberechenbarkeiten der Reibung außen vor bleiben. Leider ist dem nicht ganz so, denn für ein reproduzierbar-gleichmässiges und gleich gutes Ergebnis muss ja der Start der Winkelmessung immer der gleiche sein.
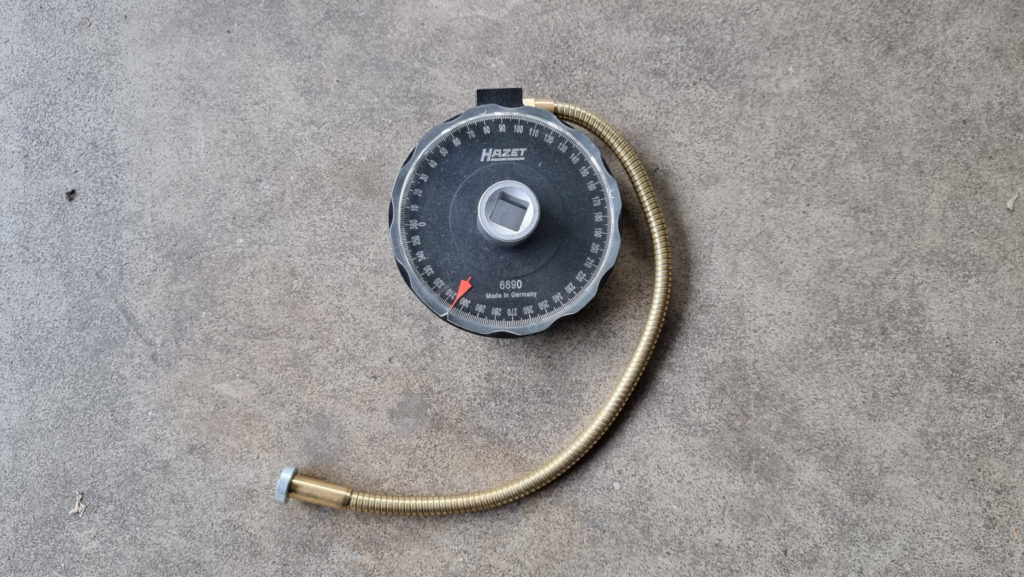
Der Punkt an dem die Winkelmessung beginnen soll ist der sogenannte Fügemoment. Er ist definiert als der Moment, ab dem der Drehmomentanstieg und Drehung zueinander linear verlaufen. Das ist dann der Fall, wenn der Schraubenkopf vollflächig aufliegt und die anfänglichen Setzprozesse beendet sind. Mit anderen Worten, ihr müsst auch bei der Winkelmessung zuerst mit einem Drehmomentschlüssel beginnen. Kombinierte elektronische Drehmoment-Drehwinkelschlüssel erkennen den Fügemoment und zeigen diesen Punkt an. Aber ohne diese teuren Kombi-Schlüssel, die bei gut 1.500 Euro losgehen, ist es nahezu unmöglich, den Fügemoment selbst zu ermitteln. Dann bleibt euch nur übrig, sich genau an die Anweisungen des Werkstatthandbuchs zu halten und mit den Ungenauigkeiten zu leben. Deshalb sind in den Angaben zuerst ein oder zwei Drehmomente angegeben und dann Winkelangaben.
Warum Schraubverbindungen versagen
Bisher bewegten wir uns in einer idealen Welt. Tolle Schrauben, tolle Muttern, perfekte Gewinde, präzisestes Werkzeug, ein Drehmoment im sicheren 65%-Bereich und eine 100% richtig durchgeführte Montage. Und dann wurden wir wach und mussten feststellen, dass die Realität anders aussieht. Und dennoch halten unsere Fahrzeuge zusammen und die Anbauteile bleiben auch dran. Meistens. Also kein Grund sich Sorgen zu machen, nur einer sorgfältig zu bleiben. Was ist aber der Grund, dass sich Schraubverbindungen lösen?
Rufen wir uns noch einmal in Erinnerung, dass das entscheidende Kriterium für das Halten einer geschraubten Verbindung die Klemmkraft ist. Das Drehmoment erzeugt die Klemmkraft, aber im Betrieb kommen weitere Faktoren hinzu, die die Klemmkraft verändern. Und diese hält letztendlich alles zusammen. Gehen wir zusammen einmal die Gründe durch, weshalb sich Schrauben lösen.
Zu geringe Klemmkraft
Die Erfahrung von Experten, wie John H. Bickford, Maschinenbauingenieur und Autor des Referenzhandbuchs für die Wartung von Nuklearanlagen und vieler weiterer Publikationen zum Thema Schrauben, besagt, dass der häufigste Grund für das Versagen von Schraubverbindungen zu geringe Klemmkraft ist. Und das kann, neben zu wenig Drehmoment beim Anziehen, viele Ursachen haben, von denen wir einige aufzeigen.
Verarbeitungsqualität
Die Qualität der Verbindung hängt auch von der Qualität der Gewinde ab. Nicht sauber oder schräg geschnittene Gewinde führen zum einen zum falschen Drehmoment und können zum anderen die benötige Kontaktfläche reduzieren. Bei einem schräg geschnittenen Gewinde liegt der Schraubenkopf oder die Mutter nicht plan auf, was zum einen die Reibfläche verringert und zum anderen die Schraube ungewollten seitlichen Kräften aussetzt.
Selbstlösen
Das Selbstlösen einer Schraube führt entweder zu einer losen oder zu einer verlorenen Schraube und dem kompletten Versagen der Verbindung. Letzteres sollte auf keinen Fall passieren. Das folgende Bild zeigt die Folgen solch eines Versagens. Zuerst lösten sich die Radmuttern ohne das sie verloren gingen, was anhand er gefundenen Radbolzen festgestellt werden konnte. Die Muttern saßen noch auf den Bolzen. Die Felge hat aber dadurch so viel Spiel bekommen, dass sie die Radbolzen abscheren konnte.
Dieses Versagen einer geschraubten Verbindung ist eine der häufigsten Ursachen. Und einer der kompliziertesten Prozesse in einer Verbindung. Die grundlegende Ursache ist zu wenig Zugspannung in der Schraube. Schuld daran können verschiedene Umstände sein: Zu geringes Drehmoment beim Festschrauben, Leckagen im Bereich der Verschraubung, relative Bewegungen der Bauteile und Vibrationen.
Gerade mit Vibrationen ist bei Fahrzeugen zu rechnen. Vergleichsweise wenig Material der Gewinde von Schraube und Gewindeloch haben Kontakt miteinander. Nur gut 15% bis 20%, schlimmer noch, wenn das Material ungenau ist. Das lässt Raum für Spiel und fördert das Losrütteln.
Korrosion
Auch Korrosion kann durch zu geringe Klemmkraft hervorgerufen werden. Ist sie nicht hoch genug, gerade bei Flächen die korrosive Stoffe abdichten sollen, können diese in die Schraubverbindung eindringen und den zerstörerischen Prozess starten.
Ermüdung
Es mag komisch klingen, aber Ermüdungsbrüche entstehen seltener durch zu festes, als eher durch zu loses Anziehen. Es ist leider eine Eigenschaft von Metallen, bei zyklischen Zugbeanspruchungen, selbst wenn sie weit genug unter der Streckgrenze liegen, urplötzlich aufzugeben. Der Grund, dass die Last zyklisch wirken kann, ist, dass durch zu loses Anziehen, die Verbindung nicht die Klemmkraft und Festigkeit aufbaut, die sie benötigt. Geht das soweit, dass die Bauteile sich gegeneinander bewegen können, entstehen zyklische Lasten. Diese machen das Material über die Zeit mürbe. Die Folge ist ein Ermüdungsbruch.
Dabei werden in der Regel vier Stadien durchschritten: 1. Rissbildung – durch Beschädigungen, Korrosion, Hitze oder Materialeinschluss (bei der Produktion) oder eben zyklischen Stress. Dann folgt 2. Rissausdehnung – Der ursprüngliche Riss sorgt für eine Konzentration von Stress im Material, so dass weitere Bereiche reißen. 3. Das verbliebene Material bekommt den gesamten Stress ab und wird umso mehr belastet, so dass 4. als letztes der Abriss erfolgt.
Werden Teile nur durch eine Schraube zusammengehalten, ist das schon das Ende dieser Verbindung. Werden sie durch mehrere Schrauben gehalten, kann sich die Klemmkraft so verändern, dass sich auch die anderen Schrauben lösen oder übermäßig beansprucht werden. Der Fehler kann sich ausweiten.
Bei geringen zyklischen Zuglasten ist die Anzahl der Zyklen bis zum Bruch sehr hoch und können mehrere Millionen Zyklen beinhalten. Bei hohen zyklischen Zuglasten können sehr wenige bis einig tausend Zyklen reichen, um zur Zerstörung zu führen. Ein wesentlicher Faktor für die Unempfindlichkeit ist die der Form. Schrauben besitzen eine eher ungünstige Form und erreichen bei Stresstests nur ungefähr 10% der Haltbarkeit gegen zyklische Lasten, als ihr Material grundsätzlich in der Lage wäre auszuhalten.

Rollen ist besser als Schneiden
Gewinde, die in die Schraube gerollt bzw. gewälzt werden und die gerundete Radien am Gewindegrund haben, sind langlebiger, da geschnittene Gewinde und scharfe Winkel anfälliger für Stadium 1 Rissbildung sind. Der Grund dafür liegt innerhalb des Materials. Beim Gewindeschneiden wird der Verlauf des Material unterbrochen, beim Rollen bzw. Wälzen wird das Material zusätzlich Kaltverfestigt.
Industriell gefertigte Schrauben sind nahezu alle gerollt bzw. gewälzt. Geschnittene, also im spanabhebenden Verfahren hergestellt, kommen nur bei kleinen Serien vor oder in der privaten Anwendung.
Zu fest angezogen
Das Gegenteil der zu losen Verbindung ist die zu feste Verbindung, auch wenn sie eher selten zu finden ist. Eine zu fest angezogene Schraube kann indirekt oder direkt zu einem Fehler führen. Indirekt beispielsweise in dem durch zu hohen Druck eine Dichtung beschädigt wird und eine Leckage auftritt, die wiederum zu einer losen Schraube führt. Ein direktes Versagen kann durch ein Ausreissen des Gewindes oder eine Beschädigung der Verbindungsflächen passieren
Des Weiteren kann Spannungsrisskorrosion eintreten. Auf Zug beanspruchte Metalle können kleinste Risse bekommen. Dringt in diese ein Elektrolyt wie Wasser ein, beginnt eine Korrosion, die letztendlich im Versagen der Schraube endet.
Alles was nicht offensichtlich mit der Verbindung passiert ist leider auch nicht immer direkt zu erkennen und daher erst mit dem Folgeschaden zu erkennen.
Abriss
Im Grunde ist der Abriss auch ein Problem des zu festen Anziehens, aber wir setzen das hier separat, da er sofort zu erkennen ist. Bei einer intakten Schraube muss man sich aber schon Mühe geben, diese abzureißen, denn in den meisten Fällen, durchläuft sie vor dem Abriss noch die plastische Verformung und dort ist bereits die Abnahme des Widerstand gegen das Anziehen zu spüren. Der Pufferbereich bei Schrauben der Festigkeitsklassen (siehe unten) 10.9 und 12.9 ist kleiner, als beispielsweise bei der Klasse 8.8. Bei genügend Kraft seid ihr schneller am Zugkraftpunkt oder darüber hinaus. Ist der Hebel und die eingebrachte Kraft also groß genug, kann einen der Abriss durchaus überraschen.
Gefährlicher sind da alte, strukturell schon geschädigte Schrauben, die schon bei geringeren Kräften als zu erwarten aufgeben. Deshalb nötigenfalls ersetzen. Bei der Montage müsst ihr darauf acht geben, dass ihr euch nicht durch das urplötzliche Lösen verletzt, weil ihr mit dem Schlüssel in der Hand in irgendein scharfes Teil rauscht.
Ausriss
Es ist natürlich auch ein Ausriss durch zu festes Anziehen möglich, bei dem die Schraube das gegenüberliegend Gewinde zerstört. Das passiert insbesondere dort, wo Stahlschrauben in weichere Materialien wie Aluminium geschraubt werden.
Im Automobil-Bereich dürften herstellerseitig primär die selbstlösenden Schrauben ein Thema darstellen, bedingt durch Vibration oder Leckage.
Wo bekommt ihr das richtige Drehmoment her?
Wer ein Werkstatthandbuch hat, kann dort nachsehen. Und wenn es dort nicht steht, oder für Dinge außerhalb eures Fahrzeugs?
Auch da könnt ihr Euch behelfen. Es gibt es Tabellen aus denen das Anzugsdrehmoment für den jeweiligen Schraubentyp abgelesen werden kann. Dazu müsst ihr ein paar Angaben über eure Schraube wissen.
Die Angaben auf einer Schraube
Auf Schraubenköpfen steht eine Angabe zur Festigkeitsklasse, z.B. „8.8“ oder „10.9“. Manchmal ist auch „12.9“ im automobilen Sektor anzutreffen. Sehen wir uns diese drei häufigsten Klassen genauer an.
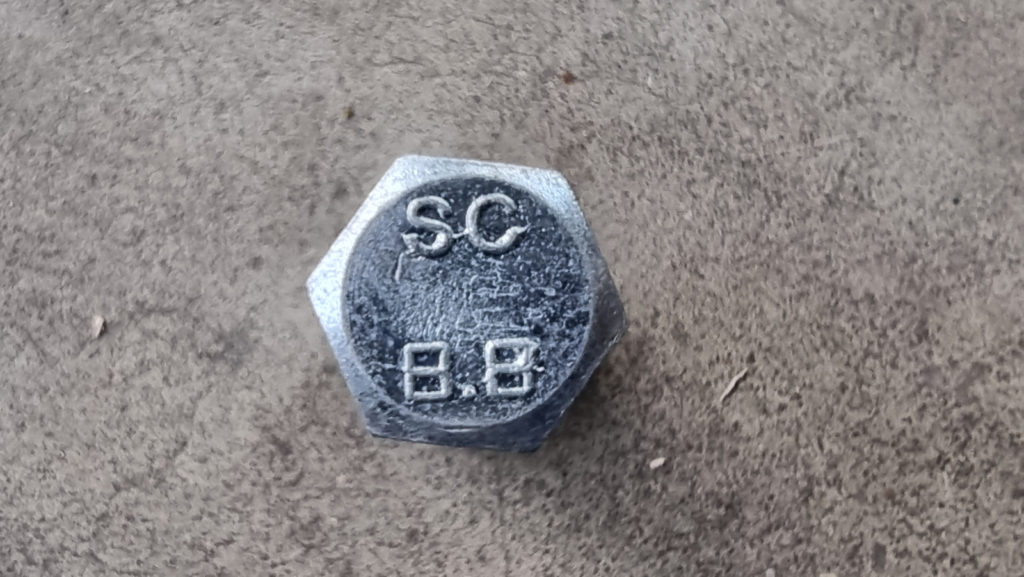
Die Angaben auf der Schraube sind gerundet und geben die Zugfestigkeit und die Streckgrenze an. Diese Begriffe haben wir ja oben bereits erklärt.
Die erste Zahl entspricht 1% der Zugfestigkeit. Sie muss also mit 100 multipliziert werden, dann bekommt ihr den Punkt ab wann die Schraube ihre maximale Belastungsgrenze erreicht hat. Die Angabe erfolgt in Megapascal (MPa) und ein MPa entspricht 1 N/mm2, was circa 100 Gramm pro mm2 entspricht.
Die Zahl hinter dem Punkt gibt das Verhältnis von Zugfestigkeit und Streckgrenze mit 10 multipliziert an. Oder anders gesagt, bei wieviel Prozent der Zugfestigkeit die Streckgrenze liegt. Bei einer 8.8-Schraube ist die Zugfestigkeit 800 MPa und die Streckgrenze wird bei 80% der Zugfestigkeit erreicht, also bei 640 MPa.
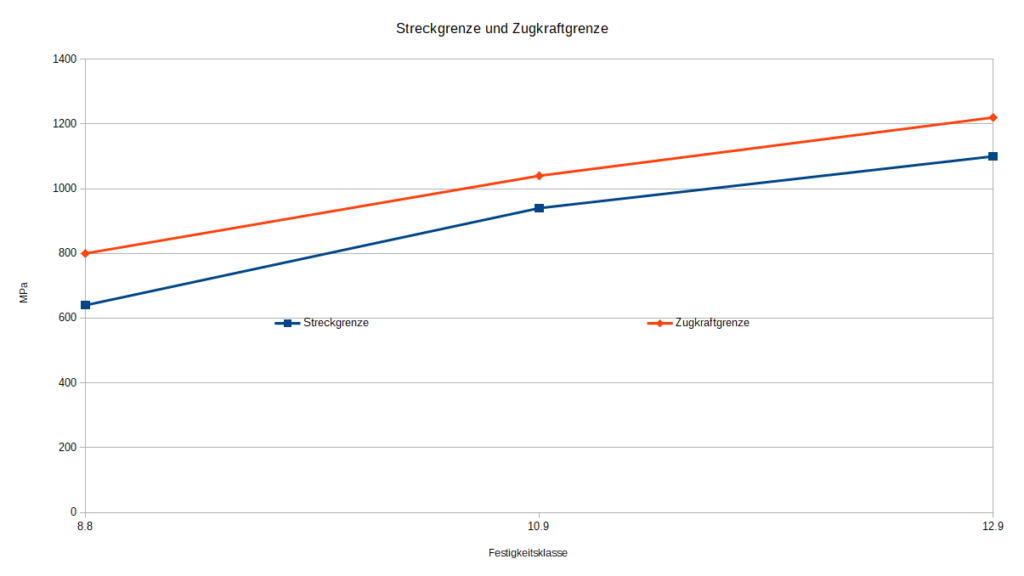
Mit den Angaben zur Festigkeitsklasse und dem Nenndurchmesser, beispielsweise „M6“ für 6 mm oder „M10“ für 10 mm, bei metrischen Schrauben, könnt ihr dann in Tabellen nachsehen und das empfohlene Anzugsdrehmoment ablesen. Diese können voneinander abweichen. So finden sich für M12 mit 10.9 Festigkeitsklasse Werte von 109 Nm bis 121 Nm. Woher kommen diese Unterschiede? Einmal spielt die Kopfform eine Rolle, also handelt es sich um eine Sechskantschraube oder beispielsweise um eine Innensechskantschraube? Weitere wichtige Faktoren sind die Steigung des Gewindes, der den Reibwinkel ergibt und natürlich das Material, z.B. Stahl oder Edelstahl. Dann kommt noch die Oberflächenbeschichtung dazu. Nackter Stahl, verzinkt usw.
Zusätzliche Sicherungsmaßnahmen
Man kann ja nie sicher genug sein, ist oft das Motto. Daher versehen Schrauber ihre Schrauben oft mit zusätzlichen Sicherungsmaßnahmen. Ist das nötig? Ja, das kann trotz allem durchaus gesagt werden.
Eine korrekt ausgeführte Schraubverbindung hält von alleine. Allerdings haben wir auch beschrieben, dass im Einsatz zahlreiche unbekannte Faktoren und unvorhergesehenes Einfluss nehmen können, wie beispielsweise eine Undichtigkeit oder extrem starke Vibrationen. Insofern ist es durchaus sinnvoll Vorkehrungen zu treffen. Dabei möchten wir zwischen zwei Prinzipien unterscheiden: a) Sicherung gegen Klemmkraftverlust, also das Lösen und b) Sicherung gegen Verlust der Schraube.
Ersteres ist natürlich das wichtigste, wir möchten erst gar nicht, dass sich die Verbindung überhaupt löst. Letzteres kann aber die letzte Sicherung vor dem Verlust eines Teiles sein und dem Auseinanderfallen sein.
Und dann gibt es auch noch Sicherungen, die unnötig oder sogar kontraproduktiv sind. Gehen wir die bekannten Vertreter einmal durch.
Sicherungslacke / flüssige Schraubensicherung
Diese Lacke, allgemein auch Schraubensicherung oder Flüssigsicherung genannt, wirken wie ein Klebstoff, der ein Herausdrehen der Schraube verhindern soll. Wenn ihr Schraubensicherungen nutzen wollt, die auch die Reibung reduzieren, dann müssen die Gewinde trocken und fettfrei sein.
Das Prinzip dieser Schraubensicherungen sind stark anhaftende Polymere, die die Zwischenräume in der Gewindeverbindung füllen. Zum einen fungieren sie als Klebstoff und zum anderen verhindern sie Bewegungen innerhalb des Gewindes. Deshalb eignen sich flüssige Schraubensicherungen insbesondere beim Auftreten von Vibrationen.
Übrigens, einige Schraubensicherungen funktionieren auch bei leicht geölten Oberflächen, wie z.B. das Liqui Moly 3801.
Die richtige flüssige Schraubensicherung finden
Wie kann es auch anders sein? Auch hier ist es nicht egal, was ihr wo verwendet. Es gibt bei den flüssigen Schraubensicherungen mehrere Festigkeiten und Viskositäten. Das sind die wesentlichen Unterscheidungsmerkmale. Dann gibt es noch Sicherungen die vor der Montage auf das Gewinde aufgetragen werden oder welche die durch Kapillarwirkungen nachträglich einziehen. Meistens werdet ihr wohl den Kleber für vor der Montage benutzen. Bleibt also die Festigkeit und die Viskosität.
Üblicherweise gibt es drei Festigkeiten: gering, mittel und hochfest. Im Zweifel nehmt die mittelfeste Variante. Bei den Viskositäten gilt, dass niedrig-viskose Produkte sich besser für kleine Nenndurchmesser und feine Gewinde eignen. Höher-viskose Schraubensicherungen sind für große Schrauben und normale Gewinde geeignet. Gut sind auch thixotrope Stoffe. Sie bleiben während des Drehens niedrigviskos und werden steifer wenn die Schraube ruht. Ein bekannter Vertreter einer mittelfesten thixotropen Sicherung ist Loctite 243.
Sicherungsmuttern
Die bekannten Sicherungsmuttern mit Nylonring sind wohl die bekanntesten Vertreter, aber es gibt viele Arten und Formen. Sie sind was den Erhalt der Klemmkraft angeht eher wenig nützlich. Die Hauptlast bleibt hier bei der Selbsthemmung des Gewindes. Die Sicherungsmutter dient jedoch dazu, dass falls sich die Verbindung durch andere Einflüsse löst, ein vollständiges Auseinanderfallen zu verhindern. Kurz gesagt, ihr gewinnt Zeit, um bei regelmäßigen Inspektionen das Problem festzustellen, bevor sich ein Teil plötzlich losgelöst von Eurem Fahrzeug auf der Autobahn befindet.
In den Inspektionsvorgaben zahlreicher Fahrzeuge stehen deshalb Sätze wie „Befestigungselemente von Lenkgetriebe sowie Vorder- und Hinterachsaufhängung kontrollieren/festziehen“. Hoffentlich wird das auch überhaupt und richtig durchgeführt.
Federscheiben
Häufig werden Federscheiben als Schraubensicherung benutzt. Genauso häufig wird ihre Funktion aber miss- und ihr Nutzen falsch verstanden.
Zunächst einmal zur Funktion. Die häufige, aber falsche Annahme ist, dass durch die Federwirkung der Scheibe, die Klemmkraft der Schraube erhöht wird. Dazu ist zu sagen, dass die Klemmkraft der Schraube immer um ein Vielfaches höher ist, als die Federscheibe jemals dazu beitragen könnte.
Das Arbeitsprinzip ist ein anderes. Sie funktioniert wie eine Art Keil oder Meißel, der einen Widerstand gegen die öffnende Drehrichtung erzeugt. Schaut ihr euch die abstehenden Kanten der Scheibe an, wo sie durchtrennt ist, erkennt ihr diese Keilform.
Früher wurde sie tatsächlich zur Sicherung von Schraubverbindungen eingesetzt, aber das ist mittlerweile überholt. Auch die diesbezüglichen Normen DIN 137 und DIN 6904 wurden mittlerweile zurückgenommen. Im „Fastener Design Manual“ der NASA , einer Beschreibung zur Auslegung und den Eigenschaften von Schrauben (Fastener), wird es auf den Punkt gebracht. Dort steht, dass Federscheiben zur Sicherung absolut nutzlos sind.
Wie geht es weiter?
Das war der erste Teil um Verständnis für die Komplexität des Themas und die Bedeutung des Drehmoments zu wecken. Im zweiten Teil, der kürzer ist (versprochen), geht es dann um die Auswahl des richtigen Werkzeugs, was ihr überhaupt an Werkzeug braucht und wie ihr es richtig einsetzt.